この記事で分かること
- 銅充填とは:ビアホールの中を銅で充填することで、上下の配線層を電気的に接続する工程です。
- 銅充填の方法:ビアホールの銅充填は主にダマシン法で行われます。まず穴を形成し、バリアメタル層と銅シード層を成膜し、その後、電解めっきでボイドなく銅を埋め込み、最後にCMPで余分な銅を除去し平坦化します。
- 電界めっきの添加剤とは:電解めっきの添加剤は、めっき液中の化学反応を制御します。抑制剤は表面での析出を抑え、促進剤はビアホール底部で析出を加速させ、ボトムアップフィリングを実現。平滑剤は膜を均一にし、微細構造への高品質な銅充填を可能にします。
ビアホールの銅充填
半導体の重要性が増す中で、前工程装置は世界的に成長が続いています。
https://optronics-media.com/news/20250414/99245/
特に中国は米中対立もあり、大幅な投資増加が続いています。今後も先端技術を駆使した半導体の需要増加と従来技術による成熟プロセスともにその重要性は増加するとみられています。
今回は、ビアホールを銅で充填する工程についての解説となります。
半導体の前工程とは
半導体の前工程とは、シリコンウェハ上にトランジスタや配線などの微細な回路を形成する一連のプロセスのことです。ウェハを素材として、集積回路を作り込んでいく、半導体製造の最も重要な部分と言えます。非常に多くの精密な工程を経て、最終的な半導体チップの機能が決まります。
主な前工程は以下の通りです。
ウェハ準備
シリコンインゴットの製造: 高純度のシリコンを溶解し、種結晶を用いて単結晶のシリコンインゴットを育成します。
- スライス: インゴットを薄い円盤状(ウェハ)にスライスします。
- 研磨: ウェハ表面を平坦かつ滑らかに研磨します。
- 洗浄: ウェハ表面の微細な異物や汚れを徹底的に除去します。
成膜
ウェハ表面に、酸化膜、窒化膜、金属膜など、様々な薄膜を形成します。
- 成膜方法には、CVD(化学気相成長法)、スパッタリング(物理気相成長法)、ALD(原子層堆積法)などがあります。
フォトリソグラフィ
ウェハ表面に感光材(フォトレジスト)を塗布します。
- 回路パターンが描かれたマスク(フォトマスク)を通して紫外線を照射し、レジストにパターンを焼き付けます。
- 現像液で不要なレジストを除去し、ウェハ上に回路パターンを形成します。
エッチング
フォトリソグラフィでパターン形成されたレジストをマスクとして、露出した成膜を除去し、ウェハに回路パターンを転写します。
- エッチングには、液体を用いるウェットエッチングと、プラズマを用いるドライエッチングがあります。
不純物導入(ドーピング)
半導体特性を持たせるために、リンやボロンなどの不純物をウェハ中に注入します。
- イオン注入法などが用いられます。
平坦化(CMP: Chemical Mechanical Polishing)
表面の凹凸をなくし、平坦にするための処理です。
- 化学的な腐食と 研磨を同時に行います。
配線形成(メタライゼーション)
形成されたトランジスタなどの素子間を金属配線で接続します。
- スパッタリングなどで金属膜を形成し、フォトリソグラフィとエッチングで配線パターンを作ります。
これらの工程を何度も繰り返し行うことで、複雑な集積回路がウェハ上に形成されます。前工程は、半導体の性能や品質を大きく左右する、非常に重要なプロセスです。
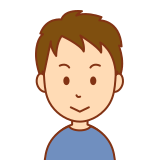
前工程は、微細な回路を形成する一連のプロセスのことで、半導体の性能や品質を大きく左右する、非常に重要なプロセスです。
ビアホールの銅の充填手順は
半導体デバイスにおけるビアホールへの銅充填は、主にダマシン法と呼ばれるプロセスによって行われます。これは、銅を直接エッチングすることが困難であるため開発された、非常に巧妙な技術です。
ダマシン法にはいくつかのステップがあり、それぞれが重要な役割を担っています。
1. ビアホールの形成
- まず、層間絶縁膜(Low-k材料など)の上に、フォトリソグラフィとドライエッチング(プラズマエッチング)を用いて、ビアホール(そして同時に配線用のトレンチ)のパターンを形成します。
- この段階では、ビアホールは単なる絶縁膜中の「穴」です。
2. バリアメタル層の成膜
- 次に、形成されたビアホールとトレンチの内部全体に、非常に薄いバリアメタル層を成膜します。
- 目的: 銅が層間絶縁膜や下地のシリコン中に拡散するのを防ぎ、デバイスの特性劣化を防ぐためです。
- 材料: 主にタンタル(Ta)やタンタル窒化物(TaN)が用いられます。コバルト(Co)やルテニウム(Ru)なども新しいバリア層として研究されています。
- 成膜方法: 主にPVD(物理気相成長、スパッタリング)や、より緻密で均一な膜が必要な場合はALD(原子層堆積)が用いられます。特に高アスペクト比のビアホールでは、側面や底面への均一な被覆性が求められるため、ALDの重要性が増しています。
3. 銅シード層の成膜
- バリアメタル層の上に、銅を電解めっきで成長させるための「足場」となる、非常に薄い銅の層(シード層)を成膜します。
- 成膜方法: 主にPVD(スパッタリング)で形成されます。ビアホールの底や側面への被覆性が重要です。
4. 銅の電解めっき(ビアホール充填の主工程)
- シード層が形成されたウェハーを、硫酸銅を主成分とするめっき液に浸し、電気化学反応によって銅を堆積させます。
- 特徴(ボトムアップフィリング): 微細なビアホールをボイド(空隙)なく完全に埋め込むため、特殊な添加剤がめっき液に配合されます。これらの添加剤(促進剤、抑制剤、平滑剤など)の作用により、ビアホールの底から優先的に銅が成長し、上方向へと充填されていく「ボトムアップフィリング」が実現されます。これにより、狭い穴の内部にボイドや継ぎ目(シーム)ができることなく、完全に銅が充填されます。
- めっきはビアホールやトレンチが完全に埋まるだけでなく、ウェハー表面全体が銅で覆われるオーバーフィル状態になるまで行われます。
5. 化学機械研磨(CMP: Chemical Mechanical Polishing/Planarization)
- めっきによって全面に堆積した余分な銅膜とバリアメタル層を、研磨剤(スラリー)と研磨パッドを用いて研磨・除去します。
- 目的: ビアホールとトレンチの内部にだけ銅が残るようにし、ウェハー表面を完全に平坦化します。これにより、次の層のフォトリソグラフィや成膜がスムーズに行えるようになります。
- CMPは、化学的なエッチング作用と機械的な研磨作用を組み合わせた技術であり、高精度な平坦化を実現します。
ダマシン法の種類
- シングルダマシン法: ビアホール形成・充填・CMPと、配線トレンチ形成・充填・CMPを別々に行う方法。
- デュアルダマシン法: 配線トレンチとビアホールを同時にエッチングで形成し、一度のバリアメタル、シード層、銅めっき、CMPで両方を形成する方法。プロセスステップを削減でき、現在の主流です。
これらの工程を経て、微細なビアホール内部に低抵抗な銅が充填され、多層配線が電気的に接続されます。
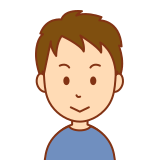
ビアホールの銅充填は主にダマシン法で行われます。まず穴を形成し、バリアメタル層と銅シード層を成膜し、その後、電解めっきでボイドなく銅を埋め込み、最後にCMPで余分な銅を除去し平坦化します。
電解めっきの添加剤の役割は何か
電解めっき、特に半導体製造における銅めっきでは、液中に微量の添加剤(Additive)が加えられます。これらの添加剤は、めっきの品質、特に微細なビアホールを完璧に埋め込むために不可欠な役割を担っています。
1. 抑制剤(Suppressor)
- 役割: めっき液中で銅イオンの析出を抑制する働きをします。特に、ビアホールの開口部や表面の平坦な部分で析出速度を遅らせることで、ビアホール内部(底)の成長を相対的に速める効果があります。
- メカニズム: 主にポリエチレングリコール(PEG)などの高分子化合物と塩化物イオン(Cl⁻)が組み合わされて使われます。これらがめっき表面に吸着し、銅イオンの移動や還元反応を妨げることで、銅の析出を抑制します。
2. 促進剤(Accelerator / Brightener)
- 役割: 抑制剤の効果が弱い、あるいは抑制剤が到達しにくいビアホールの底や側面で、銅イオンの析出を促進する働きをします。
- メカニズム: SPS(ビス(3-スルホプロピル)ジスルフィド)などの硫黄系化合物が代表的です。これらの分子は、ビアホールの底に優先的に吸着し、めっき反応を加速させると考えられています。抑制剤と促進剤の相互作用により、ビアホールの底から上に向かって銅が成長する「ボトムアップフィリング(Bottom-Up Filling)」が実現されます。これにより、狭いビアホールにボイド(空隙)やシーム(継ぎ目)なく銅を充填できます。
3. 平滑剤(Leveler)
- 役割: めっき膜の表面をより滑らかに、均一にする働きをします。
- メカニズム: 微細な凹凸がある場合、電流密度は凸部に集中しやすく、めっきが凸部に厚くつきがちです。平滑剤は、この凸部に優先的に吸着し、めっきの成長を抑制することで、全体の表面を平坦化する効果があります。これにより、均一な膜厚と良好な表面品質が得られます。
まとめ
これらの添加剤は、それぞれ異なる役割を持ちながらも、めっき液中で複雑に相互作用することで、半導体配線に求められる高い充填性(ボトムアップフィリング)、均一な膜厚、優れた表面平坦性、そして最終的な配線の信頼性を実現するために不可欠な存在です。添加剤の精密な管理と最適化は、高性能な半導体チップを製造する上で極めて重要な技術要素となっています。
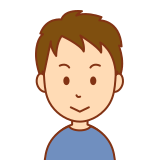
電解めっきの添加剤は、めっき液中の化学反応を制御します。抑制剤は表面での析出を抑え、促進剤はビアホール底部で析出を加速させ、ボトムアップフィリングを実現。平滑剤は膜を均一にし、微細構造への高品質な銅充填を可能にします。
なぜ、均一性が重要なのか
半導体製造における銅めっきで均一性が求められる理由は、多岐にわたる重要な要素に影響を与えるためです。これは、単に見た目の問題ではなく、デバイスの性能、信頼性、そして製造歩留まりに直結します。
- 電気的特性の均一性:
- 抵抗値の均一化: 配線の膜厚が均一でないと、場所によって抵抗値にばらつきが生じます。抵抗値のばらつきは、信号の伝送速度の不均一、電圧降下の変動、電流密度の偏りを引き起こし、LSI全体の動作速度や信号品質に悪影響を与えます。
- RC遅延の安定化: 配線の抵抗(R)と、隣接する配線との間の容量(C)によって生じるRC遅延は、LSIの動作速度を決定する重要な要素です。膜厚が均一でないと、RC遅延が予測不能になり、設計通りの性能が出せなくなります。
- デバイス信頼性の確保:
- エレクトロマイグレーション耐性: 銅配線に電流が流れると、電子との衝突により銅原子が移動するエレクトロマイグレーションという現象が起こり、配線が断線する原因となります。膜厚が不均一な場合、薄い部分に電流が集中しやすくなり、エレクトロマイグレーションが加速され、配線の寿命が短くなります。
- ストレスマイグレーション耐性: 銅配線は、製造プロセス中の温度変化によって生じる応力によっても、ボイド(空隙)が発生し、断線するストレスマイグレーションを起こすことがあります。均一な膜厚は、応力分布を均一化し、この現象を抑制します。
- 接合信頼性: ビアホール内部への銅の充填が均一でない場合、ボイドや欠陥が生じやすくなります。これは、ビアホールの導通不良や、その後の工程でのクラックの原因となり、電気的接続の信頼性を著しく低下させます。
- 後工程への影響と製造歩留まりの向上:
- CMP(化学機械研磨)の安定性: 銅めっきの後には、余分な銅を除去し表面を平坦化するためにCMPが行われます。めっき膜厚が不均一だと、CMPで研磨しすぎたり(オーバーポリッシュで下地を削る)、研磨が足りなかったり(アンダーポリッシュで平坦化不足)して、デバイス構造を破壊したり、平坦化の品質を損なったりします。均一な膜厚は、CMPプロセスの安定化と高精度な平坦化を実現し、不良の発生を抑えます。
- リソグラフィの精度: 後続のリソグラフィ工程では、膜表面の平坦性が重要です。めっき膜厚の不均一性は表面の凹凸につながり、露光時の焦点ズレを引き起こし、微細なパターンが正確に転写されにくくなります。
- ワイヤーボンディング性: チップと外部パッケージを接続するワイヤーボンディングにおいて、電極の膜厚が不均一だとボンディングの安定性や強度に影響が出ることがあります。
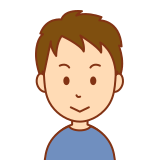
銅めっきの均一性は、配線の電気的性能、デバイスの長期信頼性、そして複雑な半導体製造プロセスの歩留まりを最大化するために不可欠な要素です。これを実現するために、電解めっき液の添加剤の精密な制御や、めっき装置の電流分布の最適化など、高度な技術が用いられています。
コメント