この記事で分かること
- 製造技術の知識構造化型データベースとは:製造現場で長年培われてきた技や経験則、ノウハウなどをコンピュータが理解・活用しやすいように体系的に整理した、データベースのことです。
- なぜ、重要か:技術の伝承を続け、属人化を防ぐ、デジタル化を推進するために重要性が増しています。
- データの収集法:IoT/センサーによるリアルデータの取得、既存のデジタルデータの統合、 暗黙知・形式知の明示化と構造化などでデータの収集を行います。
次世代ものづくり実装研究センター
産業技術総合研究所(産総研)は、2025年4月に「実装研究センター」を新設し、社会課題の解決に向けた技術の社会実装を加速する取り組みを開始しました。
https://www.aist.go.jp/aist_j/news/au20250401_2.html
産総研の第6期中長期目標では、「エネルギー・環境・資源制約への対応」「人口減少・高齢化社会への対応」「レジリエントな社会の実現」の3つの社会課題の解決が掲げられています。
これらの課題に取り組むため、7つの実装研究センターが設立され、所内の研究成果を結集し、産総研の総合力を最大限に生かした研究開発を推進していくとしています。
今回は次世代ものづくり実装研究センターの製造技術の知識構造化型データベースの構築についての解説となります。
次世代ものづくり実装研究センターとは何か
産総研(国立研究開発法人産業技術総合研究所)の次世代ものづくり実装研究センターは、2025年4月に新設された7つの実装研究センターの一つです。
このセンターの主な目的は、以下のような取り組みを通じて、次世代のものづくりシステムを構築し、生産性向上と高度人材の育成を目指すことです。
主な活動内容・研究テーマ:
製造サイバーフィジカルシステム(CPS)の研究開発
- AI技術、DX技術、ロボット技術などを活用し、物理空間と情報空間を高度に融合させた製造システムを構築します。
- ロボットや工作機械、AI、デジタルツインなどを連携させることで、より効率的で高度なものづくりを実現します。
製造技術の知識構造化型データベースの構築
- 製造現場で培われてきたノウハウや加工現象のモデル化、データ化を進め、デジタルものづくりを推進するための基盤を構築します。
データ駆動型加工データ統合・活用
- 加工された材料の特性とミクロ組織との関係性の解明や、加工現象の観察によるモデル化などを通じて、データに基づいた効率的な加工技術を開発します。
ロボットソフトウェアプラットフォームの研究開発
- ロボットの命令系統やプログラム言語をオープンミドルウェアを使って統一・標準化を進め、異種のロボットやシステム間の連携を容易にします。
高機能部材開発
- 形状・材料特性と異分野プロセスを融合させた高機能部材の開発に取り組んでいます。光機能や濡れ性、摩擦特性などの機能制御を目指します。
高度ものづくり人材の育成
- 人口減少や高齢化社会に対応するため、生産性向上と同時に高度なものづくり人材の育成が急務とされており、これにも貢献することを目指しています。
拠点
次世代ものづくり実装研究センターは、以下の3つの研究拠点に設置されています。
- 臨海副都心センター(東京)
- つくばセンター(茨城)
- 北陸デジタルものづくりセンター(石川)
背景と意義
産総研は、研究成果の社会実装を通じて、社会課題の解決と産業競争力の強化を目指しており、この次世代ものづくり実装研究センターは、その一環として、日本のものづくり産業が直面する課題(人口減少、高齢化、国際競争力の強化など)に対応し、新たな価値を創出するための重要な役割を担っています。
産学官連携を強化し、技術の実用化と普及を推進していく方針です。
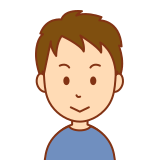
次世代ものづくり実装研究センターは様々な次世代のものづくりシステムを構築することで、生産性向上と高度人材の育成を目指す取り組みです。
製造技術の知識構造化型データベースの構築とは何か
製造技術の知識構造化型データベースの構築とは製造現場で長年培われてきた熟練工の「匠の技」や、複雑な加工現象に関する経験則、あるいは設計・開発段階で得られるノウハウなど、これまで暗黙知として扱われたり、文書として散逸したりしていた製造に関するあらゆる「知識」を、コンピュータが理解・活用しやすいように体系的に整理し、データベースとして構築することです。
データベースの構築化が必要な理由
その背景には、以下のような課題があります。
- 熟練工の高齢化と技術継承の困難: 日本の製造業では、熟練工の高齢化が進み、彼らが持つ高度な技術やノウハウが失われる危機に直面しています。これらの知識は経験に基づいており、言葉や文書だけでは伝えきれない「暗黙知」が多いのが現状です。
- 属人化による生産性の低下: 特定の個人の知識や経験に頼りすぎると、その人がいないと作業が進まない、あるいは品質が安定しないといった属人化の問題が発生します。
- データと知識の断絶: 製造現場では様々なデータ(センサーデータ、検査データなど)が蓄積されていますが、これらのデータが「なぜそのような結果になったのか」という背景にある知識と結びついていないため、十分な活用ができていない場合があります。
- デジタルものづくりへの移行の遅れ: サイバーフィジカルシステム(CPS)やAIを活用したスマートファクトリーを実現するためには、物理空間のデータだけでなく、そのデータが意味する「知識」をデジタル化し、コンピュータが判断・推論できるようにする必要があります。
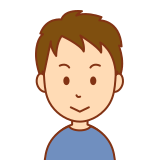
製造技術の知識構造化型データベースの構築とは製造現場で長年培われてきた技や経験則、ノウハウなどをコンピュータが理解・活用しやすいように体系的に整理し、データベースとして構築することです。
技術の伝承を続け、属人化を防ぐ、デジタル化を推進するために重要性が増しています。
具体的な内容はどのようなものか
このデータベースは、単にデータを羅列するだけでなく、知識間の関係性や階層構造、意味合いを明確にした形で整理されます。具体的には、以下のような要素が含まれると考えられます。
たとえば、溶接時のアークの状態から「今、溶け込みが足りない」と判断する際の、アークの見た目、音、匂いといった五感で捉える情報とその対応など。
加工条件と結果の因果関係
- 例:「この材料をこの形状に加工するには、この工具で、この回転数、送り速度、切削深さで加工すると、最適な表面粗さが得られる。」といった具体的な加工レシピとその理由、結果。
- 「なぜこの条件だと良いのか/悪いのか」という知見や、その条件を選定した思考プロセスなども含みます。
材料特性と加工性の関係
- 例:特定の材料の結晶構造や硬度が、切削抵抗や溶接品質にどう影響するか、といった物理的な知識。
設備特性とパフォーマンス
- 例:特定の工作機械の剛性や熱変位が、加工精度にどう影響するか、といった機械固有の特性に関する知識。
不良モードと原因・対策
- 例:特定の不良品が発生した場合、その原因として考えられる加工条件、材料不良、設備異常などを体系的に分類し、それぞれの対策方法や過去の事例を紐付けます。
設計意図と製造制約
- 製品の設計段階での意図(例:特定の機能や性能を実現するため)が、製造工程でどのような制約を受けるか(例:この形状は現行の設備では加工できない)、その解決策は何か、といった情報。
熟練工の判断基準とノウハウ
- 熟練工が特定の状況下でどのような判断を下し、どのような微調整を行うのか、その判断基準や感覚的なノウハウを、可能な限り言語化・数値化・モデル化して表現します。
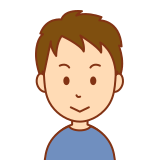
データベースでは、データを羅列するだけでなく、知識間の関係性や階層構造、意味合いを明確にした形で整理されます。暗黙知や経験則で行われてきたことがなぜそうなるのかを含め改めて解析することが可能となります。
データの蓄積はどのように行うのか
データの蓄積方法は、以下のように、多岐にわたる方法が用いられると考えられます。
1. リアルタイムデータ収集(IoT/センサーデータ)
これは、製造現場の物理空間から直接データを取得する最も基本的な方法です。
- センサーの活用
- 工作機械: スピンドルの回転数、送り速度、切削抵抗、トルク、温度、振動、電流、クーラント流量など。
- ロボット: 動作座標、関節トルク、アーム速度、把持力、ビジョンデータなど。
- 生産ライン: 製品の位置情報(RFID、バーコード)、通過時間、搬送速度、温湿度、圧力、流量など。
- 材料: 入力材料のロット番号、供給速度、保管条件など。
- 品質検査: 寸法、形状、表面粗さ、画像データ、音響データなど。
- データ収集の仕組み
- IoTゲートウェイ: センサーからのデータを集約し、クラウドやエッジサーバーに送信するデバイス。
- 産業用ネットワーク: EtherCAT, PROFINET, CC-Link IE Fieldなど、高速・高信頼性の産業用通信プロトコルを利用してデータを伝送。
- MQTT, OPC UA: 異種デバイス間のデータ連携を容易にするプロトコル。
- データの種類: 時系列データ、数値データ、画像データ、音声データなど。
2. 既存のデジタルデータの統合
これまでデジタル化されてきたが、必ずしも一元的に管理されていなかったデータも重要な情報源です。
- CAD/CAM/CAEデータ
- 設計データ(CAD): 製品の形状、寸法、材料、公差情報。
- 加工プログラム(CAM): NCプログラム、ロボットプログラム。
- 解析データ(CAE): 強度解析、熱解析、流体解析の結果。
- 生産管理システム(MES/ERP)のデータ
- 生産計画、進捗状況、設備稼働状況、資材管理、在庫情報、人員配置など。
- 品質管理システムのデータ
- 検査結果、測定データ、不良履歴、ロット情報、トレーサビリティデータ。
- 設備管理システムのデータ
- 設備ごとの稼働履歴、メンテナンス履歴、故障履歴、部品交換履歴。
- 過去の実験・研究データ
- R&D部門で蓄積された各種実験データ、シミュレーション結果。
3. 暗黙知・形式知の明示化と構造化
熟練工の持つノウハウや文書化されていない知識を、コンピュータが理解できる形に変換し、構造化されたデータベースに蓄積します。これが「知識構造化型データベース」の核となる部分です。
- ヒアリング/インタビュー: 熟練工や技術者から、作業手順、判断基準、トラブルシューティングのノウハウ、加工時の「勘所」などを丁寧に聞き取り、言語化します。
- 作業観察/ビデオ解析: 実際の作業風景を観察し、どのような動作や判断が行われているかを記録・分析します。ビデオデータは、後から繰り返し分析するのに有効です。
- 専門家による知識モデリング: 収集した情報に基づいて、オントロジー(概念間の関係性定義)、知識グラフ(概念と関係性のネットワーク)、ルールベース(IF-THEN形式の条件と結果)などの形式で知識をモデル化します。
- テキストマイニング/自然言語処理(NLP): 既存の報告書、日報、技術文書、マニュアル、メールなどの非構造化テキストデータから、キーワード抽出、関連性分析、意味解析を行い、暗黙的に含まれる知識を洗い出し、構造化データに変換します。
- ベテランの判断をデータ化: 特定の状況(例:切削音がいつもと違う)に対して、ベテランがどのように判断し、どのような調整を行ったか、その判断に至るまでの五感情報や思考プロセスを記録し、データ化します。
- シミュレーションと連動した知見の蓄積: デジタルツイン上でシミュレーションを行った結果、最適な条件や予期せぬ挙動が判明した場合、その知見もデータベースに知識として追加します。
4. 外部データの活用
関連する外部情報も、知識データベースを豊かにするために利用されます。
- 学術論文・研究成果: 最先端の研究知見、物理現象のモデルなど。
- 材料データベース: 標準的な材料特性、サプライヤー情報。
- 国際規格・業界標準: 製造プロセスや製品の仕様に関する規格情報。
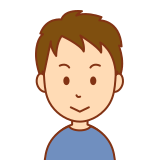
IoT/センサーによるリアルデータの取得、既存のデジタルデータの統合、 暗黙知・形式知の明示化と構造化などでデータの収集を行います。
コメント