この記事で分かること
- チタンとタンタルの使い分け:現在の最先端プロセスでは、銅配線のバリアメタルとしてはTa/TaNが標準となっています。しかし、デバイスの構造や要求される特性によっては、Ti/TiNがコンタクトホールや下地層として独自の役割を果たす形で共存しています。
- コンタクトホールとは:半導体デバイスにおいて、シリコン基板上のトランジスタ電極(ソース、ドレイン、ゲート)と、その上層の金属配線を電気的に接続するために開けられる穴です。
バリアメタルとしてのチタン
半導体の重要性が増す中で、前工程装置は世界的に成長が続いています。
https://optronics-media.com/news/20250414/99245/
特に中国は米中対立もあり、大幅な投資増加が続いています。今後も先端技術を駆使した半導体の需要増加と従来技術による成熟プロセスともにその重要性は増加するとみられています。
今回はバリアメタルとして使用されるチタンについての解説となります。
半導体の前工程とは
半導体の前工程とは、シリコンウェハ上にトランジスタや配線などの微細な回路を形成する一連のプロセスのことです。ウェハを素材として、集積回路を作り込んでいく、半導体製造の最も重要な部分と言えます。非常に多くの精密な工程を経て、最終的な半導体チップの機能が決まります。
主な前工程は以下の通りです。
ウェハ準備
シリコンインゴットの製造: 高純度のシリコンを溶解し、種結晶を用いて単結晶のシリコンインゴットを育成します。
- スライス: インゴットを薄い円盤状(ウェハ)にスライスします。
- 研磨: ウェハ表面を平坦かつ滑らかに研磨します。
- 洗浄: ウェハ表面の微細な異物や汚れを徹底的に除去します。
成膜
ウェハ表面に、酸化膜、窒化膜、金属膜など、様々な薄膜を形成します。
- 成膜方法には、CVD(化学気相成長法)、スパッタリング(物理気相成長法)、ALD(原子層堆積法)などがあります。
フォトリソグラフィ
ウェハ表面に感光材(フォトレジスト)を塗布します。
- 回路パターンが描かれたマスク(フォトマスク)を通して紫外線を照射し、レジストにパターンを焼き付けます。
- 現像液で不要なレジストを除去し、ウェハ上に回路パターンを形成します。
エッチング
フォトリソグラフィでパターン形成されたレジストをマスクとして、露出した成膜を除去し、ウェハに回路パターンを転写します。
- エッチングには、液体を用いるウェットエッチングと、プラズマを用いるドライエッチングがあります。
不純物導入(ドーピング)
半導体特性を持たせるために、リンやボロンなどの不純物をウェハ中に注入します。
- イオン注入法などが用いられます。
平坦化(CMP: Chemical Mechanical Polishing)
表面の凹凸をなくし、平坦にするための処理です。
- 化学的な腐食と 研磨を同時に行います。
配線形成(メタライゼーション)
形成されたトランジスタなどの素子間を金属配線で接続します。
- スパッタリングなどで金属膜を形成し、フォトリソグラフィとエッチングで配線パターンを作ります。
これらの工程を何度も繰り返し行うことで、複雑な集積回路がウェハ上に形成されます。前工程は、半導体の性能や品質を大きく左右する、非常に重要なプロセスです。
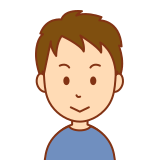
前工程は、微細な回路を形成する一連のプロセスのことで、半導体の性能や品質を大きく左右する、非常に重要なプロセスです。
バリアメタルとは何か
半導体前工程におけるビアホール(via hole)の充填において、バリアメタルは極めて重要な役割を担っています。特に、銅(Cu)配線が主流となっている現在の半導体プロセスでは、その重要性が増しています。
バリアメタルの役割
バリアメタルの主な役割は以下の通りです。
- 銅の拡散防止(バリア機能): 銅は電気伝導性に優れていますが、シリコン(Si)や層間絶縁膜(Interlayer Dielectric, ILD)中に容易に拡散するという特性があります。銅が拡散すると、デバイスの電気特性を劣化させたり、リーク電流を引き起こしたり、信頼性を著しく低下させたりする原因となります。バリアメタルは、この銅の拡散を防ぐための「壁」として機能します。
- 銅と絶縁膜の密着性向上: 銅と層間絶縁膜の間には、密着性が悪いという問題があります。バリアメタルは、銅と絶縁膜の間に介在することで、両者の密着性を向上させ、配線の剥離などを防ぎます。
- 銅のシード層(seed layer)との密着性向上: ビアホールの銅充填は通常、めっきプロセスで行われます。めっきの前に、銅のシード層を形成しますが、このシード層とバリアメタルとの密着性も重要です。
- エレクトロマイグレーション(EM)耐性の向上: 銅配線では、高電流密度下で原子が移動し、配線の断線やショートを引き起こすエレクトロマイグレーションが問題となります。バリアメタルは、銅のEM耐性を向上させる効果も期待されています。
主なバリアメタル材料
現在、主に用いられているバリアメタル材料は以下の通りです。
- タンタル(Ta)/窒化タンタル(TaN): 銅配線のバリアメタルとして最も広く用いられています。TaNはTaに比べて拡散防止能力が高く、Taと組み合わせて使用されることが多いです。
- チタン(Ti)/窒化チタン(TiN): かつてアルミ(Al)配線で広く使われていましたが、銅配線でもバリアメタルや接着層として用いられることがあります。特に、TiNは銅との密着性やバリア性に優れる場合があります。
これらの材料は、一般的に高融点金属であり、化学的に安定していることが求められます。
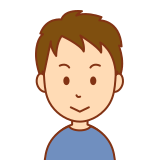
バリアメタルは、半導体配線において、銅(Cu)などの金属が周囲のシリコンや絶縁膜へ拡散するのを防ぐ薄い層です。配線材料と他の層との密着性を高め、電気特性の劣化や信頼性低下を防ぐ重要な役割を担います。
タンタルとチタンはどう使い分けるのか
半導体前工程のビアホール充填におけるバリアメタルとして、タンタル(Ta)とチタン(Ti)はそれぞれ異なる特性を持ち、用途やプロセスの要求に応じて使い分けられています。
タンタル(Ta)および窒化タンタル(TaN)
- 主な用途: 主に銅(Cu)配線のバリアメタルとして、現在の半導体プロセスで最も広く利用されています。
- 特徴:
- 優れた銅拡散防止能力: タンタルおよびその窒化物であるTaNは、銅原子のシリコンや層間絶縁膜への拡散を非常に効果的に阻止します。TaNはTaよりも拡散防止能力が高いとされています。
- 高い熱安定性: 高い熱処理温度にも耐えることができます。
- 良好な銅との密着性: 銅との密着性が比較的良好です。
- 低抵抗: 純粋なタンタルは比較的に抵抗が低いですが、TaNは抵抗がやや高くなります。しかし、バリア層としては十分許容範囲内です。
- エレクトロマイグレーション(EM)耐性向上: Ta/TaNバリアメタルは、Cu配線のエレクトロマイグレーション耐性を向上させる効果も報告されています。
- 成膜性:
- 主にスパッタリング(PVD)で成膜されますが、微細なビアホールへの均一なカバレッジが課題となることがあります。IMP(Ion Metal Plasma)や将来的なALD(Atomic Layer Deposition)の適用が進んでいます。
- 使い分けのポイント: 銅配線が主流である現在の先端プロセスにおいて、主要なバリアメタルとして選択されます。特に、銅の拡散という深刻な問題に対して、その優れたバリア機能が不可欠です。
チタン(Ti)および窒化チタン(TiN)
- 主な用途:
- かつてはアルミニウム(Al)配線におけるバリアメタルや密着層として広く用いられていました。
- 現在の銅配線においても、完全に使われなくなったわけではなく、特にコンタクトホールにおけるコンタクト抵抗低減のための層として、またはTiNとTa/TaNを積層して使用されるケースがあります。
- コンタクトホールでは、シリサイド(TiSi2)を形成してシリコンとのオーミック接触を改善し、コンタクト抵抗を低減する役割も果たします。
- 特徴:
- 良好なシリコンとの反応性: シリコンと反応してチタンシリサイド(TiSi2)を形成し、コンタクト抵抗を低減する効果があります。これが、コンタクトホールでTiが使われる主要な理由です。
- 優れた密着性: 特にSiやSiO2といった材料への密着性に優れています。
- 銅拡散防止能力: Ta/TaNに比べると、純粋なTiの銅拡散防止能力は限定的です。しかし、TiNは一定のバリア機能を持っています。
- 成膜性: PVD(スパッタリング)やCVD(Chemical Vapor Deposition)で成膜されます。TiNはCVDでの成膜も可能であり、良好なカバレッジが得られる場合があります。
- 使い分けのポイント:
- コンタクトホールで、シリコン基板との良好なオーミック接触(低抵抗)を確保する必要がある場合に、Ti/TiNが選択されることが多いです。TiをSiと反応させてTiSi2を形成し、その上にTiNをバリア層として積層するような構造が一般的です。
- 銅配線においては、Ta/TaNがメインのバリア層として使われる一方で、その下地や特定の目的のためにTiNが補助的に用いられることがあります。例えば、TiN層を介してTaN層を成膜することで、密着性の向上や複合的なバリア効果を狙う場合などです。
まとめると
特性/用途 | タンタル(Ta)/窒化タンタル(TaN) | チタン(Ti)/窒化チタン(TiN) |
主要用途 | 銅(Cu)配線における銅拡散防止バリア | コンタクトホールにおける低抵抗化(TiSi2形成)、Al配線のバリア |
バリア性 | 非常に高い(特にCuに対して) | TiNは一定のバリア性を持つが、Cuに対してはTa/TaNに劣る |
Siとの反応性 | 低い | 高い(TiSi2を形成) |
密着性 | 銅、層間絶縁膜に対して良好 | シリコン、酸化膜に対して良好 |
抵抗 | Taは比較的低く、TaNはやや高め | Tiは比較的低く、TiNはやや高め |
成膜法 | 主にPVD(スパッタリング、IMP)、将来的にALD | PVD、CVD |
現在の最先端プロセスでは、銅配線のバリアメタルとしてはTa/TaNが標準となっています。しかし、デバイスの構造や要求される特性によっては、Ti/TiNがコンタクトホールや下地層として独自の役割を果たす形で共存しています。最適なバリアメタルの選択は、配線材料、アスペクト比、熱処理条件、そして最終的なデバイス性能要求など、多岐にわたる要因を考慮して決定されます。
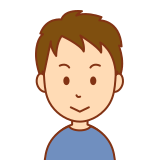
タンタル(Ta)とチタン(Ti)はそれぞれ異なる特性を持ち、用途やプロセスの要求に応じて使い分けられていますが、現在はタンタルが使用されることが一般的です。
コンタクトホールとは何か
半導体デバイスにおける「コンタクトホール」とは、シリコン基板上のトランジスタ(ゲート、ソース、ドレインなど)の電極と、その上層に形成される金属配線層とを電気的に接続するための穴のことです。
半導体デバイスは、シリコンウェハー上に何層もの薄膜を積層して作られています。トランジスタなどのデバイス要素はシリコン基板表面に形成され、その上に電気配線(ワイヤー)が形成されます。しかし、これらの配線層は通常、電気的に絶縁された層間絶縁膜(Interlayer Dielectric, ILD)によって分離されています。
この絶縁された層を貫通し、下の電極と上の配線を繋ぐために、選択的に穴を開ける必要があります。この穴が「コンタクトホール」です。
コンタクトホールの重要性
- 電気的接続: トランジスタで処理された信号や電力を、デバイス内部の他の部分や外部へ伝えるための導電経路を提供します。
- 低抵抗化: コンタクトホールを介した接続部分の電気抵抗は、デバイス全体の性能に大きく影響します。できるだけ低抵抗にすることが求められます。
- 信頼性: 安定した接続は、デバイスの長期的な信頼性を保証するために不可欠です。
コンタクトホールの形成プロセス
一般的なコンタクトホールの形成プロセスは以下のようになります。
- 層間絶縁膜の堆積: シリコン基板上のトランジスタやゲート電極の上に、まず絶縁膜(例:SiO2、Low-k膜など)が形成されます。
- レジスト塗布・露光・現像: コンタクトホールを開けたい部分だけを残すように、感光性樹脂(レジスト)を塗布し、フォトリソグラフィ技術を用いてパターンを転写します。
- エッチング: レジストをマスクとして、露出した絶縁膜をエッチング(削り取る)して、シリコン基板上の電極まで穴を開けます。この際、アスペクト比(深さ/幅)が高い微細な穴を正確に形成することが非常に重要です。
- レジスト除去: エッチングが完了したら、残ったレジストを除去します。
- バリアメタル/接着層の成膜: 穴の内壁に、バリアメタル(例:Ti/TiN)や接着層を薄く成膜します。これは、その後に埋め込む金属がシリコン基板へ拡散するのを防ぎ、また、埋め込む金属との密着性を高めるためです。特に、シリコン基板との接触抵抗を低減するために、チタンシリサイド(TiSi2)を形成する目的でチタン(Ti)層が用いられることが多いです。
- 導電性材料の充填: 開けられた穴の中に、タングステン(W)や、場合によっては銅(Cu)などの導電性材料を埋め込みます。タングステンは高アスペクト比の穴埋めにCVD法(Chemical Vapor Deposition)が適しており、耐熱性も高いため、コンタクトホールのプラグ(埋め込み金属)として広く使われています。
- CMP(Chemical Mechanical Polishing): 余分な導電性材料を研磨(CMP)して除去し、コンタクトホールの中にだけ導電性材料を残します。これにより、表面が平坦化され、次の配線層の形成準備が整います。
コンタクトホールとビアホールの違い
似たような概念に「ビアホール(via hole)」があります。
- コンタクトホール: シリコン基板上のアクティブ領域(トランジスタのソース、ドレイン、ゲートなど)と、最初の金属配線層とを接続する穴を指すことが多いです。
- ビアホール: 複数の金属配線層の間(例えば、第1層の金属配線と第2層の金属配線)を接続する穴を指します。
このように、接続する階層が異なるため、名称が使い分けられています。ただし、広義には両方をまとめて「ホール」と呼ぶこともあります。
半導体の微細化が進むにつれて、コンタクトホールのサイズはますます小さく、深くなっています(高アスペクト比化)。これにより、穴の内壁に材料を均一に成膜したり、完全に埋め込んだりすることが非常に難しくなっており、半導体製造技術の重要な課題の一つとなっています。
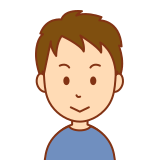
コンタクトホールは、半導体デバイスにおいて、シリコン基板上のトランジスタ電極(ソース、ドレイン、ゲート)と、その上層の金属配線を電気的に接続するために開けられる穴です。絶縁膜を貫通し、導電性材料で埋められます。
コメント