この記事で分かること
直接接合とは:半導体チップやウエハーを接着剤やはんだなどの介在物させずに、直接、原子レベルで結合させる技術のことです。
メリット:チップ間の接続ピッチを大幅に短縮できるため、さらなる微細化、高密度化や異種材料の接合を可能になります。
工程と重要な点:チップ同士を作成し、位置合わせを行った後、加熱や加温で接合を行っています。表面を極めて高いレベルで洗浄できるか、超高精度での位置合わせができるかなどがポイントといえます。
キヤノンマシナリーの半導体チップの直接接合
キヤノンマシナリーは、半導体製造の後工程における重要な技術の一つである「接合」において、様々な装置を提供しています。
特に、半導体チップ同士の「直接接合」に繋がる技術の実用化に力を入れており、来年以降の実用化を検討しています。
https://www.nikkan.co.jp/articles/view/00749987
チップの直接接合とは何か
「直接接合」とは、半導体チップやウエハーを、接着剤やはんだなどの介在物をほとんど、あるいは全く使わずに、直接、原子レベルで結合させる技術のことです。これは、半導体デバイスの高性能化、高密度化、低消費電力化を実現するための重要な技術として注目されています。
直接接合の仕組み
主な直接接合の仕組みは以下の通りです。
- 表面活性化: 接合する両方の半導体表面を、プラズマ処理やイオンビーム照射などによって清浄化し、表面に存在する酸化膜や有機物などを除去します。これにより、表面の原子が活性化され、他の原子と結合しやすい状態になります。
- 密着: 活性化された表面同士を極めて高い精度で密着させます。この際、表面の平坦性や清浄度が非常に重要になります。
- 化学結合の形成: 密着した表面の原子間に、ファンデルワールス力、水素結合、または共有結合などの化学結合が形成されます。
- 常温接合 (フュージョンボンディング、分子接合): 表面に水酸基(OH基)などを形成し、常温で密着させることで水素結合やファンデルワールス力によって仮接合し、その後、熱処理を加えることで強固な共有結合を形成する方法です。
- 表面活性化接合: 真空中で原子ビームなどを照射して表面を活性化させ、そのまま真空中で接触させることで、原子間の凝着力を利用して常温または低温で接合する方法です。熱膨張係数差の大きい材料間でも接合が可能です。
- ハイブリッドボンディング: 金属配線(銅など)と絶縁体(酸化シリコンなど)を同一面上に形成し、これらを同時に直接接合する技術です。金属配線間の電気的接続と、絶縁体間の機械的・電気的絶縁を一度に行うことができ、より高密度な接続を可能にします。
直接接合の種類
直接接合は、接合する対象によって大きく以下の2つに分けられます。
- ウエハー直接接合 (Wafer-to-Wafer Direct Bonding): 2枚の半導体ウエハーを丸ごと直接接合する方法です。主に、MEMS(微小電気機械システム)デバイスの製造、3D積層メモリ、SOI(Silicon On Insulator)ウエハーの製造などに用いられます。
- チップ直接接合 (Die-to-Wafer / Die-to-Die Direct Bonding): 個々に切り分けられた半導体チップ(ダイ)を、別のウエハーや他のチップに直接接合する方法です。特に、Known Good Die(良品チップ)だけを接合することで、歩留まりの向上や、異なる種類のチップを組み合わせるヘテロジニアスインテグレーション(異種積層)が可能になります。
直接接合のメリット
- 高密度化・微細化: 従来のワイヤーボンディングやはんだバンプに比べて、より微細な接続が可能になり、チップ間の接続ピッチを大幅に短縮できます。これにより、デバイスの小型化、高集積化に貢献します。
- 高性能化・高機能化: 信号伝送経路が短くなるため、電気抵抗や寄生容量が低減され、信号遅延が少なくなり、デバイスの高速化や低消費電力化が実現します。
- 3D積層: 複数のチップを縦方向に積層する3Dパッケージングにおいて、チップ間の高密度で効率的な接続を可能にします。
- 異種材料の接合: 熱処理を必要としない常温接合などの技術により、熱膨張係数の異なる材料や、熱に弱い材料同士の接合が可能になります。これにより、多様な機能を持つデバイスの統合が促進されます。
- 高い信頼性: 接着剤などの異物がないため、熱応力による剥離や信頼性の低下のリスクが低減されます。
直接接合のデメリット・課題
- 高い表面清浄度と平坦性: 原子レベルでの結合を達成するためには、接合面の極めて高い清浄度と平坦性が求められます。わずかなパーティクルや表面の凹凸が接合不良(ボイド)の原因となります。
- アライメント精度: 特にチップ直接接合の場合、ナノメートルオーダーの高精度な位置合わせが不可欠です。
- コスト: 高精度な装置やクリーンルーム環境が必要となるため、従来の接合技術に比べて設備投資や製造コストが高くなる傾向があります。
- 歩留まり: 高い精度が要求されるため、初期段階では歩留まりの確保が課題となることがあります。
直接接合技術は、ムーアの法則の限界が叫ばれる中で、半導体の性能向上を牽引する次世代のパッケージング技術として、今後ますます重要性が増していくと考えられています。
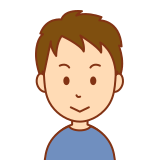
直接接合とは、半導体チップやウエハーを直接、原子レベルで結合させる技術のことで、さらなる微細化、高密度化や異種材料の接合を可能にするとして注目されています。
直接接合はどのような工程で行われるのか
半導体の直接接合は、非常に高度な技術と精密な工程を経て行われます。主要な直接接合の方式である「ウエハー直接接合(Wafer-to-Wafer Direct Bonding)」と、近年注目されている「ハイブリッドボンディング」の工程は以下のようなものです。
1. ウエハー直接接合 (Wafer-to-Wafer Direct Bonding) の一般的な工程
ウエハー直接接合は、2枚のウエハーを丸ごと接合する方式で、主にフュージョンボンディング(分子接合)と表面活性化接合の2つの主要なプロセスがあります。
1-1. フュージョンボンディング(分子接合)の工程
この方法は、特にSiO2(酸化シリコン)などの誘電体層を持つウエハーで広く用いられます。
- 洗浄・親水化処理:
- 接合する2枚のウエハー表面を、薬液や純水で徹底的に洗浄し、パーティクル(微粒子)や有機物などの不純物を除去します。
- この際、ウエハー表面に水酸基(OH基)を形成させるための「親水化処理」を行います。プラズマ処理(O2プラズマなど)がよく用いられます。この水酸基が、後の水素結合形成に重要となります。
- 前接合(プレボンディング):
- 清浄化・親水化された2枚のウエハーを、クリーンルーム内の超高精度な位置合わせ装置で、微細なズレなく密着させます。
- この段階では、ウエハー表面の水酸基間に水素結合やファンデルワールス力が働き、仮の接合(プレボンディング)が形成されます。この結合力はまだ弱く、物理的な力で剥がすことも可能です。
- この工程は常温(室温)で行われることが多いです。
- アニール(熱処理):
- プレボンディングされたウエハーを、高温(数百℃~1000℃以上)の熱処理炉に入れます。
- 熱を加えることで、表面の水酸基から水分子が脱離し、強固なSi-O-Si結合(共有結合)が形成されます。これにより、ウエハー間の接合が非常に強固になり、信頼性の高い結合となります。
- この熱処理によって、接合界面に残存するボイド(空隙)が拡散・消滅し、より密着した結合が実現されます。
1-2. 表面活性化接合 (Surface Activated Bonding: SAB) の工程
この方法は、常温・無加圧での接合を可能にし、熱に弱い材料や異種材料の接合に適しています。
- 表面活性化:
- 接合するウエハーの表面を、高真空チャンバー内でAr(アルゴン)イオンビームやAr原子ビームなどで照射します。
- これにより、表面の酸化膜や吸着ガス、汚染物質が物理的に除去され、ウエハー本来の原子が持つ「ダングリングボンド」(不飽和結合手)が露出します。この状態が「活性化された表面」です。
- この工程は、超高真空下で行われることが一般的です。
- 接合:
- 活性化された2つのウエハー表面を、同じく高真空中で、高精度なアライメント装置を用いて接触させます。
- 露出したダングリングボンド同士が瞬時に反応し、強固な共有結合が形成されます。この結合は、常温(室温)で行われ、熱や加圧をほとんど必要としません。
- (必要に応じて)熱処理:
- 結合強度を高めたり、残存する応力を緩和したりするために、後工程で比較的低温のアニール処理が施されることもあります。
2. ハイブリッドボンディングの工程
ハイブリッドボンディングは、金属配線(通常は銅:Cu)と絶縁体(通常はSiO2)を同一面上に形成し、これらを同時に直接接合する技術です。主に3D積層デバイスの高密度な電気接続に用いられます。
- 前処理(CMP、洗浄):
- 接合するウエハー(またはダイ)の表面に、金属配線(Cu)と絶縁体(SiO2)が形成されています。
- これらの表面を、CMP(化学的機械的平坦化)によって極めて高い平坦度と清浄度に研磨します。これは、ナノメートルレベルの平坦性が要求されるため、非常に重要な工程です。
- その後、パーティクルや有機物などを除去するための精密な洗浄を行います。
- 表面活性化(プラズマ処理):
- 洗浄後のウエハー表面に、プラズマ処理(N2プラズマなど)を施し、表面を活性化させます。これにより、CuとSiO2の両方の表面が接合しやすい状態になります。
- 位置合わせ・プレボンディング:
- 活性化された2つのウエハー(またはウエハーとダイ)を、超高精度なアライメント装置で位置合わせし、常温で密着させます。
- この段階では、主にSiO2界面間で水素結合が形成され、仮の接合が行われます。Cu配線間もわずかに接触しますが、本格的な接合はまだです。
- アニール(熱処理):
- プレボンディングされたウエハーを、比較的低温(200℃~400℃程度)で熱処理します。
- この熱処理によって、SiO2界面の水素結合が共有結合に変化し、同時にCu配線同士が熱拡散によって金属結合(固相拡散接合)を形成します。これにより、絶縁層と金属配線が同時に、かつ強固に接合されます。
- 熱処理温度が比較的低いため、デバイスへの熱ダメージを抑えることができます。
チップ直接接合 (Die-to-Wafer / Die-to-Die Direct Bonding) の工程
ウエハー直接接合の概念を、チップ単位に適用したものです。
- 個別チップの作製:
- まず、個々の半導体チップ(ダイ)をウエハーから切り出します。この際、Known Good Die(良品チップ)であることが重要です。
- チップの接合面も、ウエハーの場合と同様に、CMPやプラズマ処理などで平坦化・活性化されます。
- チップピックアップと位置合わせ:
- 専用のダイボンダーやピックアップ装置を用いて、切り出されたチップを1つずつ吸着し、接合対象のウエハーや他のチップの上に高精度に位置合わせします。
- このアライメント精度は、特に微細な接続ピッチを持つハイブリッドボンディングにおいて、非常に重要です。
- 接合:
- 位置合わせ後、チップとウエハー(またはチップとチップ)を接触させ、必要に応じて加圧や熱処理を行います。
- 接合のメカニズムは、フュージョンボンディングやハイブリッドボンディングと類似しており、表面の活性化状態とアニールによって強固な結合を形成します。
- 最終処理:
- 接合されたチップは、必要に応じてモールド封止やパッケージングなどの後工程に進みます。
まとめ
直接接合の工程は、いずれの方式においても、以下の点が共通して非常に重要となります。
- 極めて高い表面清浄度: わずかなパーティクルや有機物が接合不良(ボイド)の原因となるため、超クリーンな環境と精密な洗浄が不可欠です。
- ナノメートルレベルの表面平坦性: 接合面全体が均一に密着するためには、ナノメートルオーダーの平坦度が求められます。特にハイブリッドボンディングでは、CMPによる精密な研磨が必須です。
- 超高精度な位置合わせ: 特にチップ直接接合やハイブリッドボンディングでは、ミクロンからサブミクロンレベルの正確なアライメントが不可欠です。
- 表面活性化: 接合面が化学的に活性化されていることで、原子間の結合が促進されます。
これらの工程は、半導体製造装置メーカーによって開発された高度な装置によって自動的に行われ、高い歩留まりと信頼性を実現しています。
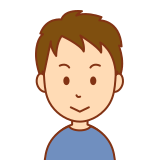
直接接合はチップ同士を作成し、位置合わせを行った後、加熱や加温で接合を行っています。表面を極めて高いレベルで洗浄できるか、超高精度での位置合わせができるかなどがポイントといえます。
直接接合時の酸化はどうやって防ぐのか
半導体の直接接合、特に銅(Cu)配線を含むハイブリッドボンディングのようなケースでは、銅の酸化防止は極めて重要な課題です。銅が酸化すると、電気抵抗が増加し、接合不良の原因となるため、デバイスの性能と信頼性に直接影響します。
直接接合において銅の酸化を防ぐ方法は、主に以下の2つのアプローチで実現されます。
1. 酸化が起きにくい環境でのプロセス管理
これは、直接接合における最も基本的かつ重要な酸化防止策です。
- 高真空環境下での処理:
- 直接接合の前工程(表面活性化など)から接合、そして場合によってはその後のアニール工程まで、可能な限り高真空チャンバー内で行われます。真空にすることで、空気中の酸素分子が銅表面に到達するのを極限まで防ぎます。
- キヤノンアネルバの原子拡散接合装置(BC7300)のように、基板搬送、成膜、接合、回収までを全自動で真空一貫処理できる装置は、この酸化防止の思想に基づいています。
- 不活性ガス雰囲気(N2、Arなど):
- 完全な真空が難しい場合や、特定のプロセスでガスを使用する必要がある場合は、窒素(N2)やアルゴン(Ar)などの不活性ガス雰囲気下で処理を行います。これらのガスは酸素と反応せず、銅の酸化を防ぎます。
- ウエハーやダイの保管、搬送時にも、不活性ガスが充填されたFOUP(Front Opening Unified Pod)などの容器が使用されます。
- コールドプロセス(低温処理):
- 温度が高いほど酸化反応は促進されるため、可能な限り低温で処理を行うことが望ましいです。特に、表面活性化接合のように常温で直接接合できる技術は、銅の酸化を大幅に抑制できます。ハイブリッドボンディングのアニール温度も、従来の接合方法に比べて比較的低温に抑えられています。
2. 銅表面の処理と保護
プロセス環境だけでなく、銅表面そのものにも酸化を防ぐための工夫が施されます。
- 精密な表面洗浄とプラズマ処理:
- 接合直前には、ウエハー(またはチップ)表面を極めて精密に洗浄し、微粒子(パーティクル)や有機汚染物質、そしてすでに形成されてしまった薄い酸化膜を徹底的に除去します。
- その後、**アルゴンプラズマ(Arプラズマ)や窒素プラズマ(N2プラズマ)**などの処理で表面を活性化させます。このプラズマ処理には、残存する微量の酸化膜を物理的に除去するスパッタリング効果や、表面の活性サイトを増やす効果があります。
- 特に銅の場合、プラズマ処理によって表面の酸化銅(Cu2OやCuO)を金属銅(Cu)に還元する効果も期待されます。
- バリア層/キャップ層の形成:
- 銅はシリコンや絶縁膜中へ拡散しやすい性質があるため、配線形成時にバリアメタル層(例:Ta、TaN、TiNなど)を形成して拡散を防ぎます。このバリア層は、同時に銅が外部の酸素と接触するのを防ぐ物理的な障壁としても機能します。
- 特にハイブリッドボンディングでは、銅配線が埋め込まれたSiO2絶縁膜の上に、さらに**SiN(窒化シリコン)やSiC(炭化シリコン)**などの薄いキャップ層を形成することがあります。これにより、銅表面が直接大気に触れるのを防ぎ、後のプロセスでの酸化を抑制します。
- インサイチュー(in-situ)処理:
- 一つの装置内で、銅配線の形成から表面処理、そして直接接合までを一貫して行う「インサイチュー」プロセスを採用することで、銅が空気に触れる機会を最小限に抑えます。これにより、酸化のリスクを劇的に低減できます。
ハイブリッドボンディングにおける具体的な対策
ハイブリッドボンディングは、銅(Cu)と絶縁体(SiO2)を同時に接合する技術であり、銅の酸化対策が特に重要になります。
- CMPによる平坦化と表面調整: CMP(化学的機械的平坦化)によって銅配線とSiO2絶縁膜の表面を原子レベルで平坦化し、かつクリーンな状態にします。このスラリーには、銅の腐食・酸化を防ぐための防食剤が添加されていることもあります。
- プラズマ処理: 接合直前に、N2プラズマなどを用いてCuとSiO2の両表面を活性化し、酸化物や吸着ガスを除去します。
- 比較的低温のアニール: 従来の半田接合などに比べ、ハイブリッドボンディングのアニール温度は比較的低く抑えられます(200℃~400℃程度)。これにより、熱による銅の酸化促進を抑制しつつ、Cu同士の固相拡散接合を促します。
これらの対策を組み合わせることで、半導体製造の直接接合において、銅の酸化を効果的に防ぎ、高性能で信頼性の高いデバイスを実現しています。
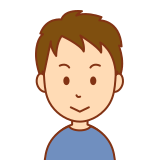
銅が酸化すると、電気抵抗が増加し、接合不良の原因となるため、デバイスの性能と信頼性に直接影響すため、酸化の防止は極めて重要です。酸化が起きにくい環境での処理や銅表面の処理と保護などが重要となります。
コメント