この記事で分かること
射出成形機とは:プラスチック原料を加熱・溶融し、金型へ高圧で射出し冷却固化させることで、多様なプラスチック製品を効率的に製造する機械です。
電動式のメリット:電気モーターで各動作を駆動します。これにより、油圧式に比べ省エネ、高精度な制御、騒音低減、クリーンな環境維持、サイクルタイム短縮が可能となり、精密成形や環境負荷低減に貢献します。
日本製鋼所の電動式射出成形機
日本製鋼所が2025年7月にも、電動式の4000トン射出成形機を市場に投入するしています。
https://www.nikkan.co.jp/articles/view/00752546
日本製鋼所は、プラスチック射出成形機の分野で高い技術力を持ち、特に大型の成形機に強みがあります。同社の射出成形機は、自動車部品、ペットボトル、レンズ、メモリーチップなど、幅広いプラスチック製品の製造に貢献しています
射出成形機とは何か
射出成形機(しゃしゅつせいけいき)とは、プラスチック製品を製造するための機械です。その名の通り、材料を「射出」し、「成形」する工程を行います。
簡単に言うと、プラスチックの原料(ペレット状の樹脂など)を機械の中で溶かし、それを金型と呼ばれる精密な型の中に高圧で流し込み(射出)、冷却して固めることで、目的の形に製品を作り出す機械です。
射出成形機の主な仕組みと工程
射出成形機は大きく分けて、以下の2つのユニットで構成されています。
- 射出ユニット (Injection Unit)
- ホッパー: プラスチックの原料(ペレット)を投入する部分です。
- シリンダー(加熱筒): ホッパーから送られてきたペレットをヒーターで加熱し、スクリューの回転による摩擦熱も加えて溶融します。
- スクリュー: シリンダー内で回転・前進することで、溶けた樹脂を混練し、先端に計量・蓄積します。
- ノズル: スクリューの先端に溜まった溶融樹脂を、金型に射出する出口です。
- 型締ユニット (Clamping Unit)
- 金型: 製品の形状が彫り込まれた金属製の型です。可動側と固定側の2つのプレートで構成され、これらが閉じ合わさって製品のキャビティ(空洞)を形成します。
- 型締装置: 金型を強力に締め付け、溶融樹脂を射出する際の高い圧力によって金型が開いてしまわないように保持します。成形後には金型を開いて製品を取り出します。
射出成形の基本的な工程
- 型閉じ・型締め: 可動側の金型が固定側の金型に移動し、強力な力で締め付けられます。
- ノズルタッチ: 射出ユニットのノズルが金型に密着します。
- 射出: シリンダー内で溶融・計量された樹脂が、スクリューの前進によって高圧で金型内に射出されます。
- 保圧: 金型内の樹脂が冷えて収縮するのを補うため、一定の圧力をかけ続けます。
- 冷却: 金型内で樹脂が冷却され、固化します。この間に、次の射出のための樹脂の溶融・計量(可塑化)が並行して行われることが多いです。
- 型開き: 金型が開き、成形された製品が取り出されます。
- 製品取り出し: ロボットや手作業で成形品を取り出します。
射出成形機の駆動方式
射出成形機には、主に以下の駆動方式があります。
- 油圧式: 油圧ポンプの力で駆動する方式。高い型締力を安定して出せるのが特徴です。
- 電動式: サーボモーターの力で駆動する方式。精密な制御が可能で、省エネルギー性や静音性に優れます。最近の主流です。
- ハイブリッド式: 油圧と電動を組み合わせた方式。両者の良い点を兼ね備えています。
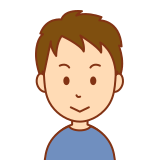
射出成形機は、プラスチック原料を加熱・溶融し、金型へ高圧で射出し冷却固化させることで、多様なプラスチック製品を効率的に製造する機械です。自動車部品から日用品まで、幅広い製品の量産に不可欠な設備です。
どんなプラスチック製品に、使用されるのか
射出成形機は、非常に幅広い種類のプラスチック製品の製造に利用されています。
以下のように、私たちの身の回りのほとんどのプラスチック製品は、射出成形で作られていると言っても過言ではありません。
1. 自動車部品
- 外装部品: バンパー、グリル、ヘッドライトのハウジング、サイドミラー、ドアノブ、フェンダーインナーなど。軽量化と耐腐食性、デザイン性の両立に貢献しています。
- 内装部品: ダッシュボード、インストルメントパネル、ドアトリム、シートの骨格、カップホルダー、各種スイッチ類、エアコン吹き出し口など。
- エンジンルーム部品: エアインテークマニホールドなど、耐熱性や強度を求められる部品も製造されます。
2. 家電製品・エレクトロニクス部品
- 筐体: テレビやエアコンの外装、洗濯機の部品、冷蔵庫の棚、掃除機本体など。
- 内部部品: パソコンのフレームやキーボード、プリンターの部品、リモコン、スイッチ、コネクタ、レンズ、光ディスク(CD/DVD/Blu-ray)など。
- 携帯電話・スマートフォン部品: ケース、内部の精密部品、レンズなど。
3. 日用品・雑貨
- 容器: ペットボトル(プリフォーム製造)、ボトルキャップ、食品容器(タッパーなど)、洗剤ボトルなど。
- 食器: プラスチック製の皿、コップ、カトラリーなど。
- おもちゃ: プラモデル、ブロック玩具、人形のパーツなど、細かな部品から大型のものまで。
- 文房具: ペンケース、定規、クリアファイル、ファイルボックスなど。
- その他: ゴミ箱、収納ケース、ハンガー、風呂椅子、ガーデニング用品、屋外用家具など。
4. 医療機器
- 注射器の筒、点滴容器、ピペット、医療用トレイ、検査用チップなど、衛生性や高精度が求められる製品。
5. 建設・住宅関連
- 配管部品、スイッチプレート、ドアの取っ手、窓枠の一部など。
6. スポーツ・レジャー用品
- ヘルメットの一部、スキーブーツのシェル、釣り具、アウトドア用品など。
7. 精密部品
- カメラのレンズ、光ファイバー接続部品、時計の歯車など、非常に高い寸法精度が要求される部品。
このように、射出成形機は、小さなネジのような部品から、車のバンパーのような大きな部品まで、様々なサイズ、形状、機能を持つプラスチック製品を、高品質かつ効率的に量産するために不可欠な機械です。使用されるプラスチック材料も、ポリエチレン(PE)、ポリプロピレン(PP)、ABS樹脂、ポリカーボネート(PC)、アクリル(PMMA)など、多岐にわたります。
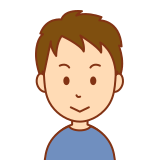
射出成形機は、自動車部品(バンパー、内装)、家電製品(筐体、内部部品)、日用品(容器、おもちゃ)、医療機器(注射器)、精密部品(レンズ)など、多様なプラスチック製品の効率的な大量生産に広く使用されています。
電動式とはどのような装置なのか
射出成形機の場合、「電動式」は、機械の各動作(型開閉、射出、計量、突き出しなど)を、油圧ポンプの力ではなく、サーボモーター(電気モーター)の力で駆動することを指します。
従来の射出成形機は「油圧式」が主流でしたが、近年では「電動式」が普及し、特に小型~中型の精密成形機において主流になりつつあります。
電動式射出成形機の主な特徴とメリット
- 省エネルギー性: 必要な時に必要なだけモーターを動かすため、油圧式に比べて消費電力を大幅に削減できます(40~50%削減とも言われます)。これは電気料金の削減に直結します。
- 高精度・高安定性: サーボモーターによる精密な位置・速度制御が可能で、成形条件の安定化が図れます。これにより、成形品の寸法や品質のバラつきが少なくなり、不良率の低減に貢献します。
- 生産性向上: 複数のモーターが独立して動作するため、型開閉、射出、計量といった工程を並行して行いやすくなり、成形サイクルタイムを短縮できます。
- クリーンな環境: 油圧を使用しないため、作動油の漏れや油煙の発生がなく、工場内の環境が清潔に保たれます。食品容器や医療関係の製品を製造する際に特に有利です。
- 低騒音: 油圧ポンプの駆動音がなく、比較的静かに運転できます。
ただし、一般的に油圧式に比べて初期導入コストが高い傾向にあります。それでも、省エネ性や品質安定性などのメリットを考慮すると、長期的な運用コストや製品品質の面で優位性があるとされ、導入が進んでいます。
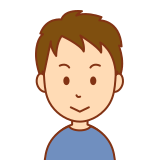
電動式射出成形機は、電気モーターで各動作を駆動します。これにより、油圧式に比べ省エネ、高精度な制御、騒音低減、クリーンな環境維持、サイクルタイム短縮が可能となり、精密成形や環境負荷低減に貢献します。
射出成形機にはどんな機能が必要なのか
近年の射出成形機には、技術進化と社会の変化に対応するため、多岐にわたる要素が求められています。主なものとしては以下の点が挙げられます。
省エネルギー性・環境対応
- 電動化の推進: 以前にも述べた通り、油圧式から電動式への移行が加速しており、消費電力の削減とCO2排出量の削減が強く求められています。
- 材料のリサイクル対応: プラスチック廃棄物の問題意識の高まりから、再生材やバイオマスプラスチックなど、環境負荷の低い材料の成形に対応できる能力や、成形工程での廃棄物削減も重要視されています。
- 製造工程での熱効率向上: ヒーターの放熱抑制や排熱回収システムなど、工場全体のエネルギー効率向上が求められます。
高精度・高品質化
- 精密成形への対応: 自動車部品のEV化に伴う複雑な形状や薄肉化、医療機器や光学部品など、より高い寸法精度や表面品質が要求される製品の製造に対応できる能力が不可欠です。
- 成形不良の低減: ショートショット、バリ、ヒケ、ソリなどの成形不良を最小限に抑え、歩留まりを向上させるための高度な制御技術が求められています。
生産性向上・自動化・スマート化
- 高速化・サイクルタイム短縮: 大量生産におけるコスト競争力維持のため、より短いサイクルタイムで成形できる能力が求められます。
- 多品種少量生産への対応: 消費者ニーズの多様化や製品ライフサイクルの短期化に対応するため、金型交換の効率化や、少量でも高効率に生産できる柔軟性が重要です。
- IoT・AIの活用: 成形条件のリアルタイム監視、データ分析による最適化、予知保全、自動調整など、生産ライン全体のスマート化が求められています。これにより、人手不足への対応や、熟練技術者のノウハウの継承にも繋がります。
- 自動化の促進: ロボットによる製品の取り出し、ゲートカット、検査、梱包など、前後工程を含めた自動化が求められています。
多様な材料への対応
- 一般的な汎用プラスチックに加え、エンジニアリングプラスチック、スーパーエンジニアリングプラスチック、複合材料(繊維強化プラスチックなど)といった、特殊な物性を持つ材料の成形技術も進化が求められています。
これらの要求は、射出成形機メーカーに対して、より高度な技術開発と、製造業全体の持続可能性に貢献するソリューションの提供を促しています。
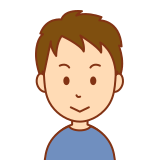
近年の射出成形機には、省エネルギー化・環境対応(電動化、リサイクル材対応)、高精度・高品質化(精密部品、不良低減)、生産性向上・自動化・スマート化(高速化、IoT・AI活用)、そして多様な材料への対応力**が強く求められています。
コメント