この記事で分かること
- インターポーザーとは:複数の半導体チップを接続するための中間基板です。微細な配線でチップ間の高速な信号伝達や電力供給を可能にし、高密度なパッケージングと性能向上を実現します。
- パッケージ基板との違いは:パッケージ基板は半導体チップを外部(マザーボードなど)に接続する「土台」で、保護や放熱も担います。一方、インターポーザーは複数のチップ同士を高密度かつ高速に接続するための「中間基板」で、より微細な配線が特徴です。
TOPPANの次世代半導体用インターポーザーの開発
TOPPANは、次世代半導体用のインターポーザーの開発と準備に積極的に取り組んでいます。
https://chemicaldaily.com/archives/661698
次世代半導体の高機能化に不可欠なインターポーザー技術において、材料開発から生産体制の構築、国際的な連携まで、多角的に準備を進めています。
インターポーザーとは何か
インターポーザー(Interposer)とは、半導体チップや電子部品を接続するための中間基板のことです。「interpose」は「間に挟む」という意味を持つ英語が語源となっています。
半導体技術の進化により、複数の異なる機能を持つチップを一つのパッケージに集積する「ヘテロジニアスインテグレーション(異種チップ集積)」が進んでいます。この際、異なるサイズのチップや、異なる製造プロセスで製造されたチップ同士を直接接続するのは非常に困難です。そこで、インターポーザーが橋渡し役として重要な役割を担います。
インターポーザーの主な役割
- 電気的接続の確立:
- 複数の半導体チップ(ダイ)をインターポーザー上に配置し、その内部に形成された微細な配線層(RDL: Redistribution Layer)や貫通ビア(TSV: Through-Silicon Via)を通じて、チップ間で高速かつ安定した信号伝達を可能にします。
- これにより、チップ間のデータ転送速度を大幅に向上させ、システム全体の性能を最適化できます。
- 高密度実装の実現:
- 複数のチップを近接して配置できるため、回路の高密度実装が可能になります。
- パッケージ内の配線距離を短縮し、信号遅延を最小限に抑えることで、小型化と高性能化を両立させます。
- 熱管理の向上:
- 半導体デバイスの動作中に発生する熱を効果的に分散し、温度管理を助けます。熱伝導性の良い材料を使用することで、デバイスの性能向上と寿命延長に貢献します。
- 電力供給の効率化:
- 電源ラインを最適に配置することで、各チップへの電力供給を安定化し、電力消費を抑えることができます。
インターポーザーの材料
- シリコンインターポーザー: 微細な配線加工が可能で、高性能なデータ転送に適していますが、コストが高い傾向があります。
- 有機インターポーザー(RDLインターポーザー): 樹脂基板を使用し、製造コストを抑えることができます。電気損失が少なく、高周波特性に優れる場合があります。
- ガラスインターポーザー: シリコンに代わる選択肢として注目されており、高い平坦性、熱安定性、優れた電気特性を持つため、次世代半導体向けとして開発が進められています。
インターポーザーは、特にAI処理やデータセンター向けの高性能半導体、スマートフォンなどの小型高性能デバイスにおいて、その重要性が増しています。2.5D実装や3D実装といった、より高度なパッケージング技術において不可欠なコンポーネントとなっています。
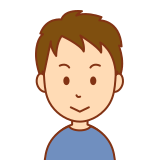
インターポーザーは、複数の半導体チップを接続するための中間基板です。微細な配線でチップ間の高速な信号伝達や電力供給を可能にし、高密度なパッケージングと性能向上を実現します。シリコン、有機、ガラスなどが材料として使われます。
パッケージ基板との違いはなにか
インターポーザーとパッケージ基板は、どちらも半導体チップを搭載し、電気的に接続するための重要な部品ですが、その役割と位置づけ、そして微細加工のレベルに違いがあります。
パッケージ基板
半導体チップ(またはインターポーザー上に搭載されたチップ群)を最終的に外部のプリント基板(マザーボードなど)に接続するための、より大きな「土台」となる基板です。チップの保護、放熱、外部との電気的接続(はんだボールなど)を提供する、文字通りの「パッケージ」の一部です。
インターポーザー
主に複数の半導体チップ(ダイ)同士を、高密度かつ高速に接続するための中間基板です。パッケージ基板とチップの間に挟まれる形で配置され、より微細な配線でチップ間の情報をやり取りする役割を担います。
パッケージ基板(例:FC-BGA基板)
- 主な役割:
- 半導体チップを物理的に保護する。
- チップから発生する熱を外部に放熱する。
- チップの微細な端子ピッチを、より広いピッチの外部接続端子(はんだボールなど)に変換し、プリント基板に実装しやすくする。
- チップに電源を供給し、信号を入出力するための電気的経路を提供する。
- チップが直接マザーボードに接続できない場合に、その間の「橋渡し」をする。
- 特徴:
- 一般的にインターポーザーよりも大きく、頑丈な構造をしている。
- 配線密度はインターポーザーほど高くないが、チップの入出力端子数が増えるにつれて、パッケージ基板自体の配線も高密度化している。
- 有機材料(樹脂)が主流だが、セラミックなども使われる。
- 従来の半導体パッケージの主流であったFC-BGA(Flip Chip-Ball Grid Array)では、各々の半導体チップが各々のパッケージ基板上に搭載され、チップ間の情報伝達はマザーボード経由で行われる。
インターポーザー
- 主な役割:
- 複数の異なる半導体チップ(ダイ)を極めて近接して配置し、チップ同士を高密度かつ高速に電気的に接続する。
- 特に「2.5Dパッケージング」と呼ばれる技術で用いられ、ロジックチップとメモリチップなどを横に並べて接続する際に活用される。
- チップ間で大量のデータを高速にやり取りするための微細な配線を提供する。
- 必要に応じて貫通電極(TSV: Through-Silicon Via)などを持ち、垂直方向の接続も可能にする。
- 特徴:
- パッケージ基板よりも**はるかに微細な配線(1μm以下)**が可能。これは、半導体の前工程(チップ製造)の技術を応用して作られるシリコンインターポーザーに顕著。
- シリコン、有機材料(RDLインターポーザー)、ガラスなど様々な材料がある。
- チップ間(ダイ間)の距離を短縮し、信号遅延や電力損失を最小限に抑えることに特化している。
- 高性能コンピューティング(HPC)やAIプロセッサなど、複数の高性能チップを統合する際に不可欠な存在。
関係性
現代の先進的な半導体パッケージでは、インターポーザーとパッケージ基板は密接に連携して機能します。
例えば、高性能なAIプロセッサでは、以下のような構造が一般的です。
- 複数の半導体チップ(CPU、GPU、HBMメモリなど)がインターポーザー上に高密度に実装される。
- このインターポーザーは、さらにその下のパッケージ基板に接続される。
- パッケージ基板は、最終的にPCのマザーボードなどのプリント基板に実装される。
このように、インターポーザーはチップ間の「内部的な接続」に特化し、パッケージ基板はチップ群(またはインターポーザー上のチップ群)を「外部と接続する」役割を担う、という棲み分けがされています。インターポーザーの登場により、従来のパッケージ基板だけでは難しかった、複数の高性能チップを効率的に統合する「2.5D実装」が実現可能になりました。
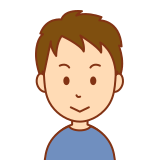
パッケージ基板は半導体チップを外部(マザーボードなど)に接続する「土台」で、保護や放熱も担います。一方、インターポーザーは複数のチップ同士を高密度かつ高速に接続するための「中間基板」で、より微細な配線が特徴です。
インターポーザーの課題は何か
インターポーザーは高性能半導体パッケージに不可欠な技術ですが、その導入と普及にはいくつかの課題があります。主な課題は以下の通りです。
高コスト
- シリコンインターポーザー: 最も微細な配線が可能で高性能ですが、半導体前工程の設備やプロセスを使用するため、製造コストが非常に高いです。特に大面積化すると、そのコストはさらに跳ね上がります。
- 全体コスト: インターポーザーそのもののコストに加えて、インターポーザーを介してチップを接続する2.5D/3Dパッケージング全体が、従来のパッケージングよりも複雑な工程を伴うため、全体の製造コストが上昇します。
熱管理の課題
- インターポーザー上に複数の高性能チップが高密度に集積されるため、発熱量が非常に大きくなります。
- 熱がこもりやすく、効率的な放熱が求められます。適切な熱管理ができないと、チップの性能低下や寿命の短縮につながる可能性があります。高熱伝導材料や冷却技術のさらなる進化が必要です。
製造技術の複雑化と歩留まり
- 微細配線と高精度接続: インターポーザーの配線は非常に微細であり、チップとの接続も高い精度が求められます。製造プロセスが複雑になり、わずかな欠陥でも不良につながりやすいため、歩留まりの確保が課題です。
- 材料の信頼性と耐久性: 特に有機インターポーザーやガラスインターポーザーでは、柔軟性や熱膨張率の差による応力、耐久性、信頼性の確保が課題となることがあります。
- 貫通ビア(TSV)の形成: シリコンインターポーザーで用いられるTSVの形成は高度な技術を要し、製造コストと歩留まりに影響を与えます。
材料選定と特性のバランス
- インターポーザーの材料(シリコン、有機、ガラスなど)にはそれぞれ一長一短があります。
- シリコン: 微細加工性、熱伝導性に優れるが、高コスト、高周波特性に課題がある場合があります。
- 有機: 低コスト、高周波特性に優れるが、微細加工が難しく、剛性が低い場合がある(TOPPANがこの課題解決に取り組んでいます)。
- ガラス: 平坦性、熱安定性、電気特性に優れるが、製造プロセスの確立やコストが課題となる場合があります。
- 用途に応じて最適な材料と構造を選択し、性能、コスト、信頼性のバランスを取ることが重要です。
設計の複雑さ
- 複数の異なるチップをインターポーザー上で統合するため、全体の設計が非常に複雑になります。
- チップ間の信号整合性、電力供給、熱分布などを考慮した高度な設計技術が求められます。
これらの課題に対し、各メーカーや研究機関は、低コスト化のための新素材(有機、ガラス)や新プロセスの開発、熱管理技術の向上、製造歩留まりの改善、設計ツールの進化など、多岐にわたる研究開発を進めています。
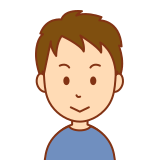
インターポーザーの課題は、製造コストの高さ、複雑な熱管理、製造歩留まりの低さ、そして微細加工技術の高度化に伴う複雑な設計が挙げられます。これらを解決する新素材やプロセスの開発が求められています。
コメント