この記事で分かること
- ウェットストリップとは:導体製造で不要なレジストを化学溶液(薬液)に浸漬して除去する方法です。プラズマダメージがない利点がある一方、廃液処理や下地への影響が課題となることがあります。
- 使用される薬液:濃硫酸と過酸化水素水の混合液であるSPM、アミン系やジメチルスルホキシドのような有機系剝離液、水酸化テトラメチルアンモニウムのようなアルカリ系剝離液などが使用されます。
- レジストが膨張する理由:レジストの分子構造の隙間に溶剤分子が入り込み、レジストの高分子鎖を広げることで、物理的に膨張させています。
ウェットストリップ
半導体の重要性が増す中で、前工程装置は世界的に成長が続いています。
https://optronics-media.com/news/20250414/99245/
特に中国は米中対立もあり、大幅な投資増加が続いています。今後も先端技術を駆使した半導体の需要増加と従来技術による成熟プロセスともにその重要性は増加するとみられています。
今回はレジスト除去工程の一種であるウエットストリップに関する解説となります。
半導体の前工程とは
半導体の前工程とは、シリコンウェハ上にトランジスタや配線などの微細な回路を形成する一連のプロセスのことです。ウェハを素材として、集積回路を作り込んでいく、半導体製造の最も重要な部分と言えます。非常に多くの精密な工程を経て、最終的な半導体チップの機能が決まります。
主な前工程は以下の通りです。
ウェハ準備
シリコンインゴットの製造: 高純度のシリコンを溶解し、種結晶を用いて単結晶のシリコンインゴットを育成します。
- スライス: インゴットを薄い円盤状(ウェハ)にスライスします。
- 研磨: ウェハ表面を平坦かつ滑らかに研磨します。
- 洗浄: ウェハ表面の微細な異物や汚れを徹底的に除去します。
成膜
ウェハ表面に、酸化膜、窒化膜、金属膜など、様々な薄膜を形成します。
- 成膜方法には、CVD(化学気相成長法)、スパッタリング(物理気相成長法)、ALD(原子層堆積法)などがあります。
フォトリソグラフィ
ウェハ表面に感光材(フォトレジスト)を塗布します。
- 回路パターンが描かれたマスク(フォトマスク)を通して紫外線を照射し、レジストにパターンを焼き付けます。
- 現像液で不要なレジストを除去し、ウェハ上に回路パターンを形成します。
エッチング
フォトリソグラフィでパターン形成されたレジストをマスクとして、露出した成膜を除去し、ウェハに回路パターンを転写します。
- エッチングには、液体を用いるウェットエッチングと、プラズマを用いるドライエッチングがあります。
不純物導入(ドーピング)
半導体特性を持たせるために、リンやボロンなどの不純物をウェハ中に注入します。
- イオン注入法などが用いられます。
平坦化(CMP: Chemical Mechanical Polishing)
表面の凹凸をなくし、平坦にするための処理です。
- 化学的な腐食と 研磨を同時に行います。
配線形成(メタライゼーション)
形成されたトランジスタなどの素子間を金属配線で接続します。
- スパッタリングなどで金属膜を形成し、フォトリソグラフィとエッチングで配線パターンを作ります。
これらの工程を何度も繰り返し行うことで、複雑な集積回路がウェハ上に形成されます。前工程は、半導体の性能や品質を大きく左右する、非常に重要なプロセスです。
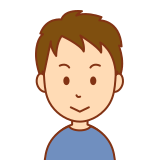
前工程は、細な回路を形成する一連のプロセスのことで、半導体の性能や品質を大きく左右する、非常に重要なプロセスです。
ウエットストリップとは何か
ウェットストリップ(Wet Strip)は、半導体製造工程において、役割を終えたフォトレジストや特定の汚染物質を、化学溶液(薬液)にウェーハを浸漬させることで溶解・剥離・除去する方法です。
「ウェット(湿式)」という名の通り、液体を使用するのが特徴で、ドライアッシングとは対照的なアプローチを取ります。
原理
ウェットストリップの基本的な原理は、使用する薬液とレジスト(または除去対象物)との間の化学反応または溶解です。
- 酸化分解: レジストのような有機物を強力な酸化剤で分解し、水溶性の低い分子やガスとして除去します。
- 溶解・膨潤: レジストを構成するポリマーを溶解させる溶剤や、ポリマーを膨潤させて剥がれやすくする溶剤を使用します。
- 加水分解: アルカリ性の薬液などがレジスト中のエステル結合などを加水分解し、水溶性の低分子化合物に変えることで除去します。
主な薬液の種類と特徴
- SPM (Sulfuric Acid Hydrogen Peroxide Mixture):
- 主成分: 濃硫酸と過酸化水素水の混合液。
- 原理: 過酸化水素が分解して生成される活性酸素種(例:ヒドロキシラジカル OH⋅)が、レジスト(有機物)を強力に酸化分解します。
- 特徴: 非常に強力な酸化力を持つため、レジストだけでなく、有機系の残渣、金属汚染なども同時に除去できます。一般的に高温(80℃~150℃程度)で使用されます。
- メリット: 強力な除去力、幅広い種類の有機物に対応。
- デメリット: 下地膜へのエッチング(特に酸化膜)やダメージのリスク、高価な薬品、廃液処理の課題、安全性への配慮が必要。
- 有機系剥離液:
- 主成分: アミン系(例:MEA: モノエタノールアミン)、DMSO(ジメチルスルホキシド)、NMP(N-メチル-2-ピロリドン)などの有機溶剤をベースとした混合液。しばしば界面活性剤や腐食抑制剤が添加されます。
- 原理: レジストポリマーを直接溶解させるか、膨潤させて基板から剥離させます。アルカリ性の有機アミンがレジストの加水分解を促進する場合もあります。
- 特徴: SPMに比べて下地膜へのダメージが少ない傾向があります。特定のレジストやプロセス条件に合わせて様々な組成のものが開発されています。
- メリット: 下地への選択性が高い、プラズマダメージがない。
- デメリット: 除去能力がSPMより劣る場合がある、イオン注入などで硬化したレジストには効果が低い、残渣が残りやすい場合がある、薬液のコスト。
- アルカリ系剥離液
- 主成分: 水酸化テトラメチルアンモニウム(TMAH)など。
- 原理: レジストを水溶性にする加水分解反応などを利用します。
- 特徴: 特定のレジストや、酸性薬液が使えない場合に利用されます。
ウェットストリップの装置
- バッチ式ウェットベンチ/スピンプロセッサー: 複数のウェーハを一度に処理する槽型装置や、1枚ずつウェーハを回転させながら薬液を供給するスピンプロセッサーがあります。
- 枚葉式ウェット処理装置: ウェーハ1枚ずつ処理槽に入れるタイプや、スプレー式で薬液を噴霧するタイプなどがあります。特に最近は、環境負荷低減や高均一性を目指して枚葉式が増えています。
メリットとデメリット
メリット:
- プラズマダメージがない: 荷電粒子によるチャージアップや物理的スパッタリングが発生しないため、ダメージに敏感なデバイスや材料(特に低k膜や薄いゲート酸化膜)に適しています。
- 装置コストが比較的低い: ドライアッシャーに比べて初期導入コストが低い傾向があります。
- 高スループット(バッチ式の場合): 一度に多数のウェーハを処理できるため、大量生産に適しています。
- 付着物の同時除去: レジストだけでなく、微粒子や金属汚染などを同時に除去できる場合が多いです(特にSPM)。
デメリット:
- 薬液消費と廃液処理: 大量の薬液を使用し、使用済み薬液の処理が必要になるため、環境負荷やコストが高くなる可能性があります。
- 下地への影響: 薬液の種類によっては、目的のレジストだけでなく、下地膜やデバイス構造をエッチング・腐食させてしまうリスクがあります。特に異方性エッチングが困難なため、微細なパターン側面への影響も考慮が必要です。
- 安全性: 強酸や強アルカリを使用する場合、作業者の安全管理が非常に重要です。
- イオン注入硬化レジストへの対応: 高ドーズのイオン注入などで硬化したレジストは、ウェットストリップでは除去が困難な場合があります。この場合、ドライアッシングで表面の硬化層を除去した後にウェットストリップを併用するなどのハイブリッドプロセスが用いられることもあります。
- ぬれ性の問題: 超微細パターン内部への薬液の浸透性や、乾燥時のウォーターマーク(シミ)が課題となることがあります。
近年は、環境規制の強化や微細化による下地ダメージへの懸念から、ダメージの少ないドライアッシングが主流になりつつありますが、特定のプロセスやコスト効率の観点から、ウェットストリップも依然として重要なレジスト除去手段として利用されています。また、環境負荷低減のための薬液リサイクル技術や、低ダメージ・高効率な新しい薬液の開発も進められています。
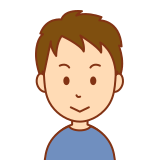
ウェットストリップは、半導体製造で不要なレジストを化学溶液(薬液)に浸漬して除去する方法です。プラズマダメージがない利点がある一方、廃液処理や下地への影響が課題となることがあります。
なぜ、有機系剝離液はレジストを膨張させることができるのか
有機系剥離液がレジストを膨潤させるメカニズムは、主にレジストのポリマー(高分子)と剥離液の溶剤分子との間の相互作用によります。簡単に言うと、剥離液がレジストの分子構造の隙間に入り込み、レジスト自体を「溶かし始める」ことで膨らませるのです。
レジスト膨潤のメカニズム
- 溶剤の浸透と高分子鎖の拡散:レジストは高分子(ポリマー)が網目状に絡み合ってできています。有機系剥離液に含まれる溶剤分子が、レジスト表面から内部へと浸透し始めます。溶剤分子がレジストの高分子鎖の間に入り込むことで、高分子鎖が互いに引き離され、動きやすくなります。
- 高分子鎖の解離と引き伸ばし:溶剤分子がさらに多く浸透すると、レジストの高分子鎖同士の弱い結合(分子間力など)が弱まり、高分子鎖がより自由に動き回れるようになります。これにより、絡み合っていた高分子鎖が広がり、レジスト全体が体積を増し、膨潤という現象が起こります。
- 溶解への移行:膨潤が進むと、最終的にはレジストの高分子鎖が剥離液中に完全に分散し、レジストが溶解して基板から剥がれ落ちます。膨潤は溶解の前段階とも言えます。
影響する要因
- レジストの化学構造: レジストのポリマーの種類や架橋(分子間の結合)の度合いによって、剥離液への浸透性や溶解性が異なります。架橋が強いレジスト(特にイオン注入で硬化したレジストなど)は、膨潤しにくく、溶解も困難になります。
- 剥離液の溶剤特性:
- 溶解度パラメーターの類似性: 剥離液の溶剤とレジストのポリマーの溶解度パラメーター(分子間相互作用の尺度)が近いほど、お互いが混ざりやすく、浸透・膨潤・溶解が進みやすくなります。
- 分子サイズ: 小さな分子の溶剤はレジスト内部に浸透しやすいため、膨潤が起こりやすいです。
- 温度: 通常、温度が高いほど分子運動が活発になり、溶剤の浸透や高分子鎖の動きが促進されるため、膨潤や溶解が早まります。
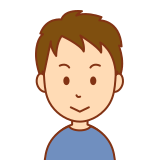
有機系剥離液はレジストの分子構造の隙間に溶剤分子が入り込み、レジストの高分子鎖を広げることで、物理的に膨張させ、最終的には溶解・剥離を行っています。
酸性薬液が使えない場合とはどんな場合か
半導体製造プロセスにおいて、酸性薬液が使えない、または使用が推奨されないケースはいくつかあります。これは主に、ウェーハ上のデリケートな材料や構造へのダメージ、プロセスへの悪影響、安全性といった観点から判断されます。
酸性薬液が使えない主なケース
- 酸に弱い下地膜やデバイス構造が存在する場合最も一般的なケースです。ウェーハ上には様々な薄膜や微細な構造が形成されており、それらの中には酸によってエッチングされたり、腐食されたりする可能性がある材料があります。
- 低k膜(Low-k膜): 最近の半導体では、配線間の絶縁膜として誘電率の低い「低k膜」が使われます。多くの場合、これらの膜は多孔質であったり、有機成分を含んでいたりするため、酸性薬液、特に強酸(SPMなど)によって膜構造が変化したり、誘電率が上昇(k値が悪化)するダメージを受けやすいです。水分の吸着も誘電率上昇につながるため、酸性薬液後の水洗・乾燥プロセスも注意が必要です。
- 特定の金属配線: 例えば、アルミニウム(Al)配線などは酸によって腐食する可能性があります。銅(Cu)配線も、CMP(化学機械研磨)後の洗浄などで、酸性環境下でのガルバニック腐食(異種金属間の電位差による腐食)を防ぐために、特定の薬液選定やプロセス条件が重要になります。
- ゲート酸化膜などの極薄絶縁膜: 酸性薬液によるごくわずかなエッチングやダメージでも、デバイスの電気特性に致命的な影響を与える可能性があります。
- 選択性が必要な場合レジストだけを除去し、下地膜には全く影響を与えたくない場合、強力な酸性薬液では下地膜もエッチングしてしまう可能性があります。このような場合は、レジストに対して高い選択性を持つ有機系剥離液や、ダメージの少ないドライアッシングが選ばれます。
- 安全性と環境負荷への懸念強酸性の薬液は、作業者の安全管理が厳しく求められ、廃液処理にもコストと手間がかかります。環境負荷低減の観点から、できるだけ使用を避けたいという企業の意向もあります。
- レジストの特性による場合特定のレジストの種類によっては、酸性薬液よりもアルカリ性薬液や有機系剥離液の方が効率的に除去できる場合があります。また、イオン注入などでレジストが硬化してしまった場合、SPMのような強酸でも完全に除去することが困難な場合があります。
これらの理由から、半導体製造プロセスでは、単一のレジスト除去方法に依存するのではなく、ウェーハ上の材料、デバイス構造、要求される品質、コスト、スループットなどを総合的に考慮し、ドライアッシング、ウェットストリップ(有機系、アルカリ系含む)、あるいはそれらの組み合わせ(ハイブリッドプロセス)の中から最適な方法が選択されます。
特にダメージに敏感な先進ノードのプロセスでは、酸性薬液の使用が避けられ、ドライアッシングや低ダメージな有機系剥離液が主流となる傾向があります。
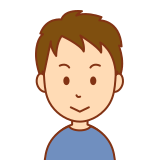
酸性薬液が使えないのは、低k膜のように酸に弱い下地膜や、特定の金属配線が腐食するリスクがある場合です。また、安全性や廃液処理の観点からも使用を避けることがあります。
コメント