この記事で分かること
- ビアホールの金属充填とは:上下の配線層を電気的に接続し、回路として機能させるための工程です。電気的な接続以外にも、金属の熱伝導性を利用して、デバイスから発生する熱を効果的に放散する効果もあります。
- 使用される金属:主に低抵抗の銅やタングステンが用いられています。
- 銅の特徴:低抵抗、高エレクトロマイグレーション耐性、高熱伝導性が特徴で、LSIの高速化・低消費電力化に貢献します。しかし、直接エッチングが困難なためダマシン法が必須で、シリコン拡散防止のバリア層も必要です。
ビアホールの金属充填
半導体の重要性が増す中で、前工程装置は世界的に成長が続いています。
https://optronics-media.com/news/20250414/99245/
特に中国は米中対立もあり、大幅な投資増加が続いています。今後も先端技術を駆使した半導体の需要増加と従来技術による成熟プロセスともにその重要性は増加するとみられています。
今回はメタライゼーションの工程の一つであるビアホールの金属の充填と充填や配線に使用される銅の特徴についての記事となります。
半導体の前工程とは
半導体の前工程とは、シリコンウェハ上にトランジスタや配線などの微細な回路を形成する一連のプロセスのことです。ウェハを素材として、集積回路を作り込んでいく、半導体製造の最も重要な部分と言えます。非常に多くの精密な工程を経て、最終的な半導体チップの機能が決まります。
主な前工程は以下の通りです。
ウェハ準備
シリコンインゴットの製造: 高純度のシリコンを溶解し、種結晶を用いて単結晶のシリコンインゴットを育成します。
- スライス: インゴットを薄い円盤状(ウェハ)にスライスします。
- 研磨: ウェハ表面を平坦かつ滑らかに研磨します。
- 洗浄: ウェハ表面の微細な異物や汚れを徹底的に除去します。
成膜
ウェハ表面に、酸化膜、窒化膜、金属膜など、様々な薄膜を形成します。
- 成膜方法には、CVD(化学気相成長法)、スパッタリング(物理気相成長法)、ALD(原子層堆積法)などがあります。
フォトリソグラフィ
ウェハ表面に感光材(フォトレジスト)を塗布します。
- 回路パターンが描かれたマスク(フォトマスク)を通して紫外線を照射し、レジストにパターンを焼き付けます。
- 現像液で不要なレジストを除去し、ウェハ上に回路パターンを形成します。
エッチング
フォトリソグラフィでパターン形成されたレジストをマスクとして、露出した成膜を除去し、ウェハに回路パターンを転写します。
- エッチングには、液体を用いるウェットエッチングと、プラズマを用いるドライエッチングがあります。
不純物導入(ドーピング)
半導体特性を持たせるために、リンやボロンなどの不純物をウェハ中に注入します。
- イオン注入法などが用いられます。
平坦化(CMP: Chemical Mechanical Polishing)
表面の凹凸をなくし、平坦にするための処理です。
- 化学的な腐食と 研磨を同時に行います。
配線形成(メタライゼーション)
形成されたトランジスタなどの素子間を金属配線で接続します。
- スパッタリングなどで金属膜を形成し、フォトリソグラフィとエッチングで配線パターンを作ります。
これらの工程を何度も繰り返し行うことで、複雑な集積回路がウェハ上に形成されます。前工程は、半導体の性能や品質を大きく左右する、非常に重要なプロセスです。
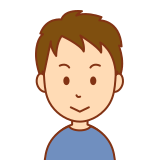
前工程は、微細な回路を形成する一連のプロセスのことで、半導体の性能や品質を大きく左右する、非常に重要なプロセスです。
ビアホールへの金属充填とは何か
半導体前工程におけるビアホールへの金属充填は、多層配線の電気的接続を確立するために極めて重要なプロセスです。
1. ビアホール充填の目的
ビアホールに金属を充填する主な目的は以下の通りです。
- 電気的接続: 上下の配線層を電気的に接続し、回路として機能させる。
- 信号伝送: 低抵抗の金属で充填することで、信号の高速伝送を可能にする。
- 熱放散: 特に高電力デバイスでは、金属の熱伝導性を利用して、デバイスから発生する熱を効果的に放散する。
- 平坦化: 後の工程(特にCMP)で表面を平坦化しやすくし、次の層の形成を容易にする。
- 信頼性向上: ボイド(空隙)のない充填により、信頼性の高い接続を確保する。
2. 主な充填材料
現在、半導体デバイスのビアホール充填に最も広く使用されている材料は以下の通りです。
- 銅 (Cu):
- 特徴: 低抵抗、優れた熱伝導性。アルミニウムに比べて遥かに低抵抗であるため、LSIの高速化・低消費電力化に不可欠。
- 用途: 最先端のロジックICの多層配線において、配線そのものだけでなく、ビアホール充填の主要材料として使用されています。
- タングステン (W):
- 特徴: 融点が高い、熱安定性に優れる、シリコンとの反応性が低い、異方性エッチングが可能。
- 用途: 主にトランジスタのゲート電極や、最初の配線層(コンタクトホール)の充填材料として使われることが多いです。微細な穴への埋め込み性に優れます。
- アルミニウム (Al) 系合金:
- 特徴: 比較的低抵抗、成膜しやすい。
- 用途: 以前は主要な配線材料でしたが、微細化に伴い抵抗が高くなる問題から銅に置き換わっています。一部のビアホール充填にも使われることがありましたが、現在は限定的です。
- 導電性ポリマー/エポキシ(銅/銀エポキシ):
- 特徴: コスト効率に優れる、フレキシブル基板などで使用されることがある。
- 用途: 主にプリント基板(PCB)のビアホール充填に使用されます。半導体チップ内部の微細なビアホールには適していません。
3. 主な充填方法
ビアホールへの金属充填は、穴の形状(アスペクト比)、材料の種類、求められる特性によって様々な方法が用いられます。
3.1. ダマシン法 (Damascene Process)
- 特徴: 現在の銅配線形成の主流。層間絶縁膜に配線パターン(トレンチ)とビアホールを同時に、または個別に形成し、その溝や穴全体に金属膜を堆積させた後、不要な部分をCMP(化学機械研磨)で除去して埋め込み配線を形成します。象嵌細工に似ているためこの名があります。
- プロセス:
- 層間絶縁膜にビアホールと配線トレンチをエッチングで形成。
- バリアメタル層の成膜: 銅の拡散を防ぐため、タングステン(W)、タンタル(Ta)、タンタル窒化物(TaN)などの薄い膜をPVD(物理気相成長)やALD(原子層堆積)で形成。
- シード層の成膜: 銅を成長させるための薄い銅の層(シード層)をPVDで形成。
- 電解めっき (Electroplating): シード層を足場として、ビアホールやトレンチ全体に銅をめっきで堆積させます。高い埋め込み性が得られます。
- CMP(化学機械研磨): ウェハー表面の余分な銅膜とバリアメタル層を研磨して除去し、ビアホールとトレンチ内部の銅配線だけを残します。
- 種類:
- シングルダマシン法: 配線層とビア層を別々に形成し、それぞれをCMPで平坦化する方法。
- デュアルダマシン法: 配線トレンチとビアホールを一度に形成し、一度の金属充填とCMPで両方を形成する方法。プロセスステップを削減できるため、現在の主流です。
3.2. CVD (Chemical Vapor Deposition)
- 特徴: 気相から化学反応によって膜を成膜する方法。特にタングステン(W)の充填によく用いられます。良好な段差被覆性と埋め込み性を提供します。
- プロセス: タングステンヘキサフルオリド (WF6) などのガスを反応させ、熱エネルギーを与えてタングステンを堆積させます。
- 用途: 微細なコンタクトホールやビアホールの充填に適しており、ボイド(空隙)の少ない充填が可能です。
3.3. PVD (Physical Vapor Deposition) – スパッタリング/蒸着
- 特徴: ターゲット材料を物理的に飛ばして基板に堆積させる方法。
- 用途: 主にバリアメタル層やシード層の薄膜形成に用いられます。微細なビアホールへの均一な埋め込みは難しい場合があります(開口部が狭いため、側面への被覆性が低下しやすい)。
4. 技術的課題
ビアホールへの金属充填は、LSIの微細化が進むにつれて多くの技術的課題に直面しています。
- 高アスペクト比への対応: 微細化により、ビアホールの直径は小さくなる一方で深さはあまり変わらないため、アスペクト比(深さ/直径)が非常に高くなります。このような深くて狭い穴の底まで均一にバリアメタルやシード層を成膜し、ボイドなく金属を充填することが非常に困難です。
- 埋め込み性の確保: 特に電解めっきにおいて、微細な穴の内部にボイドやシーム(継ぎ目)なく金属を充填するための、添加剤やプロセス条件の最適化が重要です。
- バリア性の確保: 銅は層間絶縁膜中に拡散しやすく、デバイス特性を劣化させるため、強固なバリアメタル層の形成が不可欠です。薄膜化と高いバリア性を両立させる必要があります。
- CMPによる平坦化: 埋め込んだ金属を効率的かつ均一に除去し、表面を平坦に保つためのCMP技術の精度向上が求められます。
- 信頼性: 充填された金属の抵抗安定性、エレクトロマイグレーション(電流による金属原子の移動)耐性、ストレスマイグレーション(応力による金属原子の移動)耐性など、長期的な信頼性の確保が重要です。
これらの課題を克服するため、ALD(原子層堆積)による超薄膜バリア層の形成、新しいめっき添加剤の開発、革新的なCMP技術などが研究開発されています。
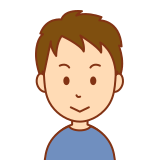
ビアホールへの金属充填は、上下の配線層を電気的に接続する重要工程です。主に低抵抗の銅(Cu)やタングステン(W)が用いられ、ダマシン法(電解めっきとCMP)やCVDで形成されます。微細化に伴う高アスペクト比穴へのボイドフリー充填と信頼性確保が課題です。
銅の特徴は何か
半導体配線において、銅(Cu)は、従来のアルミニウム(Al)配線に代わるものとして、現代のLSIの高性能化に不可欠な技術となっています。その主な特徴は以下の通りです。
1. メリット(長所)
- 低い電気抵抗率:
- 銅はアルミニウムに比べて約30%低い抵抗率を持ちます。これは、同じ太さの配線であれば、銅の方が電気をはるかに効率的に流せることを意味します。
- LSIの微細化が進み、配線の断面積が小さくなるにつれて、配線抵抗が増大し、信号遅延(RC遅延)が問題となります。低抵抗の銅を用いることで、この遅延を大幅に削減し、LSIの高速動作を可能にします。
- 高いエレクトロマイグレーション耐性:
- エレクトロマイグレーションとは、配線に大電流を流し続けることで、電子と金属原子の衝突により金属原子が移動し、配線の断線や短絡を引き起こす現象です。
- 銅はアルミニウムに比べてエレクトロマイグレーションに対する耐性が1桁以上高く、より大電流を流すことができ、デバイスの長期信頼性を向上させます。
- 高い熱伝導率:
- 銅はアルミニウムよりも熱伝導率が高いため、配線に電流が流れて発生するジュール熱を効率的に拡散させることができます。これにより、配線の局所的な過熱を防ぎ、信頼性の低下やエレクトロマイグレーションの加速を抑制します。
- 低消費電力化への貢献:
- 抵抗が低いため、配線での電力損失を抑えることができます。これは、LSI全体の消費電力削減に寄与します。
2. デメリット(課題)
- エッチングが困難:
- 銅は揮発性のエッチングガスを形成しにくいため、従来のアルミニウム配線のようにプラズマ(ドライ)エッチングで直接パターニングすることが非常に困難です。
- このため、ダマシン法という特殊なプロセスが開発され、これが銅配線の主流となっています。ダマシン法では、まず層間絶縁膜に配線の溝やビアホールを形成し、その中に銅を埋め込み、余分な銅をCMP(化学機械研磨)で除去します。
- シリコン基板への拡散:
- 銅はシリコン基板や層間絶縁膜(特にシリコン酸化膜)中に容易に拡散し、デバイスの電気的特性を劣化させる可能性があります。
- これを防ぐため、銅配線の周囲にはバリアメタル層(タンタル、タンタル窒化物など)が必須となります。
- 応力誘起ボイド(ストレスマイグレーション):
- 銅と周囲の絶縁膜との熱膨張係数の違いにより、冷却時に配線に応力が生じ、ボイド(空隙)が発生することがあります。これにより配線が断線する現象をストレスマイグレーションと呼びます。
- この現象はアルミニウムよりも銅の方が起こりやすいとされており、特に微細化が進むと顕在化するため、プロセス条件や構造の最適化が重要です。
- 加工・管理の難しさ:
- 銅はアルミニウムよりも酸化しやすく、デリケートな材料であるため、製造プロセスにおける汚染管理や取り扱いがより厳密に求められます。
これらのメリットとデメリットを総合的に考慮し、半導体業界では銅の低抵抗・高信頼性というメリットを最大限に活かすために、ダマシン法やバリアメタル技術などの革新的なプロセス技術が開発・導入されてきました。これにより、銅配線は現代の高性能LSIにおいて不可欠な要素となっています。
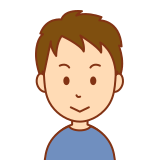
銅配線は低抵抗、高エレクトロマイグレーション耐性、高熱伝導性が特徴で、LSIの高速化・低消費電力化に貢献します。しかし、直接エッチングが困難なためダマシン法が必須で、シリコン拡散防止のバリア層も必要です。
なぜ、初期の半導体で銅ではなく、アルミニウムが使用されていたのか
半導体配線において、当初アルミニウム(Al)が使用され、後に銅(Cu)に置き換わっていったのは、当時の技術的制約と、アルミニウムが持っていた加工上の利点が大きかったためです。
主な理由は以下の通りです。
- 加工の容易さ(特にエッチング):
- アルミニウム: アルミニウムとその合金は、フッ素系や塩素系のガスを用いたプラズマ(ドライ)エッチングによって、容易にパターニングすることが可能でした。揮発性の副生成物(塩化アルミニウムなど)が生成されるため、精密な配線パターンを形成しやすかったのです。
- 銅: 銅は、通常のプラズマエッチングでは揮発性の副生成物を形成しにくいため、直接パターニングが非常に困難でした。この問題は、銅配線が実用化されるまで長年大きな障壁となっていました。銅を実用化するためには、ダマシン法という全く新しいプロセス技術(溝を掘ってから埋め込む方式)の開発が不可欠でした。
- 既存技術との親和性:
- アルミニウムは、半導体製造の初期から使用されていたシリコン酸化膜との相性も比較的良く、既存のプロセス技術(成膜、エッチング、ボンディングなど)と容易に組み合わせることができました。
- 当時、LSIの性能向上は主にトランジスタの微細化によって達成されており、配線性能の要求はそれほど高くありませんでした。アルミニウムは当時のニーズを満たす十分な導電性を持っていました。
- 拡散の問題:
- 銅はシリコンやシリコン酸化膜中に容易に拡散し、トランジスタの特性を著しく劣化させるという大きな問題がありました。これを防ぐためには、銅の拡散を遮断するバリアメタル層が必要でしたが、その技術開発も当時の課題でした。アルミニウムはそのような深刻な拡散の問題は抱えていませんでした。
- 低コストと豊富な供給:
- アルミニウムは非常に安価で、供給も安定しており、当時としては経済的な選択肢でした。
銅への移行の背景
1990年代後半に入り、LSIの集積度が向上し、配線が極めて微細化されると、アルミニウム配線では以下の問題が顕在化しました。
- RC遅延の増大: 配線抵抗と配線間容量が無視できないほど大きくなり、LSIの動作速度が頭打ちになる。
- エレクトロマイグレーションによる信頼性低下: 配線幅の縮小と電流密度の増大により、アルミニローム配線の断線リスクが高まる。
これらの問題を解決するために、より低抵抗でエレクトロマイグレーション耐性の高い銅が注目されるようになり、ダマシン法や高性能バリアメタル層などの画期的なプロセス技術が開発されたことで、ようやく銅配線が実用化され、現在の半導体デバイスの主流となりました。
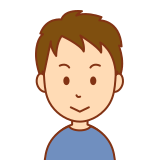
始めから銅を使用しなかったのは、当時の技術レベルでは銅を半導体配線として実用化するための加工技術が未熟であり、アルミニウムの方が製造上の優位性(特にエッチング性)が高かったためです。
コメント