この記事で分かること
- 配線形成、メタライゼーションとは:トランジスタなどの素子同士を電気的に接続するため、金属膜を成膜・加工し、多層の電気配線を構築する技術です。これにより、LSIとして機能する回路が完成します。
- 使用される金属:配線としてアルミニウムや銅、バリアメタルとしてタングステンやチタンなどが利用されています。
- 製法:主にサブトラクティブ法で配線に利用されます。これは、まずウェーハ全面にアルミニウム膜を成膜し、その上にリソグラフィでパターンを形成。その後、不要なアルミニウム部分をエッチングで除去することで、配線を形成する手法です。
配線形成、メタライゼーション
半導体の重要性が増す中で、前工程装置は世界的に成長が続いています。
https://optronics-media.com/news/20250414/99245/
特に中国は米中対立もあり、大幅な投資増加が続いています。今後も先端技術を駆使した半導体の需要増加と従来技術による成熟プロセスともにその重要性は増加するとみられています。
今回は、配線形成、メタライゼーションの解説となります。
半導体の前工程とは
半導体の前工程とは、シリコンウェハ上にトランジスタや配線などの微細な回路を形成する一連のプロセスのことです。ウェハを素材として、集積回路を作り込んでいく、半導体製造の最も重要な部分と言えます。非常に多くの精密な工程を経て、最終的な半導体チップの機能が決まります。
主な前工程は以下の通りです。
ウェハ準備
シリコンインゴットの製造: 高純度のシリコンを溶解し、種結晶を用いて単結晶のシリコンインゴットを育成します。
- スライス: インゴットを薄い円盤状(ウェハ)にスライスします。
- 研磨: ウェハ表面を平坦かつ滑らかに研磨します。
- 洗浄: ウェハ表面の微細な異物や汚れを徹底的に除去します。
成膜
ウェハ表面に、酸化膜、窒化膜、金属膜など、様々な薄膜を形成します。
- 成膜方法には、CVD(化学気相成長法)、スパッタリング(物理気相成長法)、ALD(原子層堆積法)などがあります。
フォトリソグラフィ
ウェハ表面に感光材(フォトレジスト)を塗布します。
- 回路パターンが描かれたマスク(フォトマスク)を通して紫外線を照射し、レジストにパターンを焼き付けます。
- 現像液で不要なレジストを除去し、ウェハ上に回路パターンを形成します。
エッチング
フォトリソグラフィでパターン形成されたレジストをマスクとして、露出した成膜を除去し、ウェハに回路パターンを転写します。
- エッチングには、液体を用いるウェットエッチングと、プラズマを用いるドライエッチングがあります。
不純物導入(ドーピング)
半導体特性を持たせるために、リンやボロンなどの不純物をウェハ中に注入します。
- イオン注入法などが用いられます。
平坦化(CMP: Chemical Mechanical Polishing)
表面の凹凸をなくし、平坦にするための処理です。
- 化学的な腐食と 研磨を同時に行います。
配線形成(メタライゼーション)
形成されたトランジスタなどの素子間を金属配線で接続します。
- スパッタリングなどで金属膜を形成し、フォトリソグラフィとエッチングで配線パターンを作ります。
これらの工程を何度も繰り返し行うことで、複雑な集積回路がウェハ上に形成されます。前工程は、半導体の性能や品質を大きく左右する、非常に重要なプロセスです。
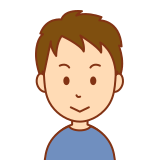
前工程は、微細な回路を形成する一連のプロセスのことで、半導体の性能や品質を大きく左右する、非常に重要なプロセスです。
配線形成、メタライゼーションとは何か
半導体前工程における配線形成(メタライゼーション)とは、半導体チップ内で、トランジスタなどの素子同士を電気的に接続し、回路として機能させるために、金属の配線を形成する一連の技術とプロセスを指します。
- 金属配線層の形成:
- 材料: 主にアルミニウム (Al) や銅 (Cu) などの低抵抗金属、およびそれらの合金が用いられます。微細化が進むにつれて、より抵抗の低い銅への転換が進んでいます。また、配線材料とシリコンとの反応を防ぐためのバリアメタル(タングステン (W)、チタン (Ti) など)も使用されます。
- 成膜方法: 物理的成膜法 (PVD: 蒸着、スパッタリング) や化学的成膜法 (CVD: Chemical Vapor Deposition) などが用いられます。特に銅配線では、めっき法やダマシン法(後述)が活用されます。
- ビアホールの埋め込み: 複数の配線層を接続するために、層間絶縁膜に開けられたビアホール(穴)に金属を埋め込む技術です。タングステンなどが一般的に用いられます。
- 層間絶縁膜の形成: 配線層同士を電気的に絶縁するための膜を形成します。シリコン酸化膜が一般的ですが、信号伝達の遅延を抑えるために、より誘電率の低い(低誘電率)材料も研究されています。
- 平坦化技術: 多層配線を形成する際に生じる凹凸をなくし、表面を平坦にする技術です。CMP (Chemical Mechanical Polishing: 化学機械研磨) が代表的です。
- 配線信頼性評価技術: 形成された配線の電気的特性や信頼性(エレクトロマイグレーションなど)を評価する技術も含まれます。
なぜメタライゼーションが重要なのか?
半導体デバイスは、トランジスタなどの個々の素子が作られただけでは機能しません。それらの素子を適切に接続することで初めて、LSI(大規模集積回路)として複雑な演算やデータ処理が可能になります。メタライゼーションは、この「電気的な道筋」を作る極めて重要な工程であり、LSIの性能(高速性、低消費電力など)や信頼性に大きく影響します。
特に、近年における半導体の微細化と多層化の進展に伴い、配線の抵抗や寄生容量による信号遅延がLSIの高速化を妨げる大きな課題となっています。そのため、より低抵抗な材料の採用(例:AlからCuへ)、低誘電率の層間絶縁膜の開発、そしてそれらの材料を微細かつ高精度に加工する技術(ダマシン法など)が、メタライゼーション技術の進化を牽引しています。
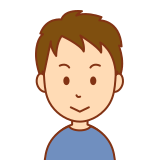
半導体前工程の配線形成(メタライゼーション)は、トランジスタなどの素子同士を電気的に接続するため、金属膜を成膜・加工し、多層の電気配線を構築する技術です。これにより、LSIとして機能する回路が完成します。
アルミニウムはどのように使用されるのか
アルミニウムは、長らく半導体デバイスの配線材料として標準的に使用されてきました。その主な使用方法は、サブトラクティブ法と呼ばれるプロセスです。
サブトラクティブ法におけるアルミニウム配線の形成
- 層間絶縁膜の成膜: まず、下層のトランジスタや配線層の上に、電気的に絶縁するための層間絶縁膜(主にシリコン酸化膜)が成膜されます。
- アルミニウム膜の全面成膜: 次に、その絶縁膜の表面全体に、PVD(物理気相成長法)の一種であるスパッタリングによって、アルミニウム(Al)またはアルミニウム合金(通常、エレクトロマイグレーション耐性向上のため微量の銅を添加したAl-Cu合金)の薄膜を均一に成膜します。
- レジスト塗布と露光・現像(リソグラフィ): 成膜されたアルミニウム膜の上に、感光性のフォトレジストが塗布されます。その後、配線パターンが描かれたマスクを通して紫外線などを露光し、現像することで、配線として残したい部分のレジストが残り、不要な部分のレジストが除去されます。
- エッチング: 残ったフォトレジストをマスクとして、その下の不要なアルミニウム膜を化学的、または物理的に削り取ります(エッチング)。ドライエッチング(プラズマエッチング)が一般的です。これにより、アルミニウムの配線パターンが形成されます。
- レジスト除去: 最後に、残ったフォトレジストを除去します。
この後、必要に応じて次の層間絶縁膜の成膜、平坦化(CMP)、そして次の配線層の形成、というプロセスが繰り返され、多層配線が構築されていきます。
アルミニウム配線の利点と欠点
利点
- 加工の容易性: アルミニウムはエッチングによる加工が比較的容易であり、従来の半導体製造プロセスとの適合性が高かった。
- コストの低さ: 銅に比べて材料費が安価であり、製造コストを抑えることができた。
- 安定性: 酸化膜が表面に自然に形成されるため、安定性が高い。
欠点
- 高い電気抵抗: 銅に比べて電気抵抗が高いため、微細化が進むと配線抵抗による信号遅延(RC遅延)が顕著になり、デバイスの高速化の妨げとなる。
- エレクトロマイグレーション耐性: 電子が金属原子を移動させる現象(エレクトロマイグレーション)に対する耐性が銅に比べて低く、配線の断線を引き起こすリスクがあった。
- 熱伝導率: 銅に比べて熱伝導率が低いため、発熱対策の面で不利となる場合がある。
現在の傾向
微細化と高性能化が進むにつれて、アルミニウム配線は、より電気抵抗の低い銅(Cu)配線へと置き換えが進んでいます。銅配線は、エッチングが困難であるため、ダマシン法と呼ばれる異なるプロセス(絶縁膜に溝を掘り、そこに銅を埋め込む方法)が主流となっています。
しかし、アルミニウム配線は、その加工の容易さとコストの低さから、一部の特定の用途や、より古い世代のプロセスルールを用いたデバイスにおいては、現在でも使用され続けています。
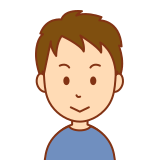
アルミニウムはメタライゼーションにおいて、主にサブトラクティブ法で配線に利用されます。これは、まずウェーハ全面にアルミニウム膜を成膜し、その上にリソグラフィでパターンを形成。その後、不要なアルミニウム部分をエッチングで除去することで、配線を形成する手法です。
サブトラクティブ法とは何か
サブトラクティブ法(Subtractive Process)は、「引き算」を意味する「Subtractive」の名の通り、材料を削り取ることで目的の形状を作り出す加工方法全般を指します。半導体製造の文脈では、主に配線形成において、この手法が用いられます。
具 体的には、半導体ウェーハの上にまず材料を全面に薄く均一に堆積させ、その後、フォトリソグラフィ(露光・現像)とエッチング(削り取り)の技術を組み合わせて、不要な部分の材料を除去し、必要なパターン(配線など)を残すプロセスを指します。
サブトラクティブ法の一般的な手順(半導体配線形成の場合)
- 材料の全面成膜: ウェーハの表面に、配線の材料となる金属(例:アルミニウム)や、層間を絶縁する材料(例:シリコン酸化膜)を、CVD(化学気相成長法)やPVD(物理気相成長法)などの方法で薄く均一に堆積させます。
- フォトレジスト塗布: 成膜された材料の上に、光に反応する感光性樹脂であるフォトレジストを均一に塗布します。
- 露光: 作成したい配線パターンが描かれたフォトマスクを通して、フォトレジストに光(通常は紫外線)を照射します。これにより、光が当たった部分のフォトレジストの性質が変化します。
- 現像: 特定の現像液を用いて、光が当たった(または当たらなかった)部分のフォトレジストのみを除去します。これにより、下の材料層がパターン状に露出した部分と、フォトレジストで覆われた部分ができます。
- エッチング: 残ったフォトレジストをマスクとして、露出した下の材料層を化学的(ウェットエッチング)または物理的(ドライエッチング/プラズマエッチング)に削り取ります。これにより、フォトレジストで覆われていた部分の材料だけが、目的の配線パターンとして残ります。
- フォトレジスト除去: 最後に、役目を終えたフォトレジストを剥離(アッシング)して除去します。
この一連のプロセスにより、希望する配線パターンがウェーハ上に形成されます。
サブトラクティブ法の特徴
- 利点:
- 歴史が長く、技術が成熟している: 半導体製造において長年にわたり使用されてきたため、安定したプロセスが確立されています。
- コスト効率: 大量生産において比較的コスト効率が良い場合があります。
- 多様な材料に適用可能: 金属だけでなく、酸化膜などの絶縁膜の加工にも広く使われます。
- 欠点:
- サイドエッチング: エッチングの際に、マスクの下にも材料が削り取られてしまう「サイドエッチング」が発生し、微細なパターン形成の限界となることがあります。
- 材料の無駄: 全面に成膜した材料の大部分を削り取るため、材料の無駄が多い。
- 銅配線への不向き: 銅はドライエッチングが困難であるため、銅配線には別の手法(ダマシン法)が主流となっています。
対照的な加工方法として、材料を必要な場所に「付け足していく」アディティブ法(Additive Process)があります。半導体配線では、銅配線で主流のダマシン法がこのアディティブ的な考え方に近いと言えます。
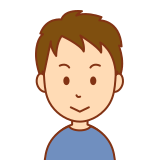
サブトラクティブ法は、半導体配線形成において、まず材料(Alなど)を全面に成膜します。その後、フォトリソグラフィでパターンを形成したレジストをマスクとし、不要な部分をエッチングで削り取る(引き算する)ことで、目的の配線パターンを作り出す加工技術です。
コメント