- ALDとは何か:自己制御型の表面反応を利用して、原子レベルで膜を一層ずつ堆積させる技術です。
- ALDの特徴:原子レベルの精密な膜厚制御である反面、成膜速度が遅い、高真空が必要であり、コストが高いという特徴があります。
- 利用分野:EUVリソグラフィと組み合わせた微細加工、GAA (Gate-All-Around) 構造トランジスタ、積層型3Dデバイスなど、次世代の半導体デバイス製造において、ALDは不可欠な技術となっていきとされています。
半導体前工程の原子層堆積法
半導体の重要性が増す中で、前工程装置は世界的に成長が続いています。
https://optronics-media.com/news/20250414/99245/
特に中国は米中対立もあり、大幅な投資増加が続いています。今後も先端技術を駆使した半導体の需要増加と従来技術による成熟プロセスともにその重要性は増加するとみられています。
今回は成膜工程のALD(原子層堆積法)についての解説となります。
ALD(原子層堆積法)
半導体の前工程とは、シリコンウェハ上にトランジスタや配線などの微細な回路を形成する一連のプロセスのことです。ウェハを素材として、集積回路を作り込んでいく、半導体製造の最も重要な部分と言えます。非常に多くの精密な工程を経て、最終的な半導体チップの機能が決まります。
主な前工程は以下の通りです。
ウェハ準備
シリコンインゴットの製造: 高純度のシリコンを溶解し、種結晶を用いて単結晶のシリコンインゴットを育成します。
- スライス: インゴットを薄い円盤状(ウェハ)にスライスします。
- 研磨: ウェハ表面を平坦かつ滑らかに研磨します。
- 洗浄: ウェハ表面の微細な異物や汚れを徹底的に除去します。
成膜
ウェハ表面に、酸化膜、窒化膜、金属膜など、様々な薄膜を形成します。
- 成膜方法には、CVD(化学気相成長法)、スパッタリング(物理気相成長法)、ALD(原子層堆積法)などがあります。
フォトリソグラフィ
ウェハ表面に感光材(フォトレジスト)を塗布します。
- 回路パターンが描かれたマスク(フォトマスク)を通して紫外線を照射し、レジストにパターンを焼き付けます。
- 現像液で不要なレジストを除去し、ウェハ上に回路パターンを形成します。
エッチング
フォトリソグラフィでパターン形成されたレジストをマスクとして、露出した成膜を除去し、ウェハに回路パターンを転写します。
- エッチングには、液体を用いるウェットエッチングと、プラズマを用いるドライエッチングがあります。
不純物導入(ドーピング)
半導体特性を持たせるために、リンやボロンなどの不純物をウェハ中に注入します。
- イオン注入法などが用いられます。
平坦化(CMP: Chemical Mechanical Polishing)
表面の凹凸をなくし、平坦にするための処理です。
- 化学的な腐食と механическая研磨を同時に行います。
配線形成(メタライゼーション)
形成されたトランジスタなどの素子間を金属配線で接続します。
- スパッタリングなどで金属膜を形成し、フォトリソグラフィとエッチングで配線パターンを作ります。
これらの工程を何度も繰り返し行うことで、複雑な集積回路がウェハ上に形成されます。前工程は、半導体の性能や品質を大きく左右する、非常に重要なプロセスです。
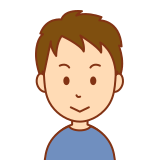
前工程は、細な回路を形成する一連のプロセスのことで、半導体の性能や品質を大きく左右する、非常に重要なプロセスです。
ALD(原子層堆積法)とは何か
原子層堆積(ALD: Atomic Layer Deposition)は、ナノスケールのデバイス製造において非常に重要な薄膜形成技術です。
1. ALDの基礎原理
ALDは、自己制御型の表面反応を利用して、原子レベルで膜を一層ずつ堆積させる技術です。
従来のCVD(Chemical Vapor Deposition)がガスを連続的に供給して化学反応によって膜を形成するのに対し、ALDは以下の4つのステップを繰り返すことで成膜します。
- 前駆体Aの導入: 成膜したい原子を含むガス(プリカーサーまたは前駆体と呼ばれる)を供給し、基板表面に吸着させます。この吸着は自己飽和的で、反応部位がすべて埋まるとそれ以上の吸着は起こりません。
- パージ: 余分な前駆体Aや副生成物を不活性ガス(窒素など)で排気します。
- 前駆体Bの導入: 別のガスを導入し、基板表面に吸着した前駆体Aと反応させ、目的の薄膜を形成します。この反応も自己飽和的です。
- パージ: 余分な前駆体Bや副生成物を排気します。
この1〜4のサイクルを繰り返すことで、原子層レベルでの膜厚制御が可能になります。
メリット
- 原子レベルの精密な膜厚制御: 1サイクルごとに原子1層分の膜を堆積するため、非常に薄い膜(数ナノメートル以下)でも精密な厚さ制御が可能です。
- 優れた均一性(ステップカバレッジ): 複雑な形状や高アスペクト比(縦横比)の構造(例:深い溝、穴、3D NANDメモリのセル)に対しても、非常に均一で段差被覆性に優れた膜を形成できます。これは、自己飽和反応により、ガスの供給が均一であれば膜厚も均一になるためです。
- ピンホールフリー: 膜中に欠陥(ピンホール)が少ない、緻密な膜を形成できます。
- 低温成膜が可能: 熱に弱い基板に対しても高品質な膜を形成できるため、多様な材料への応用が可能です。
- 幅広い材料に対応: 酸化膜、窒化膜、金属膜など、多様な材料の成膜が可能です。
デメリット:
- 成膜速度が遅い: 1サイクルごとにパージのステップが必要なため、他の成膜技術(CVDやスパッタリング)に比べて成膜速度が遅く、大量生産には時間を要する場合があります。
- 高真空が必要: プロセス中に高真空環境を維持する必要があり、装置が複雑になります。
- 前駆体の選択肢が限られる: 成膜したい材料によっては、適切な前駆体がまだ開発されていない場合があります。
- コストが高い: 装置や前駆体が高価な場合があります。
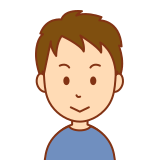
ALDは、自己制御型の表面反応を利用して、原子レベルで膜を一層ずつ堆積させる技術です。原子レベルの精密な膜厚制御が可能であるという特徴から先端技術に利用されています。
ALDはどのような場面で利用されるか
ALDの優れた特徴から、半導体製造のさまざまなプロセスで不可欠な技術となっています。
- ゲート絶縁膜: トランジスタのゲート絶縁膜として、高品質な酸化ハフニウム(HfO2)などのHigh-k(高誘電率)材料の形成に用いられます。デバイスの微細化に伴い、従来の酸化シリコンでは十分な容量が得られなくなったため、High-k材料の導入が不可欠になっています。
- DRAMキャパシタ: DRAM(Dynamic Random Access Memory)のキャパシタの誘電体膜形成に利用され、電荷を蓄える能力を高めています。
- メタルゲート電極: ゲート絶縁膜との整合性の良いメタルゲート電極の形成にも利用されます。
- バリア層/ライナー層: 配線間の電流漏れを防ぐためのバリア層や、配線材料の拡散を防ぐライナー層の形成に適用されます。特に銅配線において、銅の拡散を防ぐためのバリア層(窒化チタン、窒化タンタルなど)は重要です。
- 3D NANDフラッシュメモリ: 3次元構造を持つ3D NANDメモリでは、その複雑な形状に対して均一に膜を形成する必要があるため、ALDが非常に重要な役割を担っています。深いトレンチ(溝)の側壁にも均一に膜を形成できる特性が活かされています。
- 微細配線: ナノスケールの配線において、抵抗率の低いモリブデンなどの金属成膜にもALDが活用されています。
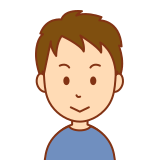
EUVリソグラフィと組み合わせた微細加工、GAA (Gate-All-Around) 構造トランジスタ、積層型3Dデバイスなど、次世代の半導体デバイス製造においては、ALDは不可欠な技術となっていきとされています。
ALDの装置はどのような構成なのか
ALD装置は、主に以下の要素で構成されています。
- リアクター(反応室/チャンバー): ALDプロセスが実際に行われる密閉された空間です。高真空または超高真空状態を維持し、原子レベルでの精密な成膜を可能にするため、気密性が非常に高く設計されています。通常、耐熱性のあるステンレス鋼や石英などの材料で作られています。
- ホットウォール型: リアクター全体を加熱するタイプ。均一な温度分布が得やすい。
- コールドウォール型: 基板のみを加熱し、チャンバー壁は低温に保つタイプ。副生成物の堆積を抑える効果がある。
- プリカーサー供給システム: 成膜したい原子を含む前駆体ガスを供給するシステムです。
- 前駆体容器: 液体または固体の前駆体を貯蔵し、加熱して気化させるための容器。
- マスフローコントローラー(MFC): ガスの流量を精密に制御する装置。
- 高速スイッチングバルブ: 前駆体ガスを瞬時に導入・遮断するためのバルブ。ALDのサイクルプロセスにおいて、前駆体と反応ガスの正確なタイミングでの供給が重要です。ALD専用のバルブは、1億回以上の開閉に耐える高耐久性が求められます。
- 反応ガス供給システム: 前駆体と反応して膜を形成するためのガス(酸化剤、還元剤など)を供給するシステムです。こちらもMFCやバルブを通じて精密に制御されます。
- パージガス供給システム: 各ステップの間に余分なガスや副生成物を排気するための不活性ガス(窒素、アルゴンなど)を供給するシステムです。
- 排気システム: リアクター内のガスを排気し、真空状態を維持するためのシステムです。
- 真空ポンプ: ドライポンプ、ターボ分子ポンプなどが組み合わされて高真空を実現します。
- トラップ: 排気ガス中の未反応ガスや副生成物を捕集し、ポンプや配管の汚染を防ぎます。
- 基板ホルダー(サセプター): 成膜対象であるウェハーを保持する台です。
- 加熱機構: ウェハーを成膜に適した温度に制御するためのヒーターを内蔵しています。
- 回転・傾斜機構: ウェハーを均一に加熱し、ガスに曝すために回転や傾斜機能を備えている場合もあります。
- 温度制御システム: リアクター、プリカーサー容器、ガス配管、基板ホルダーなど、各部の温度を精密に制御します。
- 制御システム: 全てのガス供給、バルブ開閉、温度、圧力、サイクル時間などを自動的に制御するコンピューターシステムです。
ALD装置にはどのような種類があるのか
ALD装置は、その加熱方式やプラズマの利用有無によって、いくつかの種類に分けられます。
- 熱ALD(Thermal ALD):
- 最も基本的なALDプロセスで、熱エネルギーのみを利用して前駆体と表面の反応を促進します。
- 比較的低温で成膜が可能ですが、熱に弱い材料の場合には限界があります。
- 高品質な膜が得やすい反面、プラズマALDに比べて成膜速度が遅い傾向があります。
- プラズマ支援ALD(Plasma-Enhanced ALD; PEALD):
- 前駆体の一部または全部をプラズマで活性化させることで、より低温での成膜や、熱ALDでは難しい材料の成膜を可能にします。
- プラズマの種類(容量結合プラズマ: CCP, 誘導結合プラズマ: ICP, 電子サイクロトロン共鳴プラズマ: ECRなど)によって特性が異なります。
- 熱ALDよりも成膜速度が速い場合があり、膜の特性(密度、屈折率など)を調整しやすいメリットがあります。ただし、プラズマによるダメージのリスクも考慮する必要があります。
- 空間的ALD(Spatial ALD; S-ALD):
- 従来のALDのように時間的に前駆体を交互に供給するのではなく、空間的に分離された複数の領域に前駆体と反応ガスを同時に供給し、基板を移動させることで連続的に成膜する方式です。
- 成膜速度を大幅に向上させることが可能で、大量生産への応用が期待されています。特に、ロール・ツー・ロール(R2R)プロセスなど、大面積基板への成膜に適しています。
どのような装置メーカーがあるのか
半導体分野における主要なALD装置メーカーには、以下のような企業があります。
- ASM International (オランダ): 半導体ALD装置の主要なメーカーの一つで、特にPEALD技術に強みを持っています。
- Applied Materials (米国): 半導体製造装置全般を扱う大手であり、ALD装置も提供しています。
- 東京エレクトロン (日本): 日本を代表する半導体製造装置メーカーで、ALD装置もラインナップしています。
- Beneq (フィンランド): ALD技術のパイオニアの一つで、特に研究開発用途から量産まで幅広いALD装置を提供しています。
- Picosun (フィンランド): ALDの主要な発明者の一人であるスントラ博士が取締役を務めており、ALD技術に歴史のあるメーカーです。
コメント