この記事で分かること
次世代ものづくり実装研究センターとは:様々な次世代のものづくりシステムを構築することで、生産性向上と高度人材の育成を目指す取り組みをおこなう研究センターです。
製造サイバーフィジカルシステムとは:IoTやデジタルツイン、AI技術を利用し、現実世界(フィジカル空間)と、コンピュータ内の仮想空間(サイバー空間)を高度に連携させ、モノづくりを最適化、効率化させる技術のことです。
次世代ものづくり実装研究センター
産業技術総合研究所(産総研)は、2025年4月に「実装研究センター」を新設し、社会課題の解決に向けた技術の社会実装を加速する取り組みを開始しました。
https://www.aist.go.jp/aist_j/news/au20250401_2.html
産総研の第6期中長期目標では、「エネルギー・環境・資源制約への対応」「人口減少・高齢化社会への対応」「レジリエントな社会の実現」の3つの社会課題の解決が掲げられています。
これらの課題に取り組むため、7つの実装研究センターが設立され、所内の研究成果を結集し、産総研の総合力を最大限に生かした研究開発を推進していくとしています。
今回は7つの実装研究センターの一つである「次世代ものづくり実装研究センター」の概略とテーマの一つである製造サイバーフィジカルシステムについての解説となります。
7つの実装研究センターとは何か
産総研は、研究成果の社会実装を通じて、社会課題の解決と産業競争力の強化を目指しています。
7つの実装研究センターとして以下のような主な取り組みがあり、各研究センターは、産学官連携を強化し、技術の実用化と普及を推進していく予定です。
- CCUS実装研究センター
CO₂削減技術の社会実装を目指し、カーボンニュートラル実現に貢献します。 - サーキュラーテクノロジー実装研究センター
高度リサイクル技術の社会実装を通じて、サーキュラーエコノミーの実現を目指します。 - ネイチャーポジティブ技術実装研究センター
自然資本の計測・評価・回復技術を社会実装し、ネイチャーポジティブ社会の実現を目指します。 - 次世代ものづくり実装研究センター
次世代のものづくりシステムを構築し、生産性向上と高度人材の育成を目指します。 - ウェルビーイング実装研究センター
心身負荷のモニタリングおよび軽減技術を社会実装し、生産・就労現場の改善と生産性向上を目指します。 - セルフケア実装研究センター
セルフケアの基盤技術を社会実装し、健康寿命の延伸を目指します。 - レジリエントインフラ実装研究センター
先進的なインフラ維持管理技術を社会実装し、インフラの強靱化を目指します。
これらのセンターは、産総研の研究戦略や社会実装戦略が直接反映される体制のもと、社会課題の解決を目指して研究開発を進めています。
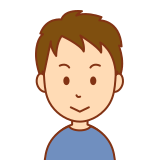
産総研は、研究成果の社会実装を通じて、社会課題の解決と産業競争力の強化を目指しています。7つの実装研究センターはそれぞれの分野で、産学官連携を強化し、技術の実用化と普及を推進していく予定です。
次世代ものづくり実装研究センターとは何か
産総研(国立研究開発法人産業技術総合研究所)の次世代ものづくり実装研究センターは、2025年4月に新設された7つの実装研究センターの一つです。
このセンターの主な目的は、以下のような取り組みを通じて、次世代のものづくりシステムを構築し、生産性向上と高度人材の育成を目指すことです。
主な活動内容・研究テーマ:
製造サイバーフィジカルシステム(CPS)の研究開発
- AI技術、DX技術、ロボット技術などを活用し、物理空間と情報空間を高度に融合させた製造システムを構築します。
- ロボットや工作機械、AI、デジタルツインなどを連携させることで、より効率的で高度なものづくりを実現します。
製造技術の知識構造化型データベースの構築
- 製造現場で培われてきたノウハウや加工現象のモデル化、データ化を進め、デジタルものづくりを推進するための基盤を構築します。
データ駆動型加工データ統合・活用
- 加工された材料の特性とミクロ組織との関係性の解明や、加工現象の観察によるモデル化などを通じて、データに基づいた効率的な加工技術を開発します。
ロボットソフトウェアプラットフォームの研究開発
- ロボットの命令系統やプログラム言語をオープンミドルウェアを使って統一・標準化を進め、異種のロボットやシステム間の連携を容易にします。
高機能部材開発
- 形状・材料特性と異分野プロセスを融合させた高機能部材の開発に取り組んでいます。光機能や濡れ性、摩擦特性などの機能制御を目指します。
高度ものづくり人材の育成
- 人口減少や高齢化社会に対応するため、生産性向上と同時に高度なものづくり人材の育成が急務とされており、これにも貢献することを目指しています。
拠点
次世代ものづくり実装研究センターは、以下の3つの研究拠点に設置されています。
- 臨海副都心センター(東京)
- つくばセンター(茨城)
- 北陸デジタルものづくりセンター(石川)
背景と意義
産総研は、研究成果の社会実装を通じて、社会課題の解決と産業競争力の強化を目指しており、この次世代ものづくり実装研究センターは、その一環として、日本のものづくり産業が直面する課題(人口減少、高齢化、国際競争力の強化など)に対応し、新たな価値を創出するための重要な役割を担っています。
産学官連携を強化し、技術の実用化と普及を推進していく方針です。
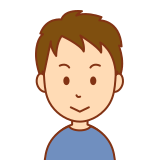
次世代ものづくり実装研究センターは様々な次世代のものづくりシステムを構築することで、生産性向上と高度人材の育成を目指す取り組みです。
製造サイバーフィジカルシステムとは何か
「製造サイバーフィジカルシステム(CPS)」とは、現実世界(フィジカル空間)の製造プロセスと、コンピュータ内の仮想空間(サイバー空間)を高度に連携させ、相互に情報をやり取りしながら、ものづくり全体を最適化・自動化するシステムのことです。
製造サイバーフィジカルシステムは以下の要素が組み合わさって実現されます。
フィジカル空間からのデータ収集
- 工場内の機械設備、センサー、ロボット、製品、作業員など、あらゆるものからリアルタイムでデータを収集します。
- IoT(Internet of Things)デバイスがこの役割を担い、温度、湿度、稼働状況、不良品の発生、部品の摩耗状態など、多種多様な情報を取得します。
サイバー空間でのデータ処理・分析・シミュレーション
- 収集された膨大なデータを、AI(人工知能)やビッグデータ解析技術を用いて分析します。
- デジタルツインの概念が重要で、現実の工場や生産ライン、製品を仮想空間に再現し、その中で様々なシミュレーションを行います。
- 例えば、生産計画の最適化、設備の故障予兆診断、品質不良の原因特定、新たな製品設計の検証などを仮想空間上で行います。
フィジカル空間へのフィードバックと制御
- サイバー空間での分析やシミュレーションの結果を基に、現実の製造プロセスに対して最適な指示や制御を行います。
- ロボットや自動機械の動作を調整したり、生産ラインの稼働条件を変更したり、作業員に具体的な指示を与えたりすることで、現実の状況を改善・最適化します。
製造CPSの主な目的とメリット
- 生産ラインの最適化: リアルタイムのデータに基づいて生産計画を調整し、無駄を排除して生産効率を最大化します。多品種少量生産や急な仕様変更にも柔軟に対応できるようになります。
- 品質向上: 異常検知や予兆保全により、不良品の発生を未然に防ぎ、製品品質の安定化・向上を図ります。
- コスト削減: エネルギー消費の最適化、設備の稼働率向上、不良品削減などにより、製造コストを低減します。
- 高度な自動化と省人化: 危険な作業や単純作業をロボットやAIに任せることで、人手不足を解消し、作業者の負担を軽減します。
- 技術継承と属人化の防止: 熟練工の「匠の技」やノウハウをデータとして蓄積・分析し、AIやロボットに学習させることで、技術の形式知化と継承を促進します。
- 新製品開発の加速: 仮想空間でのシミュレーションにより、試作回数を減らし、開発期間とコストを大幅に削減できます。
IoT、デジタルツイン、AIとの関係性
製造CPSは、IoT、デジタルツイン、AIといった技術が密接に連携することで実現されます。
- IoT: フィジカル空間からデータを収集するための「目」や「耳」の役割を果たします。
- デジタルツイン: 現実世界をサイバー空間に再現し、様々なシミュレーションを行うための「仮想空間」の役割を果たします。
- AI: 収集されたデータを分析し、最適な解を導き出すための「頭脳」の役割を果たします。
製造CPSは、これらの技術を統合することで、これまでの製造業が抱えていた様々な課題を解決し、よりスマートで効率的なものづくりを実現する、いわゆる「スマートファクトリー」や「インダストリー4.0」の中核をなす概念と言えます。
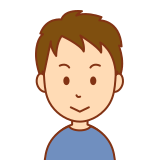
製造サイバーフィジカルシステムは、IoTやデジタルツイン、AI技術を利用し、現実世界(フィジカル空間)と、コンピュータ内の仮想空間(サイバー空間)を高度に連携させ、モノづくりを最適化、効率化させる技術のことです。
いわゆる「スマートファクトリー」や「インダストリー4.0」の中核をなす概念と言えます。
どのような具体例があるのか
製造サイバーフィジカルシステム(CPS)は以下のような製造業で具体的な事例があります。
1. 生産ラインの最適化とシミュレーション
- 大手自動車メーカー(例:BMW、トヨタ自動車、ダイキン工業)
- 状況: 新しい生産ラインを導入する際や、既存ラインのレイアウト変更、生産品目の変更などを行う際に、物理的に設備を動かす前に、サイバー空間上でシミュレーションを行います。
- CPSの機能:
- 生産ライン上のロボット、コンベア、工作機械などすべての設備をデジタルツインとして仮想空間に再現します。
- 各設備の稼働データ、製品の移動時間、ボトルネックの発生状況などをリアルタイムでサイバー空間に反映し、現状を正確に把握します。
- 新たなレイアウトや生産計画を仮想空間で試行し、生産性、スループット、リードタイムなどをシミュレーションによって予測します。
- AIが最適な生産計画や設備の配置を提案し、その結果を物理空間にフィードバックして実行します。
- 効果: 設備投資の意思決定時間を大幅に短縮し、最適な生産ラインを構築できます。試作や物理的な変更に伴うコストと時間を削減し、生産開始までの期間を短縮します。
2. 予知保全と設備稼働率向上
- 工場設備メーカーやプラント運営企業(例:旭化成、GE – 航空機エンジン)
- 状況: 製造設備やプラントは複雑であり、故障が発生すると甚大な損害や生産停止を招く可能性があります。
- CPSの機能:
- 設備に多数のセンサー(振動、温度、圧力、電流など)を取り付け、稼働データをリアルタイムで収集します。
- 収集されたデータはサイバー空間でAIによって分析され、過去の故障データや正常時のデータと比較されます。
- 異常なパターンや故障の兆候をAIが検知し、故障発生前にアラートを発します。
- デジタルツイン上で設備の劣化状況や寿命を予測し、最適なメンテナンス時期を計画します。
- 効果: 突発的な故障を未然に防ぎ、計画的なメンテナンスが可能になります。これにより、設備の稼働率が向上し、生産停止による損失を最小限に抑えられます。また、交換部品の在庫管理も最適化されます。
3. 品質管理と不良品削減
- 自動車部品メーカーや精密機器メーカー
- 状況: 製品の品質は企業の競争力に直結し、不良品が発生すると回収や廃棄にかかるコストが大きくなります。
- CPSの機能:
- 製造工程の各段階で、製品の寸法、形状、材料特性、表面状態などをリアルタイムで計測します。
- これらのデータをサイバー空間のデジタルツインに反映させ、製品の品質履歴をデジタルで管理します。
- AIが膨大な製造データと品質データを関連付け、不良品の発生要因を分析します。
- 不良品の兆候が見られた場合、自動で生産ラインの調整を行ったり、作業員に警告を発したりします。
- 効果: 品質管理の精度が向上し、不良品率を大幅に削減できます。問題発生時の原因究明も迅速に行えるため、改善サイクルが加速します。
4. 遠隔監視・遠隔操作と技術伝承
- 化学プラント、遠隔地にある工場(例:旭化成の水素製造プラント)
- 状況: 熟練の技術者が高齢化し、技術継承が課題となる中、遠隔地にある設備の監視や操作、異常対応が求められます。
- CPSの機能:
- 物理空間のプラントや設備をデジタルツインとして再現し、各種センサーから送られるデータをリアルタイムで可視化します。
- 熟練技術者は、離れた場所からでも仮想空間を通じて設備の状況を詳細に確認し、異常発生時には原因を特定し、遠隔で操作指示やアドバイスを送ることができます。
- 作業手順やノウハウをVR/AR技術と連携させ、未熟練の作業員に対して具体的な指示をデジタルで提示できます。
- 効果: 熟練技術者のノウハウを効率的に伝承し、人材不足を補うことができます。遠隔地からの迅速な対応が可能になり、出張コストや時間を削減できます。
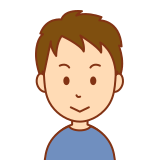
フィジカル空間とサイバー空間の連携によって、製造業の生産性、品質、コスト、人材育成といった多角的な課題解決に貢献している事例が多くあります。
デジタルツインとは何か
「デジタルツイン(Digital Twin)」とは、現実世界に存在する物理的なモノ(製品、設備、工場、都市など)やシステム、あるいは人間の活動や行動を、サイバー空間(仮想空間)上に高精度に再現した「双子」のようなモデルのことです。
この「デジタルの双子」は、単なる3Dモデルやシミュレーションとは異なり、現実世界とリアルタイムにデータを連携させ、常にその状態を反映し、相互に影響し合うという点が最大の特徴です。
デジタルツインの仕組み
- データ収集(物理空間からサイバー空間へ)
- 現実世界のモノやシステムには、温度、湿度、振動、圧力、電流、稼働状況、位置情報などを計測する多種多様なセンサー(IoTデバイス)が取り付けられます。
- これらのデータは、ネットワーク(5Gなどの高速通信技術も活用される)を通じてリアルタイムでサイバー空間に送られます。
- 仮想モデルの構築と更新(サイバー空間)
- サイバー空間では、現実のモノやシステムを忠実に再現したデジタルモデル(デジタルツイン)が構築されます。これは、3D CADデータ、物理モデル、過去のデータ、AIモデルなど、様々な情報に基づいて作成されます。
- 収集されたリアルタイムデータは、このデジタルツインに反映され、常に最新の現実世界の状況を仮想空間に再現します。
- 分析とシミュレーション(サイバー空間)
- デジタルツインに蓄積されたデータは、AI(人工知能)や機械学習、シミュレーション技術を用いて分析されます。
- これにより、以下のようなことが可能になります。
- 現状の可視化と把握: リアルタイムで何が起きているか、設備の稼働状況やパフォーマンスはどうなっているかなどを詳細に把握できます。
- 将来予測: 設備の故障予兆、製品の劣化、生産ラインのボトルネックなどを予測します。
- 問題解決のシミュレーション: 特定の状況でどのような問題が発生するか、その解決策としてどのような対応が最適かを仮想空間で試行錯誤できます。
- 最適化の検討: 生産計画、エネルギー消費、メンテナンススケジュールなど、様々な要素の最適化案をシミュレーションによって導き出します。
- フィードバックと実行(サイバー空間から物理空間へ)
- サイバー空間での分析やシミュレーションの結果に基づいて、現実世界のモノやシステムに対して最適な指示や制御が行われます。
- 例えば、ロボットの動作調整、生産ラインの速度変更、設備のメンテナンス指示、新たな設計の適用などが行われます。
デジタルツインのメリット
- 試作期間の短縮・コスト削減: 物理的な試作を減らし、仮想空間で何度も検証できるため、開発期間とコストを大幅に削減できます。
- 品質の向上・リスク低減: リアルタイム監視と予兆保全により、不良品の発生や故障を未然に防ぎ、品質安定とリスク管理を強化します。
- 生産性向上: 生産ラインの最適化、ボトルネックの解消、ダウンタイムの削減などにより、全体の生産効率を高めます。
- 遠隔での作業支援・技能伝承: 遠隔地からでも設備の状況を詳細に把握し、操作やメンテナンスの指示を出すことが可能になります。熟練者のノウハウをデジタル化し、若手への技術伝承にも役立ちます。
- 意思決定の迅速化: リアルタイムで正確な情報に基づいたシミュレーションにより、より迅速かつ的確な意思決定が可能になります。
- 顧客満足度の向上: 製品の使用状況をモニタリングし、最適なタイミングでメンテナンスやサポートを提供することで、アフターサービスを充実させることができます。
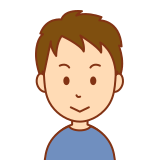
デジタルツインとは物理的なモノやシステム、あるいは人間の活動や行動を、サイバー空間に再現し、現実世界とリアルタイムにデータを連携させ、常にその状態を反映し、相互に影響し合うものです。
サイバー空間での試行は現実世界と比較して、時間もコストもかからないため、質や生産性の向上に大きく寄与できる技術です。
コメント