この記事で分かること
- セラミックとは:無機材料を高温で焼成して得られる固体材料の総称で、硬さ、高い耐熱性、絶縁特性の高さ、化学的な安定性などから多くの分野で活用されています。
- なぜ、硬いのか:原子間の結合がとても強い、結晶構造がずれにくい、自由電子がないといった特徴から、硬い材料となります。
- 金属との複合材料の利点:互いの欠点(セラミックのもろさや加工にしにくさ、金属の熱膨張・耐熱性の低さ)を補うためや応力の分散などのために利用されています。
三菱マテリアルによる金属―セラミックス複合材料
三菱マテリアルは高熱伝導性・低熱膨張性・加工性を持つ金属―セラミックス複合材料を開発したことを発表しています。
同社は今後も金属とセラミックスの接合技術や新素材の開発を進め、次世代のパワーエレクトロニクス分野での革新を目指すとしています。
セラミックとは何か
セラミック(ceramic)は、無機材料を高温で焼成して得られる固体材料の総称で、古くは陶器や磁器に始まり、現在では電子部品から人工関節まで幅広く使われています。
【セラミックの特徴】
- 硬くて丈夫
- 金属よりも硬いこともあり、耐摩耗性に優れています。
- 高い耐熱性
- 数百度から数千度でも形状を保つことができる。
- 電気絶縁性が高い
- 電気を通さないため、電子基板などに使用されます。
- 化学的に安定
- 酸やアルカリにも強く、腐食しにくい。
- 脆い(割れやすい)
- 一方で、衝撃に弱い「もろさ」が欠点です。
【セラミックの種類】
種類 | 用途の例 | 特徴 |
---|---|---|
酸化物系(例:アルミナ、ジルコニア) | 絶縁体、バイオ材料 | 高耐熱・耐腐食性 |
窒化物系(例:窒化ケイ素、窒化アルミニウム) | パワー半導体基板 | 高熱伝導、絶縁性 |
炭化物系(例:炭化ケイ素) | 切削工具、ヒートシンク | 高硬度・耐摩耗性 |
【最近のトレンド】
最近では、
- 金属とセラミックの複合材料(CMC:Ceramic Matrix Composites)
- 熱伝導性セラミック(AlN、SiCなど)
- バイオセラミック(人工骨や歯) などが注目されており、材料設計や加工技術の進展により、新しい用途がどんどん広がっています。
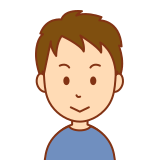
セラミックは、無機材料を高温で焼成して得られる固体材料の総称で、硬さ、高い耐熱性、絶縁特性の高さ、化学的な安定性などから多くの分野で活用されています。
セラミックはどのように作られるのか
セラミックの製造方法は以下のように「粉体を成形して焼く」というのが基本です。
【1. 原料粉末の準備】
- 原料は酸化物(Al₂O₃、ZrO₂など)や非酸化物(Si₃N₄、SiCなど)。
- 粒径を整えたり、純度を高めたりして、性能を安定させる。
【2. 混合・粉砕】
- 均一な焼結性や分布性を持たせるために、バインダー(結合剤)や分散剤と一緒に粉砕。
- ボールミルやジェットミルなどで細かくします。
【3. 成形】
目的に応じていくつかの方法があります:
成形法 | 特徴 |
---|---|
ドライプレス | 粉末を型に入れて圧縮。シンプルで大量生産向き。 |
スリップキャスティング | 水に分散させたスラリーを型に流す。複雑形状対応。 |
射出成形(CIM) | プラスチックのように成形。微細・精密部品向け。 |
テープキャスティング | フィルム状にして基板などに。電子材料に多い。 |
【4. 脱脂(バインダー除去)】
- 成形体に含まれる有機物(バインダー)を加熱で分解・除去。
- ゆっくり行わないと割れやガス欠陥が出るので慎重に。
【5. 焼結(焼成)】
- 高温(通常1000〜2000℃)で焼いて、粉末同士を融合・緻密化。
- 雰囲気(空気中、真空、窒素中など)によって性質が変わる。
【6. 機械加工・仕上げ】
- 焼結後は非常に硬いため、ダイヤモンド工具などで仕上げ加工。
- 研削やレーザー加工で高精度な仕上げが可能。
【7. 検査・評価】
- 機械的性質(強度・硬度)、熱特性、電気特性などを測定。
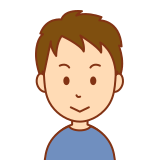
酸化物(Al₂O₃、ZrO₂など)や非酸化物(Si₃N₄、SiCなど)の粉体を成形して焼くことが基本的な製法となります。
なぜ、金属よりも硬いのか
セラミックが金属よりも硬くできる理由は、原子の結びつき(結合様式)と構造にあります。
【1. 強い原子間結合】
セラミックは主にイオン結合と共有結合でできています:
結合の種類 | 例 | 特徴 |
---|---|---|
イオン結合 | Al₂O₃(酸化アルミニウム) | 陽イオンと陰イオンが強く引き合っている。 |
共有結合 | SiC(炭化ケイ素)、Si₃N₄(窒化ケイ素) | 原子同士が電子を共有して非常に強い結合を形成。 |
→ これらの結合は非常に強力なので、原子同士がずれにくく、変形しにくい=硬いという性質が生まれます。
【2. 結晶構造がずれにくい】
金属はすべり(滑り)やすい構造を持っています。だから力がかかると変形(延性)できる。
一方セラミックは、結晶構造が「複雑」かつ「方向性が強く」、欠陥の移動(転位運動)が難しいため、「力を加えると割れる」けど「変形はしない」=硬くてもろい(脆性)という特徴があります。
【3. 電子が自由に動けない】
金属は自由電子を持ち、「電子の海」の中で原子が動けるので柔らかくなれる。
セラミックは電子が結合にがっちり関わっていて自由に動けないため、構造が固定されやすく、硬さにつながる。
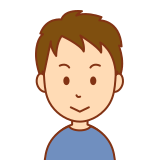
セラミックは原子間の結合がとても強い、結晶構造がずれにくい、自由電子がないといった特徴から、硬い材料となります。
金属との複合材料を作る理由は何か
セラミックと金属の複合材料(いわゆる金属–セラミックス複合材、Metal-Ceramic Composites)を作る主な理由は、それぞれの材料の「長所を生かし、短所を補う」ためです。
1. セラミックの短所(もろさ)を金属が補う
- セラミックは硬くて高耐熱だけど、衝撃や曲げに弱く割れやすい(脆い)。
- 金属と組み合わせることで、複合材は「靭性(粘り強さ)」や「耐衝撃性」が向上します。
2. 金属の短所(熱膨張・耐熱性の低さ)をセラミックが補う
- 金属は温度が上がると膨張しやすく、また酸化しやすい。
- セラミックは熱に強く、熱膨張が小さいため、複合化することで寸法安定性や高温性能を向上できます。
3. 放熱性と絶縁性を両立したい場合
- 例えば、パワー半導体では「熱は通すけど電気は通さない」材料が理想。
- セラミック基板(AlNなど)と金属(Cuなど)を接合することで、電気絶縁性と熱伝導性のバランスを取れます。
4. 加工性・機械加工のしやすさを向上
- セラミック単体は加工が困難だが、金属と組み合わせれば機械加工や接合が容易になります(例:ろう付けやメタライズ処理)。
5. 応力分散・熱応力の吸収
- 異なる材料が熱膨張したときの「応力集中」を緩和し、耐久性や信頼性を高められます。
代表的な応用例
- パワーモジュール基板(AlNセラミック基板+銅メタル)
- 航空機エンジンのCMC(セラミックマトリックス複合材)
- 歯科材料(セラミッククラウン+金属フレーム)
- 人工関節(セラミックボール+金属ソケット)
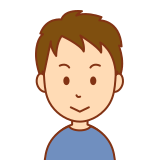
セラミックと金属の複合材料は互いの欠点(セラミックのもろさや加工にしにくさ、金属の熱膨張・耐熱性の低さ)を補うためや応力の分散などのために利用されています。
コメント