この記事で分かること
- 鍛造とは:金属を高温に加熱し、金型などを使って叩いたり押しつぶしたりして、目的の形状に成形する加工方法です。
- 鍛造の特徴:高強度・高靭性(じんせい)の部品が得られる、材料のムダが少なく、加工効率が良い反面、複雑な形状の部品には向かない場合がある、金型や設備のコストが高いなどデメリットがあります。
- 高強度・高靭性となる理由:内部が緻密になることで、欠陥が減り壊れにくくなることや金属内部の結晶組織が繊維のような役割を果たすことで、応力が強くなり、結晶粒が微細化することで割れにくくなります。
鍛造技術
経済産業省は「2025年版 素形材産業ビジョン」を策定しました。https://www.nikkan.co.jp/articles/view/00746425
これは、鋳造や鍛造、金型などの素形材産業を取り巻く環境変化に対応し、日本の製造業の競争力を維持・強化することを目的としています。前回のビジョン策定から約7年ぶりの刷新となります。
日本の素形材産業は、高性能・高品質な製品を製造できる強みを持っています。しかし、国内の人手不足や新興国との競争激化、新たな製造技術の導入など、厳しい状況に直面しています。
このような中、デジタル技術や人材などの経営資源を活用し、素形材産業の「稼ぐ力」を強化することが求められています。
前回の記事では、素形材とは何か、鋳造について解説しました。今回は鍛造についての記事となります。
鍛造(たんぞう)について
鍛造とは、金属を高温に加熱し、金型などを使って叩いたり押しつぶしたりして、目的の形状に成形する加工方法です。
刀鍛冶(かたなかじ)のように金属を打ち鍛えるイメージを思い浮かべるとわかりやすいです。
鍛造の特徴
- 金属内部の結晶構造(組織)が密になることで、非常に強度の高い部品ができます。
- 加工によって繊維状の構造(メタルフロー)ができ、それが強さにつながります。
- 主に自動車、航空機、産業機械など、強度が求められる部品に使われます。
鍛造の主な種類
- 熱間鍛造(ねっかんたんぞう) 加熱して柔らかくした金属を成形します。形状の自由度が高く、大きな力を加えやすいです。
- 冷間鍛造(れいかんたんぞう) 室温で金属を成形します。表面精度や寸法精度が高く、ばねやボルトなどによく使われます。
- 温間鍛造(おんかんたんぞう) 熱間と冷間の中間温度で加工する方法で、両者の利点をバランス良く活かせます。
鍛造品の代表例
- 自動車のクランクシャフトやコンロッド
- 航空機のエンジン部品
- 高圧配管用の継手(つぎて)
- 工具類(レンチ、ハンマーなど)
鍛造のメリット
- 高強度・高靭性(じんせい)の部品が得られる
- 材料のムダが少なく、加工効率が良い
- 長寿命の部品が作れる
鍛造のデメリット
- 複雑な形状の部品には向かない場合がある
- 金型や設備のコストが高い
- 加工時に大きな力が必要
鍛造は「強くて壊れにくいもの」を作るには最適な加工方法です。そのため、自動車や航空機のように「命を預ける」分野でとても重宝されています。
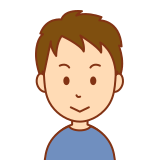
鍛造とは、金属を高温に加熱し、金型などを使って叩いたり押しつぶしたりして、目的の形状に成形する加工方法です。「強くて壊れにくいもの」を作るには最適な加工方法です。そのため、自動車や航空機のような分野で利用されています。
靭性とは何か
「靭性(じんせい)」は、材料の性質のひとつで、「壊れにくさ」「粘り強さ」を表す言葉です。
簡単に言うと「材料が衝撃や強い力を受けたときに、割れたり折れたりせずにエネルギーを吸収して耐える力」のことです。
靭性の強弱
- 硬いけどパキッと割れやすいガラス → 靭性が低い
- 多少変形してもなかなか壊れない鉄 → 靭性が高い
つまり、靭性が高い材料は「しなやかで強い」ということです。
材料の硬さ、強さを表す言葉
用語 | 意味 | 備考 |
---|---|---|
硬さ(硬度) | 表面の傷つきにくさ | 硬くても割れやすい場合がある |
強さ(引張強度など) | どれくらいの力で壊れるか | 靭性とは少し違う性質 |
靭性 | 壊れるまでにどれだけエネルギーを吸収できるか | 衝撃や繰り返し荷重への耐性を示す |
鍛造で加工された金属は、組織が引き締まり、靭性が高くなる傾向があります。そのため、自動車のクランクシャフトや航空機の部品など「壊れたら困る」部品にぴったりなんです。
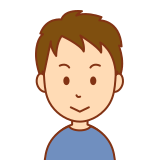
「靭性(じんせい)」は、材料の性質のひとつで、「壊れにくさ」「粘り強さ」を表す言葉で鍛造で加工された金属は、組織が引き締まり、靭性が高くなる傾向をもっています。
高強度・高靭性(じんせい)となる理由
鍛造によって高強度・高靭性になる主な理由は、次の3つです。
① 組織が緻密になる(きんみつになる)
鍛造では金属に圧力をかけて変形させるため、内部にあった空洞(ミクロな穴)や欠陥が潰されて詰まり、より密な構造になります。→ これにより、割れやすさや応力集中のリスクが減少し、靭性・強度が向上します。
② メタルフロー(鍛流線)が整う
鍛造によって金属内部の結晶組織(繊維状の流れ)が、部品の形に沿って「流れるような方向性」を持つようになります。→ これが繊維のような役割を果たし、力に対してしなやかに耐えるようになるのです。
鋳造との構造の違いのイメージ
- 鋳造品 → 板チョコを割ったようなランダムな構造
- 鍛造品 → 筋がそろった竹や炭のような構造(強い)
③ 結晶粒の微細化(グレインリファインメント)
金属の内部には「結晶粒(けっしょうりゅう)」と呼ばれる小さな粒が並んでいます。鍛造ではこの粒が叩き潰されて細かくなります。→ 粒が小さいほど、割れが進みにくくなり、結果的に強さと靭性が上がります(これを「ホール・ペッチ効果」と言います)。
このように、鍛造はただ形をつくるだけでなく、金属の“性格そのもの”を鍛え直す加工ともいえるんです
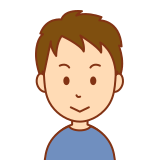
鋳造によって作られた金属は内部が緻密になることで、欠陥が減り壊れにくくなることや金属内部の結晶組織が繊維のような役割を果たすことで、応力が強くなり、結晶粒が微細化することで割れにくくなります。
このような特徴から高強度、高靭性をもたせることができます。
今後の鍛造に求められることは何か
今後の鍛造技術には、以下のような点が強く求められています。
1. 高機能・高精度化
- 高強度・軽量な部品の製造:特にEV化や航空機の軽量化に伴い、アルミ・チタン・高張力鋼などの難加工材の鍛造が求められています。
- 精密鍛造(ニアネットシェイプ):加工後の切削を最小限に抑え、材料ロスやコストを削減。
- 異形状・複雑形状の対応:多軸鍛造やサーボプレスなどで形状自由度を高める動きが進んでいます。
2. GX(グリーントランスフォーメーション)対応
- 鍛造炉の省エネ・電化:ガス炉から電気炉への転換、水素加熱技術の研究。
- 鍛造時の材料歩留まり向上:素材の無駄を減らす取り組み。
- カーボンフットプリントの削減:ライフサイクルでの環境負荷低減が企業に求められるように。
3. DX(デジタルトランスフォーメーション)の活用
- 鍛造シミュレーション(CAE)の高度化:金属流動、応力、温度分布の予測でトライ&エラーを削減。
- AI・IoTによる製造条件の最適化:プレス荷重・温度・金型の摩耗などをリアルタイムでモニタリングし、品質安定化。
- デジタルツインによる生産ラインの仮想検証:現場のトラブルや改善に迅速対応。
4. 自動化・省人化
- 鍛造機の自動化、ロボット搬送の導入:重労働の負担軽減と人手不足対策。
- 熟練技術者のノウハウのデジタル化:技能伝承と標準化を同時に実現。
5. グローバル競争力の強化
- 高付加価値品へのシフト(航空機・EV・医療部品など)
- 海外との価格・品質競争に勝てる生産性と信頼性の確保
- 海外拠点との連携・展開強化(特にアジア・北米)
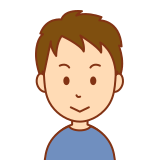
鍛造にも高機能化高精度化といった品質面以外にもやGXへの対応、DXの活用、自動化への対応などが求められています。
コメント