この記事で分かること
- PEEK樹脂とは:ポリエーテルエーテルケトンの略で、耐熱性、機械的強度、耐薬品性、軽量性に優れたスーパーエンジニアリングプラスチックです。250℃以上の連続使用が可能で、医療、航空宇宙、自動車、半導体など、過酷な環境で使われる部品に活用されます。
- 3Dプリンターでの応用例:医療分野(患者に合わせたインプラントや手術ガイド)、航空宇宙・自動車分野(軽量・高強度部品)、半導体製造装置(耐熱・耐薬品性部品)など、高性能が求められる多様な産業で複雑なカスタム部品製作に活用されています。
グーテンベルクのPEEK樹脂対応3Dプリンター
株式会社グーテンベルクは、PEEK樹脂に対応した国産超高速産業用3Dプリンターを開発しています。
https://gutenberg.co.jp/products/g-zero-MP1
これらの技術により、PEEKのような高機能材料の3Dプリンティングにおける課題であった、積層間結合の弱さを克服し、高い強度、耐熱性、耐薬品性を持つ実用的なPEEK部品の製造を目指しています。
PEEK樹脂とは何か
PEEK樹脂とは、「Poly Ether Ether Ketone(ポリエーテルエーテルケトン)」の略称で、スーパーエンジニアリングプラスチックに分類される高性能な熱可塑性樹脂です。数あるプラスチック素材の中でも特に優れた特性を持つことから、「夢のプラスチック」とも呼ばれることがあります。
PEEK樹脂の主な特徴
- 卓越した耐熱性:
- 連続使用温度が250℃~260℃と非常に高く、熱可塑性樹脂の中で最高クラスの耐熱性を示します。
- 融点は約343℃と高く、短時間であれば300℃までの高温にも耐えられます。
- 耐熱水性、耐スチーム性にも優れ、200℃~260℃のスチーム中でも連続使用が可能で、オートクレーブによる高圧蒸気滅菌にも対応できます。
- 高い機械的強度:
- 引張強度や耐衝撃性に優れ、広い温度範囲でその強度を維持します。
- クリープ特性(長時間荷重をかけた際の変形しにくさ)や耐疲労性、耐摩耗性も非常に優れています。
- ガラス繊維や炭素繊維を配合したグレード(強化グレード)では、さらに強度や剛性を向上させることができます。
- 優れた耐薬品性:
- 多くの酸、アルカリ、有機溶媒に対して高い耐性を示し、高温下でも化学的に安定しています。ただし、濃硫酸などの強酸には溶解する場合があります。
- 難燃性:
- UL94 V-0という高い難燃性を持つ素材であり、燃えにくく、燃焼時の発煙や有毒ガスの発生が極めて少ないという特徴があります。
- 良好な電気的特性:
- 高温、高圧、高湿度の過酷な環境下でも優れた電気絶縁性を維持します。高周波特性にも優れています。
- 耐放射線性:
- ガンマ線やX線などの放射線による劣化が起こりにくく、放射線環境下での使用に適しています。
- 軽量性:
- 金属と比較して非常に軽量であり(鉄の約1/6、アルミニウムの約1/2)、部品の軽量化に貢献します。
- 生体適合性(一部グレード):
- 体内で無毒かつ不活性であり、生体適合性に優れるインプラントグレードのPEEK樹脂も存在します。
PEEK樹脂の主な用途
これらの優れた特性から、PEEK樹脂は以下のような高い信頼性や過酷な環境下での使用が求められる分野で広く活用されています。
- 自動車産業: エンジン周辺部品、トランスミッション部品、ベアリング、ギア、シール、ブレーキシステムなど(軽量化、耐熱性、耐摩耗性が求められる部品)
- 航空宇宙産業: 航空機部品(軽量化、燃費向上)、コネクター、タービンブレード、配管パイプなど
- 医療分野: インプラント、義歯、外科用器具、内視鏡先端部品、医療チューブ、滅菌トレーなど(生体適合性、耐熱性、耐薬品性、滅菌耐性が求められる)
- 半導体関連分野: ウェハーキャリア、リテーナーリング、搬送容器、絶縁部品など(耐熱性、耐薬品性、耐プラズマ性、低アウトガス性が求められる)
- 化学工業: ポンプ部品、バルブ、配管、シール、パッキンなど(耐薬品性、耐熱性が求められる)
- 電子・電気産業: コネクタ、絶縁フィルム、プリント基板、高温コネクタ、ウエハーキャリアなど(電気絶縁性、耐熱性が求められる)
- その他: 食品加工機器部品、耐熱食器トレイ、油田・ガス田採掘機器部品など
PEEK樹脂は、その多岐にわたる優れた特性から、金属や他の汎用プラスチックでは対応できないような、特に厳しい環境下での代替材料として注目されています。しかし、その高性能ゆえに他のプラスチックと比較して高価である点がデメリットとして挙げられます。
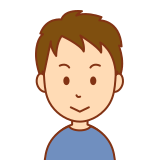
PEEK樹脂は「ポリエーテルエーテルケトン」の略で、耐熱性、機械的強度、耐薬品性、軽量性に優れたスーパーエンジニアリングプラスチックです。250℃以上の連続使用が可能で、医療、航空宇宙、自動車、半導体など、過酷な環境で使われる部品に活用されます。
なぜ生体適合性に優れるのか
PEEK樹脂が生体適合性に優れる主な理由は、その化学的安定性と不活性さにあります。具体的には以下の点が挙げられます。
- 体内での安定性(不活性性):
- PEEK樹脂は非常に安定した化学構造を持ち、体液や組織と反応しにくい「不活性」な性質を持っています。
- 体内で分解されたり、有害な物質を溶出したりすることが極めて少ないため、生体にとって異物として認識されにくく、拒絶反応や炎症を引き起こしにくいです。
- 細胞毒性や遺伝毒性、免疫原性を示さないことが確認されています。
- 高い耐薬品性:
- 体液や血液、また医療現場で用いられる消毒液や薬品など、様々な化学物質にさらされても劣化しにくい耐薬品性を持っています。これにより、長期間にわたって体内環境でその性能を維持できます。
- 優れた滅菌耐性:
- 医療機器は厳格な滅菌が必須ですが、PEEKは高温高圧のオートクレーブ滅菌や、ガンマ線滅菌など、多様な滅菌方法に耐えることができます。これにより、繰り返し滅菌しても材料の劣化が少なく、安全性を保つことができます。
- 骨に近似した機械的特性(一部グレード):
- 特にインプラント用途では、PEEKの弾性率(材料の硬さの指標)が人間の皮質骨に比較的近いという特徴があります。チタンなどの金属と比較して柔軟性があり、骨との親和性が高いとされています。これにより、骨にかかる荷重を適切に分散し、ストレスシールディング(金属インプラントが硬すぎることにより周囲の骨が弱くなる現象)のリスクを低減する可能性が期待されています。
これらの特性から、PEEK樹脂は医療分野、特に整形外科(脊椎インプラント、人工関節など)、歯科(義歯、インプラント上部構造など)、外科用器具、カテーテル、内視鏡部品など、人体と接触する、あるいは体内に埋め込まれる様々な用途で広く採用されています。
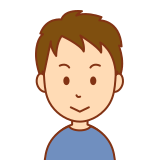
PEEK樹脂は、体液や組織と反応しにくい高い化学的安定性と不活性性を持ちます。これにより体内での分解や有害物質の溶出が極めて少なく、拒絶反応や炎症を引き起こしにくいため、生体適合性に優れます。
PEEK樹脂を3Dプリンターで成形できる利点は
PEEK樹脂を3Dプリンターで成形する利点は、その高性能な特性を活かしつつ、従来の加工方法では難しかったメリットを享受できる点にあります。
主な利点は以下の通りです。
- 複雑な形状の自由な造形:
- 射出成形では不可能な中空構造やハニカム構造、内部が入り組んだ複雑な形状でも一体で造形できます。これにより、部品の軽量化や機能統合、性能向上が実現できます。
- 切削加工では工具が届かないようなアンダーカットのある形状も可能です。
- 材料ロスの大幅な削減とコスト低減:
- 切削加工のように材料を削り出すのではなく、必要な部分にのみ材料を積層するため、材料ロスがほとんど発生しません。高価なPEEK樹脂にとって、これは大きなコストメリットになります。
- リードタイムの短縮と内製化:
- 金型製作が不要なため、開発・試作段階での部品製作が迅速に行えます。設計変更にも柔軟に対応でき、製品開発期間を大幅に短縮できます。
- 外注に頼らず自社内で製造できるため、サプライチェーンの柔軟性が向上し、必要な時に必要な数を製造できます(在庫問題の解消)。
- カスタマイズ性と小ロット生産への対応:
- 個々の患者に合わせた医療用インプラントや、特定の装置に最適化されたカスタム部品など、多品種少量生産や一点物の製造に非常に適しています。
- 機能統合と部品点数の削減:
- 複数の部品を一体として造形することで、アセンブリ工程の削減、部品点数の削減、それに伴うコスト削減や信頼性向上が期待できます。
- 試作から最終製品への移行が容易:
- 試作段階で3Dプリンターで造形したPEEK部品をそのまま最終製品として使用できる場合があり、試作と量産の間での材料特性のギャップを小さくできます。
PEEK樹脂は非常に高い耐熱性を持つため、3Dプリンターでの造形にはノズルやチャンバーの高温制御など特殊な技術が必要ですが、これらの課題が克服されつつあることで、PEEKの持つ優れた特性をより手軽に、そして多様な形状で活用できるようになってきています。
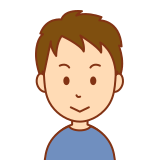
PEEK樹脂を3Dプリンターで成形する利点は、複雑な形状を金型不要で造形できる点です。これにより、材料ロスを減らし、開発・製造リードタイムを大幅に短縮。医療用インプラントなど、少量多品種のカスタム部品製作に特に有効です。
どのような応用例が考えられるのか
PEEK樹脂を3Dプリンターで成形した応用例は多岐にわたり、その高性能な特性と3Dプリンターの自由な造形能力が融合することで、様々な分野で革新的なソリューションが生まれています。
主な応用例を以下に示します。
1. 医療分野
- インプラント(脊椎、頭蓋骨、歯科など): PEEKは生体適合性に優れ、骨に近い弾性率を持つため、人工椎間板、頭蓋骨の欠損部を補うインプラント、義歯のフレームなどに3Dプリンターでカスタマイズされた形状が作られます。患者一人ひとりの骨格に合わせた高精度なインプラントが製作でき、治癒の促進や患者のQOL(生活の質)向上に貢献します。
- 手術用ガイド・治具: 患者固有の形状に合わせて3Dプリンターで作成されたPEEK製のガイドや治具は、手術の精度向上や時間の短縮に役立ちます。滅菌が可能である点も重要です。
- 義肢装具: 軽量で高強度、耐摩耗性に優れるPEEKは、義手や義足の部品、装具などに利用され、フィット感や耐久性を向上させます。
- 医療機器部品: 高温滅菌に耐える特性から、手術器具の一部や滅菌トレー、分析装置の部品などに活用されます。
- 総義歯: 従来の材料では難しかった、PEEK樹脂を用いた総義歯の開発も進められています。
2. 航空宇宙分野
- 軽量化部品: 航空機の燃料効率向上のため、金属部品の代替としてPEEK製の軽量部品が採用されます。ブラケット、コネクター、ダクト、内部構造部品など、複雑な形状でも強度を保ちつつ軽量化が図れます。
- 耐熱・耐薬品性部品: エンジン周辺や油圧システムなど、高温や化学薬品に曝される環境で使用される部品に適用されます。
3. 自動車分野
- エンジン周辺部品: 高温にさらされるエンジンルーム内の部品(ギア、ベアリング、ワッシャーなど)に、金属代替として利用され、軽量化と耐久性向上に貢献します。
- 燃料システム部品: 耐薬品性や耐熱性が求められる燃料系の部品に採用されます。
- 軽量構造部品: 車体の軽量化のため、さまざまな構造部品に応用され、燃費向上や走行性能向上に寄与します。
4. 半導体製造装置分野
- ウェハーキャリア・リテーナーリング: 高温や薬品、プラズマに耐える特性から、半導体製造工程で使用されるウェハーを搬送するキャリアや、プロセスチャンバー内の部品に利用されます。アウトガス(ガス発生)が少ないことも重要です。
- 絶縁部品: 高い電気絶縁性も活用され、様々な電気・電子部品の絶縁体として使用されます。
- 真空用部品: 一般的に樹脂が使用しにくい真空環境でも、PEEKはアウトガスが少ないため、3Dプリンターで成形された部品が真空チャンバー内で使用される事例も出ています。
これらの応用例は、PEEK樹脂の優れた特性と、3Dプリンターによる自由な形状設計・小ロット生産能力が組み合わされることで、これまでの製造方法では実現が困難だった高機能部品の製造を可能にしています。
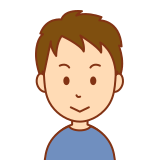
PEEK樹脂の3Dプリンターでの応用例は、医療分野(患者に合わせたインプラントや手術ガイド)、航空宇宙・自動車分野(軽量・高強度部品)、半導体製造装置(耐熱・耐薬品性部品)など、高性能が求められる多様な産業で複雑なカスタム部品製作に活用されています。
コメント