この記事で分かること
- 車向けの接着剤とは:軽量化、安全性向上、生産性向上に不可欠な素材です。異種材料接合を可能にし、車体剛性向上やNVH対策にも貢献します。
- ウェルドボンドとは:接着剤とスポット溶接を併用する接合技術です。高強度・高剛性を実現し、車体の軽量化、安全性、防錆性、静粛性向上に貢献します。
- 使用される物質:主に一液加熱硬化型エポキシ樹脂系接着剤と、鋼板やアルミニウム合金などの金属材料が使用されます。接着剤はスポット溶接の熱で硬化し、高い強度と耐久性を実現します。
サンスター、インドでの車向け接着剤の輸出拡大
サンスターがインドでの車向け接着剤の輸出を3倍に拡大する計画であることが報じられています。
https://chemicaldaily.com/archives/665084
これは主に、自動車市場の成長が見込まれるインドにおいて、同社の接着剤の需要が高まっているためと考えられます。サンスターは、自動車の軽量化や耐久性向上に貢献する高性能な接着剤を提供しており、これらの製品がインド市場で評価されていると推測されます。
車向けの接着剤とは
車向けの接着剤は、自動車の製造工程において非常に重要な役割を果たす特殊な接着剤です。従来の溶接、リベット、ボルト締結といった機械的な接合方法に代わり、またはそれらを補完する形で幅広く使用されています。
車向けの接着剤が重要視される背景
- 軽量化: 燃費向上やCO2排出量削減のため、自動車の軽量化は喫緊の課題です。接着剤は、異種材料(スチール、アルミニウム、CFRPなどの複合材、樹脂など)を接合するのに適しており、これにより部品点数の削減や材料自体の軽量化が可能になります。溶接では困難な異種材料の接合を可能にするため、接着剤は「マルチマテリアル化」に不可欠な技術です。
- 安全性・耐久性の向上: 接着剤は面で接合するため、応力集中を緩和し、車体の剛性を高め、衝撃吸収性を向上させます。また、振動を受けやすい箇所や冷熱が繰り返される箇所でも高い耐久性を発揮し、腐食防止や水密性・気密性の確保にも貢献します。
- 生産性の向上: 接着剤の中には、速硬化性や低温硬化性を持ち、製造工程の短縮や自動化に貢献するものもあります。溶接のように火花が発生せず、パネルの歪みも少ないため、後処理が容易になるなどのメリットもあります。
- 意匠性の向上: 溶接痕などが出ないため、外観品質の向上にも寄与します。
- NVH(騒音・振動・ハーシュネス)対策: 制振材や防音材として、塗布型の接着剤が車体フロアなどに用いられ、車室の静粛性向上に貢献します。
車向けの接着剤の種類と用途例
自動車に使われる接着剤は、その目的や使用部位に応じて様々な種類があります。
- 構造用接着剤(ウェルドボンドなど):
- 特徴: 機械強度が高く、耐熱性、耐久性に優れています。
- 用途: 車体構造の主要部分の接合、剛性向上、衝突安全性の確保。溶接と併用されることも多く、溶接箇所の強度を補完したり、溶接箇所を減らすことで軽量化に寄与します。
- ヘミング用接着剤:
- 特徴: 加熱硬化型のエポキシ樹脂系が多く、仮止め効果も持ちます。
- 用途: ドアやボンネットなどの外板と内板を折り返す「ヘミング部」の接着。外板の強度アップや振動による騒音防止、シーリング(防水)の役割も果たします。
- マスチック接着剤:
- 特徴: ゴム系の弾性接着剤で、充填接着に適しています。耐久性が高く、油面鋼板にも優れた接着性を示します。
- 用途: ボンネットやドアの外板と内板の接着、スポット溶接部の防水・防錆。
- DG用接着剤(ダイレクトグレージング):
- 特徴: 柔軟性と耐衝撃性に優れるウレタン系接着剤が主流です。
- 用途: 窓ガラスの車体への直接接着(はめ込み)。安全性の確保と車体剛性の向上に貢献します。
- 内装用接着剤:
- 特徴: 熱硬化弾性接着剤やホットメルト接着剤など、速硬化性や低VOC(揮発性有機化合物)が求められます。
- 用途: シートカバー、ルーフライナー、断熱マット、ドア表皮材などの内装部品の取り付け。
- スポットシーラー:
- 特徴: ゴム系の弾性接着剤。
- 用途: スポット溶接部に塗布し、耐水性を高め、溶接部の腐食を防ぎます。
- 電装部品用接着剤:
- 特徴: 耐熱・耐水性が高く、電気絶縁性に優れるシリコーン系などが使われます。
- 用途: バッテリーパックの組み立て、電子部品の固定、防水・絶縁。EV化の進展に伴い、需要が増加しています。
その他にも、アンダーボディーコート、発泡充填材(防音・剛性付与)、不定形ガスケット(FIPG)など、多種多様な接着剤が自動車の各所に利用されています。
主な自動車用接着剤メーカー
サンスターのほかにも、自動車用接着剤を製造・供給している主要なメーカーは多数あります。
- 3M(スリーエム)
- ヘンケル(LOCTITE®、TEROSON®など)
- セメダイン
- レゾナック(旧昭和電工)
- デクセリアルズ
- スリーボンド
- 東亞合成(アロンアルフアなど)
- ナガセケムテックス
これらの企業は、自動車の進化に合わせて、より高性能で環境に配慮した接着剤の開発を進めています。
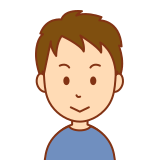
車向けの接着剤は、軽量化、安全性向上、生産性向上に不可欠な素材です。異種材料接合を可能にし、車体剛性向上やNVH対策にも貢献します。構造用、ヘミング用、窓ガラス用など多岐にわたり、自動車の進化に欠かせない重要な役割を担っています。
ウェルドボンドとは何か
ウェルドボンド(Weldbonding)とは、接着接合とスポット溶接(またはプロジェクション溶接などの抵抗溶接)を併用した金属板の接合方法のことです。
簡単に言うと、接着剤を塗布した部品同士を、その接着剤を挟んだ状態でスポット溶接するという技術です。スポット溶接の際に発生する熱を利用して接着剤を硬化させることで、接着と溶接のそれぞれの長所を組み合わせた、より強固で高性能な接合を実現します。
ウェルドボンドの特徴とメリット
ウェルドボンドは、主に自動車の車体製造において広く採用されており、以下のようなメリットがあります。
- 高強度・高剛性:
- スポット溶接は点で接合するのに対し、接着は面で接合します。ウェルドボンドは、この両方の利点を組み合わせることで、従来のスポット溶接のみよりもはるかに高い接合強度と剛性を実現します。
- 応力集中を緩和し、疲労特性が向上するため、耐久性の高い車体を作ることができます。
- 軽量化:
- 高い強度が得られるため、より薄い材料や異なる材料(例:スチールとアルミ)を組み合わせることが可能になり、車体の軽量化に貢献します。
- 溶接箇所の数を減らすこともでき、その分軽量化につながります。
- 安全性向上:
- 車体剛性が高まることで、衝突時の衝撃吸収性が向上し、乗員の安全性を高めます。
- 防錆・防水性の向上:
- 接着剤が接合部を密閉するため、溶接部に発生しやすい腐食を防ぎ、水密性・気密性も向上させます。
- NVH(騒音・振動・ハーシュネス)対策:
- 接着剤が振動を吸収する役割も果たすため、車室内の静粛性向上にも寄与します。
- 生産性向上:
- 接着剤には仮固定効果があるため、部品の組み付けが容易になり、生産効率の向上が期待できます。
- 一部のウェルドボンド接着剤は、塗装工程の熱で硬化するように設計されており、別途硬化のための工程が不要になります。
ウェルドボンドの課題・デメリット
- 接着剤による電極の汚染: スポット溶接時に接着剤が電極に付着し、溶接品質に影響を与える可能性があります。
- ガスの発生: スポット溶接の熱で接着剤が分解し、有毒ガスや腐食性ガスが発生しないような接着剤の選定が重要です。
- 表面処理: 接着剤の性能を最大限に引き出すためには、被着材(接合する材料)の表面処理が重要になる場合があります。
- コスト: 接着剤と溶接の両方の設備や材料が必要になるため、初期投資やランニングコストが上がる可能性があります。
これらの課題に対しては、接着剤メーカーや自動車メーカーが協力し、改良された接着剤や溶接技術の開発が進められています。
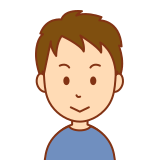
ウェルドボンドは、接着剤とスポット溶接を併用する接合技術です。高強度・高剛性を実現し、車体の軽量化、安全性、防錆性、静粛性向上に貢献します。接着剤の利点と溶接の確実性を組み合わせ、自動車製造で広く活用されています。
ウェルドボンドにはどのような物質が使用されるのか
ウェルドボンドで使用される主要な物質は、接着剤と金属材料です。
1. 接着剤
ウェルドボンドに用いられる接着剤は、スポット溶接の熱に耐え、かつ高い接着強度と耐久性を発揮する特殊なものが選ばれます。主な種類は以下の通りです。
- エポキシ樹脂系接着剤:
- 最も一般的に使用されます。
- 特徴: 強力な接着力、優れた耐熱性、耐薬品性、耐水性、そして高い剛性を持ちます。スポット溶接の熱で硬化を促進させるタイプのものが主流です。
- 種類: 主に一液加熱硬化型エポキシ接着剤が使われます。これは、自動車の塗装ラインの熱(焼き付け温度)を利用して硬化するため、別途硬化工程が不要になり、生産効率が良いからです。一部、二液混合型のエポキシ接着剤も使用されることがあります。
- その他: アルミニウム合金のウェルドボンドでは、導電性材料(例:リン酸塩や亜鉛化合物)を添加して、スポット溶接の連続打点数を高めるように工夫されたエポキシ接着剤も開発されています。
- ポリサルファイドエポキシ、ポリアミドエポキシ、ビニルプラスチゾル系接着剤:
- 一部の事例で、これらの接着剤もウェルドボンドの強度向上に寄与することが報告されています。ただし、エポキシ樹脂系が主流です。
ウェルドボンド用の接着剤には、以下のような特性が求められます。
- 熱硬化性: スポット溶接の熱や、その後の塗装工程の熱で適切に硬化すること。
- 高強度: 金属材料と同等かそれ以上のせん断強度、はく離強度を持つこと。
- 耐衝撃性: 自動車の衝突時などの衝撃に耐えられること。
- 耐久性: 長期間にわたって温度変化、湿度、振動などに耐え、性能を維持できること。
- 良好な油面接着性: プレス油などが残っている鋼板にも直接接着できること(前処理の手間を省くため)。
- 電気絶縁性: 溶接電流が適切に流れるように、溶接に影響を与えない程度の電気絶縁性または導電性が調整されていること。
- ガス発生の抑制: スポット溶接時に有害なガスや電極を汚染するガスが発生しにくいこと。
2. 金属材料
ウェルドボンドで接合される金属材料は、主に自動車の車体に使用される鋼板やアルミニウム合金です。
- 鋼板: 軟鋼板、高張力鋼板(ハイテン材)など、自動車の主要な構造材として使用されます。
- アルミニウム合金: 軽量化のために使用が増えている材料で、A6061-T6などの合金が挙げられます。アルミニウムはスポット溶接単体では強度が低くなりがちですが、ウェルドボンドによってその弱点が補強されます。
- 異種材料の組み合わせ: スチールとアルミニウムのように、異なる種類の金属を接合する際にもウェルドボンドは有効な手段となります。
これらの材料と接着剤が組み合わされることで、自動車の高性能化、軽量化、安全性の向上に貢献しています。
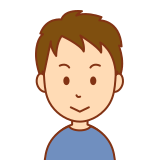
ウェルドボンドには、主に一液加熱硬化型エポキシ樹脂系接着剤と、鋼板やアルミニウム合金などの金属材料が使用されます。接着剤はスポット溶接の熱で硬化し、高い強度と耐久性を実現します。
エポキシ樹脂系接着剤の仕組みは
エポキシ樹脂系接着剤の仕組みは、エポキシ樹脂と硬化剤の化学反応に基づいて「硬化」することで接着力を発揮します。
具体的には、エポキシ樹脂が持つ「エポキシ環(エポキシ基、オキシラン環とも呼ばれる三員環構造)」と、硬化剤が持つ「活性水素(アミン、酸無水物、フェノールなどの官能基に結合した水素原子)」が反応し、開環重合と呼ばれるプロセスを経て、三次元の網目状の強固な分子構造を形成します。
この化学反応によって、液体状だった接着剤が固体の樹脂になり、被着体(接着される材料)同士を強固に接着します。
主なポイント
- 熱硬化性樹脂: エポキシ樹脂は熱硬化性樹脂に分類されます。これは、一度硬化すると熱を加えても軟化せず、元の形状に戻らない性質を持つことを意味します。
- 主剤と硬化剤: 基本的に、エポキシ樹脂(主剤)だけでは硬化せず、硬化剤と混合することで反応が始まります。
- 二液型: 主剤と硬化剤を混ぜ合わせることで常温または加熱により硬化が進行します。
- 一液型: 主剤と硬化剤があらかじめ混合されており、通常は加熱することで硬化反応が開始されます。自動車のウェルドボンドで使われるのはこのタイプが多いです。
- 副生成物が出ない: エポキシ環の開環重合という反応は、水を始めとする副生成物を発生させないのが特徴です。このため、硬化時の体積収縮が少なく、高い寸法安定性が得られます。
- 強固な三次元ネットワーク構造: 硬化によって形成される三次元の網目状構造は、高い機械的強度、耐熱性、耐薬品性、耐水性、電気絶縁性など、優れた特性をもたらします。
このように、エポキシ樹脂系接着剤は、単なる物理的な付着だけでなく、分子レベルでの強固な結合を形成することで、非常に高い接着性能を発揮するのです。
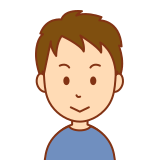
エポキシ樹脂と硬化剤が化学反応し、エポキシ環が開環重合することで、三次元の強固な網目構造を形成します。この反応により液体から固体へ硬化し、優れた接着強度や耐熱性、耐水性を発揮します。副生成物が出ず、高い寸法安定性も特徴です。
コメント