この記事で分かること
- データ駆動型加工データ統合・活用とは:練工の経験や勘に大きく依存してきた加工技術を、AIやデータ分析技術によって最適化高度化するアプローチのことです。
- どのような取り組みがあるのか:多様な「加工データ」の統合やデータからの「知見抽出と予測」、加工プロセスへの「フィードバックと活用」などの取り組みがあります。
- 多様な「加工データ」の統合とは:様々な異種データを集め、一元的に管理し、統合することであり、多様な加工データを統合し、高度な分析を行うことで、品質改善、生産性向上、コスト削減、そして新たなビジネスモデルの創出に貢献してます。
次世代ものづくり実装研究センター
産業技術総合研究所(産総研)は、2025年4月に「実装研究センター」を新設し、社会課題の解決に向けた技術の社会実装を加速する取り組みを開始しました。
https://www.aist.go.jp/aist_j/news/au20250401_2.html
産総研の第6期中長期目標では、「エネルギー・環境・資源制約への対応」「人口減少・高齢化社会への対応」「レジリエントな社会の実現」の3つの社会課題の解決が掲げられています。
これらの課題に取り組むため、7つの実装研究センターが設立され、所内の研究成果を結集し、産総研の総合力を最大限に生かした研究開発を推進していくとしています。
今回は次世代ものづくり実装研究センターのデータ駆動型加工データ統合・活用の概略と多様な「加工データ」の統合についての解説となります。
次世代ものづくり実装研究センターとは何か
産総研(国立研究開発法人産業技術総合研究所)の次世代ものづくり実装研究センターは、2025年4月に新設された7つの実装研究センターの一つです。
このセンターの主な目的は、以下のような取り組みを通じて、次世代のものづくりシステムを構築し、生産性向上と高度人材の育成を目指すことです。
主な活動内容・研究テーマ:
製造サイバーフィジカルシステム(CPS)の研究開発
- AI技術、DX技術、ロボット技術などを活用し、物理空間と情報空間を高度に融合させた製造システムを構築します。
- ロボットや工作機械、AI、デジタルツインなどを連携させることで、より効率的で高度なものづくりを実現します。
製造技術の知識構造化型データベースの構築
- 製造現場で培われてきたノウハウや加工現象のモデル化、データ化を進め、デジタルものづくりを推進するための基盤を構築します。
データ駆動型加工データ統合・活用
- 加工された材料の特性とミクロ組織との関係性の解明や、加工現象の観察によるモデル化などを通じて、データに基づいた効率的な加工技術を開発します。
ロボットソフトウェアプラットフォームの研究開発
- ロボットの命令系統やプログラム言語をオープンミドルウェアを使って統一・標準化を進め、異種のロボットやシステム間の連携を容易にします。
高機能部材開発
- 形状・材料特性と異分野プロセスを融合させた高機能部材の開発に取り組んでいます。光機能や濡れ性、摩擦特性などの機能制御を目指します。
高度ものづくり人材の育成
- 人口減少や高齢化社会に対応するため、生産性向上と同時に高度なものづくり人材の育成が急務とされており、これにも貢献することを目指しています。
拠点
次世代ものづくり実装研究センターは、以下の3つの研究拠点に設置されています。
- 臨海副都心センター(東京)
- つくばセンター(茨城)
- 北陸デジタルものづくりセンター(石川)
背景と意義
産総研は、研究成果の社会実装を通じて、社会課題の解決と産業競争力の強化を目指しており、この次世代ものづくり実装研究センターは、その一環として、日本のものづくり産業が直面する課題(人口減少、高齢化、国際競争力の強化など)に対応し、新たな価値を創出するための重要な役割を担っています。
産学官連携を強化し、技術の実用化と普及を推進していく方針です。
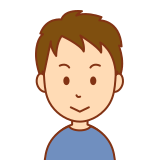
次世代ものづくり実装研究センターは様々な次世代のものづくりシステムを構築することで、生産性向上と高度人材の育成を目指す取り組みです。
データ駆動型加工データ統合・活用とは何か
産総研の次世代ものづくり実装研究センターが掲げる「データ駆動型加工データ統合・活用」とは、製造プロセスで発生する多種多様なデータを単に集めるだけでなく、それらを統合的に管理し、AIやデータ分析技術を駆使して意味のある知見を抽出し、その知見に基づいて加工プロセスを最適化・高度化するアプローチを指します。
「データ駆動型(Data-Driven)」という言葉は、「経験や勘に頼るのではなく、データに基づいて意思決定や行動を行う」という意味合いを持ちます。
製造業の文脈では、これまで熟練工の経験や勘に大きく依存してきた加工技術を、データに基づいて科学的・定量的に制御・改善していくことを目指します。
具体的には、以下の要素が組み合わされます。
- 多様な「加工データ」の統合
- データからの「知見抽出と予測」
- 加工プロセスへの「フィードバックと活用」
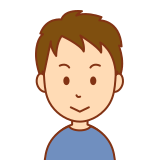
データ駆動型加工データ統合・活用は、熟練工の経験や勘に大きく依存してきた加工技術を、AIやデータ分析技術によって最適化、高度化するアプローチのことです。
多様な「加工データ」の統合とはなにか
「加工データ」には、単に機械の稼働状況だけでなく、以下のような様々な情報が含まれます。
- センサーデータ: 加工中の温度、振動、圧力、電流、音響、画像(加工面、工具の状態)、材料の状態(硬度、組成など)といったリアルタイムデータ。
- 機械稼働データ: 工作機械のスピンドル回転数、送り速度、切削深さ、工具の種類、加工時間、NCプログラムなど、加工条件に関するデータ。
- 品質データ: 加工後の製品の寸法、形状、表面粗さ、検査結果、不良品の発生状況、不良モードなど、品質に関するデータ。
- 材料データ: 加工対象の材料の種類、ロット番号、化学組成、機械的特性(引張強度、降伏点など)、前工程での履歴など。
- 環境データ: 加工時の室温、湿度など。
- 熟練工の知識データ: 前述の「製造技術の知識構造化型データベース」に含まれる、熟練工のノウハウや判断基準(例:「この音が出たら工具が摩耗している兆候」など)も、加工データと紐付けて統合されます。
- シミュレーションデータ: 仮想空間での加工シミュレーション結果(応力分布、熱変形予測など)も、実際の加工データと突き合わせることで、より高精度な予測モデル構築に貢献します。
これらの異種データが、時系列、ロット番号、製品ID、設備IDなどのキー情報で紐付けられ、一元的に管理されることが「統合」のポイントです。
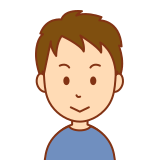
様々な異種データを集め、一元的に管理し、統合することが多様な「加工データ」の統合です。
多様な「加工データ」の統合の実例は
多様な「加工データ」の統合の実例は、スマートファクトリー化を進める多くの製造業で見られます。
1. 自動車部品メーカーにおける品質向上と不良削減
- 状況: 自動車部品の製造では、高い品質とトレーサビリティが求められます。わずかな不良でも、リコールにつながるリスクがあるため、徹底した品質管理が必要です。
- 統合されるデータ:
- 設計データ: 部品のCADデータ、公差、材料特性。
- 生産計画データ: 各部品の生産スケジュール、ロット番号、生産量。
- 機械稼働データ: 各工作機械(切削機、プレス機、溶接機など)の運転速度、圧力、温度、電流、振動、工具摩耗度などのリアルタイムセンサーデータ。
- 品質検査データ: 各工程で実施される自動検査(画像検査、寸法検査、非破壊検査など)の結果、合格/不合格判定、不良箇所と不良モードの詳細。
- 材料データ: 部品に使用される原材料のロット情報、供給元、成分分析結果。
- 環境データ: 工場内の温湿度、粉塵レベルなど。
- 作業者データ: 作業履歴、担当者情報(ただし、個人情報保護に配慮)。
- 統合の方法と活用:
- これらのデータは、部品の個体識別情報(QRコードやRFIDなど)と紐付けられ、データレイクやデータウェアハウスに一元的に蓄積されます。
- AIや機械学習モデルが、各工程の加工条件データと最終的な品質検査データを関連付け、不良が発生しやすい条件や、特定の材料ロットで不良が発生する傾向などを自動で発見します。
- 例えば、「特定の工具の摩耗が一定レベルを超え、かつ特定の材料ロットで加工を行うと、表面粗さに不良が発生しやすい」といった知見が導き出されます。
- この知見は、リアルタイムで生産ラインにフィードバックされ、自動的に加工条件が調整されたり、作業員に工具交換のアラートが送られたりすることで、不良品の発生を未然に防ぎます。
- また、万が一不良品が発生した場合でも、統合されたトレーサビリティデータから、いつ、どの機械で、どのような条件で、どの材料を使って製造されたかを即座に特定し、迅速な原因究明と対策が可能になります。
2. 半導体製造工場における歩留まり改善
- 状況: 半導体製造は非常に微細な加工が連続するプロセスであり、わずかな環境変化や設備異常でも歩留まり(良品率)が大きく変動します。
- 統合されるデータ:
- プロセスデータ: 各製造工程(露光、エッチング、成膜など)におけるガス流量、温度、圧力、電力、プラズマ強度などの詳細なレシピデータとリアルタイムの運転データ。
- 検査データ: 各工程後のウェハー上のパターン欠陥、回路抵抗、電気特性などの詳細な検査データ。
- 設備ログデータ: 製造装置ごとの稼働状況、エラーログ、メンテナンス履歴、部品交換履歴。
- クリーンルーム環境データ: 微粒子、温湿度、気流などの環境センサーデータ。
- ロットデータ: ウェハーのロット番号、サプライヤー、材料特性。
- 統合の方法と活用:
- 数十万点にも及ぶセンサーデータや検査データが、各ウェハー、各プロセスステップと紐付けられ、ビッグデータ基盤に集約されます。
- データ分析ツールやAIが、これらの膨大なデータの中から、歩留まり低下に影響を与える隠れた相関関係や異常パターンを発見します。
- 例えば、「特定の装置での特定プロセスのパラメータが、他の工程の特定の検査項目に影響を与え、最終的な歩留まりを低下させている」といった複雑な因果関係を解明します。
- 分析結果に基づき、プロセスのパラメータを自動調整したり、異常の兆候がある装置に対して予防保全を指示したりすることで、歩留まりの変動を抑え、安定した生産を実現します。
- また、過去の良品データと不良品データをAIに学習させることで、新たな不良パターンを早期に検知し、未然に防ぐことが可能になります。
3. 工作機械メーカーにおける製品の性能改善とサービス化
- 状況: 工作機械メーカーは、自社が販売した機械の稼働状況を把握し、故障予測や性能向上に役立てたいと考えています。
- 統合されるデータ:
- 設計データ: 販売した工作機械のCADデータ、部品構成、設計仕様。
- 製造履歴データ: 組み立て時の品質検査データ、初期設定値。
- 稼働データ: 顧客の工場に設置された機械からリアルタイムで送られる、主軸回転数、送り速度、切削抵抗、工具負荷、温度、振動、電力消費などのセンサーデータ。
- メンテナンス履歴データ: 顧客からの問い合わせ、修理履歴、部品交換履歴、エンジニアの作業記録。
- 加工履歴データ: 顧客が実際にその機械でどのような部品を、どのような条件で加工したかの情報(顧客の同意を得て収集)。
- 統合の方法と活用:
- クラウド上のプラットフォームに、販売した個々の機械ごとに上記のデータが紐付けられ、デジタルツインとして管理されます。
- メーカーは、このデジタルツインを通じて、世界中の自社製機械の稼働状況をリアルタイムで監視します。
- AIが稼働データと過去の故障履歴を分析し、故障の兆候を早期に検知して顧客にアラートを発し、予防保全を提案します(予知保全)。
- また、顧客の加工履歴データと機械の稼働状況を分析することで、「この機械は特定の種類の加工で高い負荷がかかりやすい」といった傾向を把握し、次世代機の設計改善にフィードバックします。
- さらに、顧客に対して「この加工条件に変えることで、工具寿命が20%延びる可能性があります」といった最適化の提案を行うなど、アフターサービスを強化し、新たな収益源(データ駆動型サービス)を生み出しています。
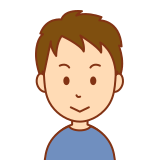
様な加工データを統合し、高度な分析を行うことで、品質改善、生産性向上、コスト削減、そして新たなビジネスモデルの創出に貢献しています。
コメント