この記事で分かること
- ウエハの洗浄とは:パーティクル、金属不純物や有機物などの除去のために行われます。全行程の約3割を洗浄工程が占めるともいわれています。
- ウェット洗浄とは:液体(主に薬液や純水)を用いてウエハ表面の汚染物質を除去する方法です。半導体洗浄の約99%を占める、主流の洗浄技術です。
- ドライ洗浄とは:ドライ洗浄は気体やエネルギーを用いてウエハ表面の汚染物質を除去する洗浄方法です。ウェット洗浄が主流である一方で、半導体の微細化が進むにつれて、精密性や薬液残渣のなさといった利点からドライ洗浄の重要性は増しています。
ウエハの洗浄
半導体の重要性が増す中で、前工程装置は世界的に成長が続いています。
https://optronics-media.com/news/20250414/99245/
特に中国は米中対立もあり、大幅な投資増加が続いています。今後も先端技術を駆使した半導体の需要増加と従来技術による成熟プロセスともにその重要性は増加するとみられています。
今回はウエハの洗浄についての解説となります。
半導体の前工程とは
半導体の前工程とは、シリコンウェハ上にトランジスタや配線などの微細な回路を形成する一連のプロセスのことです。ウェハを素材として、集積回路を作り込んでいく、半導体製造の最も重要な部分と言えます。非常に多くの精密な工程を経て、最終的な半導体チップの機能が決まります。
主な前工程は以下の通りです。
ウェハ準備
シリコンインゴットの製造: 高純度のシリコンを溶解し、種結晶を用いて単結晶のシリコンインゴットを育成します。
- スライス: インゴットを薄い円盤状(ウェハ)にスライスします。
- 研磨: ウェハ表面を平坦かつ滑らかに研磨します。
- 洗浄: ウェハ表面の微細な異物や汚れを徹底的に除去します。
成膜
ウェハ表面に、酸化膜、窒化膜、金属膜など、様々な薄膜を形成します。
- 成膜方法には、CVD(化学気相成長法)、スパッタリング(物理気相成長法)、ALD(原子層堆積法)などがあります。
フォトリソグラフィ
ウェハ表面に感光材(フォトレジスト)を塗布します。
- 回路パターンが描かれたマスク(フォトマスク)を通して紫外線を照射し、レジストにパターンを焼き付けます。
- 現像液で不要なレジストを除去し、ウェハ上に回路パターンを形成します。
エッチング
フォトリソグラフィでパターン形成されたレジストをマスクとして、露出した成膜を除去し、ウェハに回路パターンを転写します。
- エッチングには、液体を用いるウェットエッチングと、プラズマを用いるドライエッチングがあります。
不純物導入(ドーピング)
半導体特性を持たせるために、リンやボロンなどの不純物をウェハ中に注入します。
- イオン注入法などが用いられます。
平坦化(CMP: Chemical Mechanical Polishing)
表面の凹凸をなくし、平坦にするための処理です。
- 化学的な腐食と механическая研磨を同時に行います。
配線形成(メタライゼーション)
形成されたトランジスタなどの素子間を金属配線で接続します。
- スパッタリングなどで金属膜を形成し、フォトリソグラフィとエッチングで配線パターンを作ります。
これらの工程を何度も繰り返し行うことで、複雑な集積回路がウェハ上に形成されます。前工程は、半導体の性能や品質を大きく左右する、非常に重要なプロセスです。
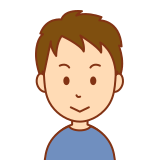
前工程は、細な回路を形成する一連のプロセスのことで、半導体の性能や品質を大きく左右する、非常に重要なプロセスです。
シリコンウエハの洗浄
半導体前工程におけるウエハの洗浄とは、シリコンウエハ上に形成される微細な回路パターンに悪影響を及ぼす可能性のある不要な物質(汚染物質)をウエハ表面から除去する非常に重要な工程です。
具体的には、以下のような目的で洗浄が行われます。
- パーティクル(微細なゴミ、チリ)の除去: 空気中や製造装置から付着するナノメートルサイズの微細なゴミは、回路の微細化が進むにつれて不良の原因となるリスクが高まっています。
- 金属不純物の除去: ウエハ搬送装置や薬液に含まれる金属成分は、ウエハ表面に付着すると積層不良などを引き起こす可能性があります。
- 有機物の除去: 人の皮脂や垢、製造工程で使用する薬液に含まれる有機物は、 後続の工程での化学反応を阻害する可能性があります。
- 自然酸化膜の除去: ウエハが大気に触れることで形成される酸化膜は、不純物を含む場合があるため除去されます。
- 前工程で使用した薬液や反応生成物の除去: 各工程で使用した薬液や、その反応によって生成された不要な物質を次の工程へ持ち込まないように除去します。
半導体製造の前工程では、各工程の前後に洗浄が行われることが多く、その重要性から全工程の約3割を洗浄工程が占めるとも言われています。
洗浄の種類
洗浄方法には、液体や気体の化学薬品を用いるウェット洗浄と、プラズマ化したガスやUVオゾンなどを用いるドライ洗浄があります。
またウエハの処理枚数や求められる清浄度によって、複数のウエハをまとめて処理するバッチ式や、一枚ずつ精密に処理する枚葉式などの装置が使い分けられています。
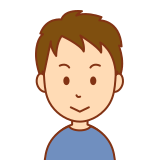
シリコンウエハの洗浄はパーティクル、金属不純物や有機物などの除去のために行われます。全行程の約3割を洗浄工程が占めるともいわれています。
ウェット洗浄とは何か
ウェット洗浄とは、半導体前工程におけるウエハの洗浄方法の一つで、液体(主に薬液や純水)を用いてウエハ表面の汚染物質を除去する方法です。半導体洗浄の約99%を占める、主流の洗浄技術です。
洗浄方法
- 浸漬洗浄: ウエハを薬液や純水の槽に浸して洗浄します。複数の槽を順番に移動させるバッチ式で行われることが多いです。
- スプレー洗浄: ウエハを回転させながら、ノズルから薬液や純水を吹き付けて洗浄します。枚葉式と呼ばれる一枚ずつ処理する方法で、精密な洗浄が可能です。
- 超音波洗浄: 薬液や純水の槽内で超音波を発生させ、その振動によってウエハ表面のパーティクルなどを剥離・除去します。
- メガソニック洗浄: 超音波よりも高い周波数(メガヘルツ帯)の振動を利用し、より微細なパーティクルを除去するのに有効です。
ウェット洗浄で、使用される化学薬品
- 酸: 金属不純物や自然酸化膜の除去
- アルカリ: 有機物やパーティクルの除去
- 過酸化水素水: 有機物や金属不純物の除去
- フッ酸: シリコン酸化膜の除去
- 界面活性剤: パーティクルの剥離
ウェット洗浄のメリット
- 高い洗浄能力: 微細なパーティクル、金属汚染、有機物など、様々な汚染物質を効果的に除去できます。
- 多様な洗浄方法と薬液の組み合わせ: ウエハの状態や汚染物質に合わせて最適な洗浄プロセスを設計できます。
ウェット洗浄のデメリット
- 薬液や純水の使用量が多い: 環境負荷やコストの面で課題となることがあります。
- 乾燥工程が必要: 洗浄後のウエハを乾燥させる工程が不可欠であり、乾燥不良は新たな汚染の原因となる可能性があります。
- 微細な構造へのダメージリスク: 薬液の表面張力などが、微細な回路パターンに影響を与える可能性があります。
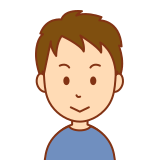
ウェット洗浄とは液体(主に薬液や純水)を用いてウエハ表面の汚染物質を除去する方法です。半導体洗浄の約99%を占める、主流の洗浄技術です。
ドライ洗浄とは何か
ドライ洗浄は、液体(水や薬液)を使用せずに、気体やエネルギーを用いてウエハ表面の汚染物質を除去する洗浄方法です。
ウェット洗浄が主流である一方で、ドライ洗浄は以下のような利点から特定の工程で利用されています。
ドライ洗浄の主な利点
- 薬液残留のリスクがない: 液体を使用しないため、ウエハ表面に薬液が残留する心配がありません。
- 精密な洗浄が可能: ガスやエネルギーを制御することで、より精密な洗浄が可能です。
- 表面張力の影響を受けにくい: 微細な構造を持つウエハに対して、表面張力によるダメージを与えにくいです。
- 乾燥工程が不要: 液体を使用しないため、洗浄後の乾燥工程が不要となり、時間とコストを削減できます。
ドライ洗浄の主な欠点
- 化学反応が遅い場合がある: 汚染物質によっては、除去に時間がかかることがあります。
- コストが高い: 装置やプロセスによっては、ウェット洗浄よりもコストが高くなる場合があります。
- 工程が複雑になる場合がある: 複数のドライ洗浄技術を組み合わせる必要がある場合があります。
- 対応できる汚染物質が限定的な場合がある: ウェット洗浄に比べて、広範囲の汚染物質に対応できないことがあります。
主なドライ洗浄の種類と原理
- プラズマ洗浄:
- 原理: 真空中でガスに高周波などのエネルギーを加えてプラズマ状態にし、発生した活性種(ラジカルやイオン)をウエハ表面に反応させて汚染物質を除去します。
- 特徴: 微細なパーティクルや有機物の除去に効果的です。エッチングにも応用されます。
- UVオゾン洗浄:
- 原理: 紫外線を照射することで酸素からオゾンを生成し、このオゾンと紫外線が有機物を酸化分解して除去します。
- 特徴: 低温で処理が可能で、有機物の除去に有効です。
- スパッタリング洗浄 (リバーススパッタリング):
- 原理: アルゴンなどの希ガスをイオン化し、ウエハ表面に衝突させて汚染物質を物理的に除去します。
- 特徴: 主に金属汚染の除去や自然酸化膜の除去に用いられます。
- CO2スノージェット洗浄:
- 原理: 液化炭酸ガスをノズルから噴射し、急激な膨張によって微細なドライアイス粒子(CO2スノー)を生成します。この粒子をウエハ表面に衝突させて汚染物質を物理的に除去します。
- 特徴: 薬液を使用せず、パーティクルや有機物の除去に有効です。
- エキシマレーザー洗浄:
- 原理: エキシマレーザーの紫外線をウエハ表面に照射し、汚染物質を蒸発・分解して除去します。
- 特徴: 特定の汚染物質をピンポイントで除去するのに適しています。
半導体製造におけるドライ洗浄の適用例
- 自然酸化膜の除去: 成膜前に、シリコンウエハ表面の自然酸化膜を除去し、下地との密着性を向上させます。
- 有機汚染物の除去: フォトリソグラフィ工程後のレジスト残渣や、プロセス中に付着した有機物を除去します。
- 金属汚染の除去: 金属配線形成前後の金属不純物を除去し、デバイスの信頼性を高めます。
- 微細パーティクルの除去: ウェット洗浄が困難な微細なパーティクルを除去します。
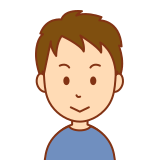
ドライ洗浄は気体やエネルギーを用いてウエハ表面の汚染物質を除去する洗浄方法です。ウェット洗浄が主流である一方で、半導体の微細化が進むにつれて、精密性や薬液残渣のなさといった利点からドライ洗浄の重要性は増しており、より効率的で環境負荷の少ないドライ洗浄技術の開発が進められています。
バッチ式と枚葉式の違い
バッチ式と枚葉式は、半導体製造におけるウエハ処理(洗浄、成膜、エッチングなど)を行う装置の、ウエハの処理方法による分類です。それぞれの特徴は以下の通りです。
バッチ式 (Batch Type)
- 処理方法: 複数のウエハをまとめて、同時に処理します。
- 構造: 薬液槽や処理チャンバーが複数あり、ウエハを収めたキャリアを順に移動させる多槽式や、一つの槽で薬液を入れ替えながら処理する単槽式があります。
- メリット:
- 高いスループット (処理能力): 一度に多数のウエハを処理できるため、大量生産に適しています。
- 低いウエハあたりの処理コスト: 多数のウエハをまとめて処理するため、個々のウエハにかかるコストを抑えられます。
- シンプルな装置構成 (単槽式の場合): 枚葉式に比べて構造がシンプルな場合があります。
- デメリット:
- 品質の均一性に課題: 全てのウエハに対して均一な処理を行うのが難しい場合があります。
- コンタミネーションのリスク: 処理槽内でパーティクルなどが蓄積しやすく、コンタミネーションのリスクが高まる可能性があります。
- 柔軟性に欠ける: ウエハ一枚ごとに処理条件を細かく変えることは困難です。
- 装置が大型化する傾向 (多槽式の場合): 多数の処理槽が必要となるため、設置面積が大きくなることがあります。
枚葉式 (Single Wafer Type)
枚葉式 (Single Wafer Type):
- 処理方法: ウエハを一枚ずつ個別に処理します。
- 構造: ウエハを回転させながら、ノズルから薬液やガスなどを供給したり、エネルギーを照射したりして処理を行います。
- メリット:
- 高い処理精度と均一性: ウエハ一枚ごとに最適な処理条件を設定できるため、高品質な処理が可能です。
- 低いコンタミネーションリスク: ウエハを個別に処理するため、処理槽からのコンタミの影響を低減できます。
- 高い柔軟性: ウエハの種類や工程に合わせて、処理条件を細かく調整できます。
- 省スペース: バッチ式に比べて装置がコンパクトな傾向があります。
- 薬液使用量の削減: 必要な量の薬液をウエハ一枚に供給するため、バッチ式に比べて薬液の使用量を抑えられる場合があります。
- デメリット:
- 低いスループット: 一度に一枚しか処理できないため、大量生産には不向きです。
- 高いウエハあたりの処理コスト: 一枚ずつ処理するため、個々のウエハにかかるコストが高くなる傾向があります。
- 複雑な装置構成: 高度な制御機構や搬送機構が必要となるため、装置構成が複雑になる場合があります。
まとめ
特徴 | バッチ式 | 枚葉式 |
---|---|---|
処理枚数 | 複数枚同時 | 1枚ずつ |
スループット | 高い | 低い |
処理精度 | 比較的低い | 高い |
均一性 | 比較的低い | 高い |
コンタミリスク | 比較的高い | 低い |
柔軟性 | 低い | 高い |
コスト (ウエハあたり) | 低い | 高い |
装置サイズ | 大型化する傾向 (多槽式) | コンパクトな傾向 |
主な用途 | 大量生産、コスト重視 | 多品種少量生産、高精度・高品質重視 |
ウエハの洗浄装置メーカー
日本国内外には、多数のウエハ洗浄装置メーカーが存在します。主なメーカーとしては、以下のような企業が挙げられます。
主要なウエハ洗浄装置メーカー
株式会社ゼビオス (日本): 洗浄装置を含む半導体製造装置を提供しています。
株式会社SCREENセミコンダクターソリューションズ (日本): 枚葉式、バッチ式、ブラシ式など、幅広い洗浄装置を提供しており、世界シェアも高い企業です。
東京エレクトロン株式会社 (日本): 成膜装置やエッチング装置など、半導体製造装置全般を手掛けていますが、洗浄装置も提供しています。
芝浦メカトロニクス株式会社 (日本): 枚葉式ウエハ洗浄装置、特に研磨後洗浄装置で高いシェアを持っています。枚葉式フォトマスク洗浄装置も手掛けています。
株式会社ジェイ・イー・ティ (日本): カスタマイズ性に優れた洗浄装置を提供しており、世界でもトップクラスのシェアと実力を持つメーカーです。
株式会社ダン科学 (日本): 半導体関連装置メーカーとして、洗浄装置も提供しています。
HUGパワー株式会社 (日本): 蒸気2流体洗浄装置や高濃度オゾン水を利用した洗浄装置など、独自の技術を持つメーカーです。
コメント