この記事で分かること
- 粉末冶金とは:金属粉末を金型に入れて圧縮成形した後、高温で焼結することで、目的とする材料を得るための手法です。
- 粉末冶金の特徴:複雑な形状の部品を効率的に製造可能であり、材料の無駄が少ない、多様な材料の組み合わせなどの特長があります。
- 複合材料が得意な理由:材料を原子レベルで溶解・混合するのではなく、粉末という中間形態を経ることで、従来の溶解鋳造法では難しかった多様な材料の組み合わせを可能にしています。
粉末冶金
経済産業省は2025年3月28日、「2025年版 素形材産業ビジョン」を策定しました。これは、鋳造や鍛造、金型などの素形材産業を取り巻く環境変化に対応し、日本の製造業の競争力を維持・強化することを目的としています。
今回は、素材材産業の中での粉末冶金についての記事になります。
粉末冶金とは何か
粉末冶金(ふんまつやきん)は、金属粉末を金型に入れて圧縮成形した後、高温で焼結(しょうけつ)することで、目的の形状と特性を持つ製品を作り出す技術です。
粉末冶金法の主な工程
- 原料粉末の準備・混合: 鉄、銅、ニッケル、クロム、タングステン、モリブデンなどの金属粉末や、合金粉末を必要に応じて混合します。
- 成形: 混合した粉末を、目的の形状をした金型に充填し、プレス機で高い圧力をかけて圧縮成形します。この工程で、最終製品に近い形状が得られます(ニアネットシェイプ)。
- 焼結: 成形された粉末成形体を、焼結炉と呼ばれる高温の炉で加熱します。この熱処理により、金属粉末同士が結合し、強度を持った緻密な製品となります。
- 後処理(必要に応じて): 焼結後、さらに寸法精度を高めるためのサイジング、機械的強度を向上させるための熱処理、表面の腐食を防ぐための表面処理などが行われることがあります。
粉末冶金法のメリット
- 複雑な形状の部品を効率的に製造可能: 金型を用いるため、複雑な形状の部品を高い精度で大量生産できます。
- 材料の有効活用: 最終製品に近い形状で成形するため、切削加工などの後工程が少なく、材料の無駄を減らせます。
- 多様な材料の組み合わせ: 異なる金属や、金属と非金属の複合材料など、通常の溶解法では難しい組み合わせの材料も製造できます。
- 高融点金属や難加工材の成形: 融点の高い金属や、切削加工が難しい材料でも成形が可能です。
- 多孔質材料の製造: 内部に微細な気孔を持つ材料を作ることができ、含油軸受や制振材料などに利用されます。
- コスト削減: 大量生産に適しており、後加工が少ないため、トータルコストを抑えられます。
- 軽量化: 製品内部の気孔を利用することで、軽量な部品を製造できます。
粉末冶金法のデメリット
- 初期投資が高い: 金型や焼結炉などの専用設備が必要なため、初期投資が高額になる場合があります。
- 大型・肉厚な製品には不向き: 成形や焼結の際に寸法変化が大きくなる可能性があり、大型製品や肉厚製品の製造は難しい場合があります。
- 密度にばらつきが生じる可能性: 製品の形状によっては、粉末の充填密度にばらつきが生じることがあります。
- 材料コストが高い場合がある: 特殊な金属粉末を使用する場合など、材料費が高くなることがあります。
- 微細な部品の成形が難しい場合がある: 粉末の特性上、非常に微細な形状の部品を高い精度で成形することは難しいことがあります。
- 強度が鋳造や鍛造に劣る場合がある: 焼結時に気孔が残ることがあり、一般的に鋳造や鍛造に比べて強度がやや劣る場合があります。
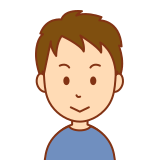
粉末冶金は、金属粉末を金型に入れて圧縮成形した後、高温で焼結することで、目的とする材料を得るための手法です。
多様な材料の組み合わせが可能な理由は?
粉末冶金で多様な材料の組み合わせが可能な理由は、主に以下の点が挙げられます。
1. 固相反応を利用できる
鋳造のように材料を完全に溶融させるのではなく、粉末状のまま混合し、焼結という固体の状態で結合させるため、融点の大きく異なる材料同士でも組み合わせやすいという利点があります。
例えば、融点の非常に高いタングステンと、比較的低いコバルトを組み合わせて超硬合金を作ることができます。
これは、鋳造ではタングステンが完全に溶融する温度でコバルトが蒸発してしまうため、困難な組み合わせです。
2. 物理的な混合が容易
粉末状の材料であれば、組成や粒径などを細かく制御しながら、物理的に均一に混合することができます。
これにより、マクロなレベルで均質な複合材料を作製することが可能です。鋳造では、溶融した状態での均一な混合が難しい場合や、比重差によって分離してしまうことがあります。
3. 組織制御の自由度が高い
焼結時の温度や雰囲気、時間などを調整することで、材料間の反応を制御し、微細組織をコントロールすることができます。
これにより、目的とする特性(強度、耐摩耗性、耐食性など)を最大限に引き出すような組織設計が可能になります。
例えば、金属とセラミックスの複合材料において、界面の結合状態を制御することで、強度と靭性を両立させることができます。
4. 多孔質構造の利用
粉末冶金では、焼結条件を調整することで、内部に意図的に気孔を残した多孔質材料を作製することができます。
この多孔質構造を利用して、異なる材料を浸み込ませたり、充填したりすることで、複合材料を作製することができます。
例えば、多孔質の金属骨格に樹脂を浸み込ませることで、軽量で減衰性の高い材料を作ることができます。
5. ニアネットシェイプによる制約の緩和
鋳造では、複雑な形状の製品を作る際に、材料の流動性や凝固収縮などが制約となる場合があります。
一方、粉末冶金では、金型で所望の形状に成形してから焼結するため、比較的複雑な形状でも、異なる材料を組み合わせた製品を作りやすいという側面があります。
具体例
- 超硬合金 (WC-Co): 硬い炭化タングステン(WC)の粉末と、結合材として靭性のあるコバルト(Co)の粉末を混合して焼結することで、非常に硬く耐摩耗性に優れた工具材料が得られます。
- サーメット (TiC-Niなど): セラミックス(炭化チタン TiCなど)と金属(ニッケル Niなど)の粉末を組み合わせることで、高温強度と耐摩耗性を兼ね備えた材料が得られます。
- 含油軸受: 多孔質の金属(主に銅合金や鉄系合金)に潤滑油を含浸させることで、自己潤滑性を持つ軸受が得られます。
- 金属基複合材 (MMC): 金属マトリックス中に、セラミックス粒子や繊維などを分散させることで、強度、剛性、耐摩耗性などを向上させた材料が得られます。
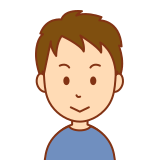
粉末冶金は、材料を原子レベルで溶解・混合するのではなく、粉末という中間形態を経ることで、従来の溶解鋳造法では難しかった多様な材料の組み合わせを可能にしています。
成形や焼結の際に寸法変化が大きくなる理由は
粉末冶金における成形や焼結の際に寸法変化が大きくなる主な理由は、以下の通りです。
成形時の寸法変化
成形工程では、金属粉末を金型に充填し、高い圧力をかけて圧縮します。この際に起こる寸法変化の主な要因は以下の通りです。
- 粉末の充填密度: 金型に充填される粉末の密度は均一ではありません。粉末の粒径、形状、流動性などによって、場所によって密度にばらつきが生じます。この密度の低い部分と高い部分で、圧縮時の変形量が異なるため、成形体全体として均一な寸法変化が起こりにくくなります。
- 圧縮圧力の分布: 金型内で均一に圧力が加わるとは限りません。金型の形状や粉末の摩擦などにより、圧力分布が生じ、それによって圧縮率が異なるため、寸法にばらつきが出ます。
- 粉末の塑性変形と粒子間の再配列: 圧力を加えることで、粉末粒子が塑性変形したり、粒子同士がより密になるように再配列したりします。この過程で、体積が減少し、寸法が変化します。
- 金型の弾性変形: 高い圧力が金型に加わるため、金型自体もわずかに弾性変形します。圧力が解放されると金型が元に戻るため、成形体にもわずかな寸法変化が生じます。
- バインダーの影響(MIMなどの場合): 金属粉末射出成形(MIM)のように、バインダーと呼ばれる有機物を粉末に混ぜて成形する場合、バインダーの体積収縮や、その後の脱脂工程でバインダーが除去されることによって、大きな寸法変化が生じます。
焼結の寸法変化
焼結工程では、成形体を高温で加熱し、金属粉末同士を結合させます。この際に起こる寸法変化の主な要因は以下の通りです。
- 緻密化(ちみつか): 焼結の主な目的は、粉末粒子間の空隙を減らし、密度を高めることです。原子拡散などの現象により、粒子同士が結合すると同時に、空隙が収縮するため、成形体全体が収縮します。この収縮率は、元の成形体の密度や焼結条件(温度、時間、雰囲気)によって大きく異なります。
- ネック成長: 焼結初期には、粉末粒子同士が接触している部分(ネック)が成長します。このネック成長も緻密化に寄与し、収縮を引き起こします。
- 粒成長: 焼結温度が高すぎたり、時間が長すぎたりすると、金属の結晶粒が成長し、これも寸法変化の原因となることがあります。
- 合金化: 複数の金属粉末を混合して焼結する場合、焼結中に金属間で合金化が起こることがあります。合金化の際に、体積が膨張または収縮することがあり、これが寸法変化につながります。
- 液相焼結: 一部の粉末が焼結温度で液体になる場合(液相焼結)、液体の表面張力によって粒子間の空隙が埋められ、大きな収縮が起こることがあります。
- 雰囲気ガスの影響: 焼結炉内の雰囲気ガスが、金属粉末と反応して酸化物を生成したり、脱炭反応を起こしたりすることで、寸法が変化する場合があります。
- 重力や摩擦: 焼結中に、自重によって変形したり、炉の治具との摩擦によって収縮が妨げられたりすることで、均一な寸法変化が得られないことがあります。
これらの要因が複雑に絡み合って、成形時や焼結時に寸法変化が生じます。
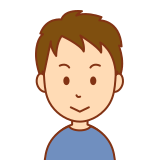
成型時には、粉末の充填密度のばらつきや圧力分布が生じるなどの理由から、焼結時には、粒子同士が結合による緻密化や金属の粒成長などで寸法の変化が起こります。
コメント