この記事で分かること
- 支援を行う技術:同社が高いシェアをもつ半導体工場向け搬送装置に関する保守点検などの技術支援を行としています。
- 半導体向け搬送装置に必要な特性:超高クリーン度、99.999%以上の高稼働率、精密な位置決めと振動抑制が必須です。さらに、高速・高スループット、製造管理システムとの高度な連携、そして将来の拡張性・安全性が求められます。
- 高稼働率の実現法:高耐久性部品の使用、システムの冗長化、そしてセンサーによる状態監視と予知保全で故障を未然に防いでいます。
村田機械の技術支援用新拠点
村田機械はドイツに技術支援の新拠点を設けています。
https://www.nikkei.com/article/DGXZQOUF144VV0U5A510C2000000/
具体的には、MURATA MACHINERY EUROPE GMBH がドイツのWillichにあり、ここが欧州地域の拠点として半導体向け搬送装置などの技術支援を行っていると考えられます。
半導体向け搬送装置に求められるものは
半導体製造における搬送システムには、極めて高いレベルの要求事項が課せられます。これは、半導体そのものが非常にデリケートな製品であり、製造工程が複雑かつ精密であるためです。主な要求事項は以下の通りです。
1. 超高クリーン度
- 発塵の徹底的な抑制: 半導体は微細なゴミやチリが製品品質に致命的な影響を与えるため、搬送装置自体からの発塵を極限まで抑える必要があります。リニアモーター駆動や非接触搬送技術などが採用されます。
- クリーンルーム環境への適合: クリーンルームのクラスに応じた清浄度を維持しながら、搬送システムが稼働できることが必須です。
2. 高信頼性と高稼働率(ノンストップ稼働)
- 24時間365日稼働: 半導体工場は基本的に止まることなく稼働するため、搬送システムもそれに合わせて高い稼働率が求められます。
- 故障時の対応力: 万が一の故障時にも、迅速な復旧や代替ルートでの搬送が可能であること、また故障自体が発生しにくい堅牢な設計が重要です。システムの冗長化も不可欠です。
- 安定した電力供給: 停電時にもシステムが停止しないよう、無停電電源装置(UPS)や非常用電源との連携も重要です。
3. 高精度と高安定性
- 正確な位置決め: FOUP(半導体ウェハを収納する容器)などのキャリアを、製造装置のロードポートへ寸分の狂いなく搬送し、正確に位置決めする能力が求められます。
- 振動抑制: 微細なウェハが破損しないよう、搬送中の振動を極力抑える技術が必要です。
4. 高速性・高スループット
- 生産能力への貢献: 生産量が増加するにつれて、より高速で大量のウェハやFOUPを搬送できる能力が求められます。
- ラインのボトルネック回避: 搬送がボトルネックとなって製造ライン全体の生産効率が落ちないよう、工程間の時間に合わせて柔軟な搬送速度の調整や、最適な経路選択が必要です。
5. 高度な制御・連携
- 製造管理システム(MES)との連携: 工場全体の生産計画や進捗状況と連携し、最適なタイミングで必要な場所に搬送を行うための高度な制御システム(MCSなど)が必要です。
- 装置間のインターフェース: 各製造装置のロードポートやストッカーとのシームレスな連携を可能にするための標準化されたインターフェース(SEMI規格など)への対応が不可欠です。
- リアルタイムな情報共有: 各FOUPの現在位置や状態、製造装置の稼働状況などをリアルタイムで把握し、適切な指示を出すための情報共有システムが必要です。
- フリートマネジメント: 複数の搬送装置(OHT、AGVなど)が効率よく連携し、衝突することなく稼働するための全体最適化が求められます。
6. 柔軟性と拡張性
- レイアウト変更への対応: 製造ラインの変更や増設に対応できるよう、柔軟なシステム構成や拡張性が必要です。
- 将来的な技術への対応: ウェハサイズの大型化や、新たな製造プロセスへの対応など、将来の技術進化に対応できる設計が求められます。
7. 安全性
- 人との共存: 無人搬送車などが稼働するエリアでの作業者の安全を確保するため、衝突防止センサーや安全停止機能などの安全対策が重要です。
これらの要求事項を満たすことで、半導体搬送システムは、半導体製造の効率化、品質向上、そして安定稼働に不可欠な役割を果たしています。
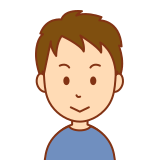
半導体搬送システムには、超高クリーン度、99.999%以上の高稼働率、精密な位置決めと振動抑制が必須です。さらに、高速・高スループット、製造管理システムとの高度な連携、そして将来の拡張性・安全性が求められます。
村田機械の半導体向け搬送装置の特徴は
村田機械は、半導体製造工場におけるクリーンFA(ファクトリーオートメーション)分野において、世界でも数社しかない搬送システムインテグレーターの1社であり、業界トップクラスのマーケットシェアを誇っています。同社の半導体向け搬送装置の主な種類と特徴は以下の通りです。
1. 主要な搬送装置の種類
- OHT(Overhead Hoist Transport / 天井走行式無人搬送車):
- 半導体工場における主力搬送システム。
- 天井に設置された軌道を走行し、ホイスト機構で製造装置のロードポートに直接アクセスし、FOUP(半導体ウエハを収納する密閉容器)などを搬送します。
- 300mmウェハ工場以降で広く普及しており、工程内搬送だけでなく、工程間や工場間搬送にも利用されています。
- 高速搬送が可能でありながら、振動を抑える制震技術が用いられています。
- 接触給電リニアモーター走行により、発塵を抑えクリーンな環境を維持します。
- HTC(High-Throughput Conveyor / 高速コンベア):
- FOUPの大量搬送に対応するコンベアシステムです。
- ユニットの組み合わせによりレイアウトの自由度が高く、OHTやVertical Conveyorにも接続可能です。
- すべてのキャリアの位置を常時監視することで、キャリアロスを発生させません。
- AGV(Automated Guided Vehicle / 無人搬送車):
- 高精度なナビゲーションシステムにより、複雑なルートをフレキシブルに走行し、製造装置などへキャリアを搬送します。
2. 保管・バッファ装置の種類
- キャリア保管ストッカー: クリーンルーム内でのFOUPなどの保管に使用されます。
- ベアウエハストッカー CDWX:
- FOUPからウェハを取り出し、専用のケース(セル)で高密度に保管するシステムです。
- ウェハの間隔をFOUPと比較して大幅に削減し、高密度保管を実現します。
- 高クリーン度を保ちながら、メンテナンス性にも優れています。
3. 特徴と強み
- 高信頼性と稼働率: 半導体製造は24時間365日稼働が求められるため、同社の搬送システムは「止まらないシステム」として、99.999%の稼働率を実現する可用性に特化したノンストップシステムを提供しています。
- クリーンルーム対応: 微細なチリやホコリも許されないクリーンルーム環境に対応するため、発塵を極限まで抑える設計や、接触給電リニアモーター走行などの技術を採用しています。
- 高度な制御技術: 大規模な工場全体の搬送システムを統括制御するシステム(MCS:Manufacturing Control System)を提供しており、さらに工場間の連携を可能にするMDS(Manufacturing Data System)も提供しています。これにより、最適な経路探索や衝突回避、工程間の同期など、高度な自動制御を実現しています。
- トータルソリューション: 開発設計から製造、組立、販売、据付工事、導入指導、保守、メンテナンスまで、一貫したシステムを提供し、顧客の多様なニーズに対応しています。
- 豊富な実績: 世界有数の半導体メーカーをクライアントに持ち、長年の経験と実績を積み重ねています。
村田機械の半導体向け搬送装置は、半導体製造の効率化、品質向上、そして安定稼働に不可欠な役割を担っており、世界の半導体産業を支える重要な技術となっています。
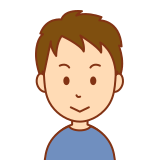
村田機械の半導体向け搬送装置は、クリーンルーム対応のOHT(天井走行式無人搬送車)や高速コンベアなどを主力とし、発塵を抑え高稼働率99.999%を実現。高度な制御技術で工場全体の自動搬送を支え、世界中の半導体製造に貢献しています。
どうやって高稼働率を実現しているのか
半導体搬送システムにおける「99.999%」という極めて高い稼働率を実現するためには、多岐にわたる技術と対策が複合的に組み合わされています。村田機械も同様のアプローチをとっていると考えられます。主な要素は以下の通りです。
1. 堅牢な設計と高品質な部品
- 高耐久性の追求: 長期間の連続稼働に耐えうる堅牢な機械設計と、高耐久性・高信頼性の部品(モーター、ベアリング、センサーなど)を選定します。
- 発塵抑制とクリーン性: 部品自体の摩耗による発塵を抑える設計(非接触駆動、特殊素材の使用など)や、クリーンルーム環境に適合した材料の使用が徹底されます。
2. 冗長性の確保
- システム冗長化: 主要な制御系や駆動系、通信系において、万が一の故障に備えて予備のシステムや経路を確保します。例えば、OHTの場合、複数の軌道や車両を用意し、一部が停止しても別の経路で搬送を継続できるようにします。
- 電源の二重化/UPS: 停電時にもシステムが停止しないよう、電源を二重化したり、無停電電源装置(UPS)を導入したりします。
3. 予防保全と予知保全
- 定期的なメンテナンス: 計画に基づいた定期的な点検や部品交換を実施し、故障を未然に防ぎます。
- 状態監視と予知保全: センサーやデータ分析により、装置の振動、温度、電流などの稼働データをリアルタイムで監視します。異常の兆候を早期に検知し、故障が発生する前に部品交換や調整を行うことで、計画外の停止を防ぎます。AIや機械学習を活用した予知保全も進められています。
- 部品寿命管理: 部品ごとの設計寿命や交換推奨時期を管理し、計画的に交換を進めます。
4. 高度な制御システムとフリートマネジメント
- 最適経路探索と衝突回避: 複数台の搬送装置が効率よく稼働できるよう、リアルタイムで最適な搬送経路を計算し、衝突を回避する高度な制御アルゴリズムが導入されます。
- 負荷分散と渋滞回避: 特定の区間に搬送が集中することを防ぎ、全体としてスムーズな流れを維持するための制御が行われます。
- 自動復旧機能: 軽微なエラーや一時的な停止が発生した場合でも、自動的に復旧し、搬送を再開する機能が搭載されています。
- 緊急時の自動対応: 予期せぬ事態が発生した場合でも、ウェハの安全を確保しながら、システムが自動的に停止したり、安全な場所へ退避したりする機能があります。
5. 迅速なトラブルシューティングとサービス体制
- リモート監視・診断: 遠隔地からシステムの稼働状況を監視し、異常が発生した際には迅速に診断・対応できる体制を構築しています。
- オンサイトサービス: 万が一の故障発生時には、専門のエンジニアが迅速に現場に駆けつけ、復旧作業を行います。
- 部品供給体制: 交換部品を迅速に供給できる体制を整備しています。
6. 人為的ミスの排除と自動化
- 徹底した自動化: 人の手による作業を極力減らし、自動化することで人為的なミスや作業遅延を排除します。
- エラープルーフ設計: 誤操作を物理的・システム的に防ぐ設計を取り入れます。
これらの技術と体制を組み合わせることで、半導体搬送システムは「止まらない」インフラとして、半導体工場の高生産性を支えています。
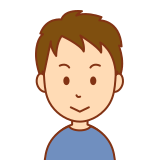
高稼働率は、高耐久性部品の使用、システムの冗長化、そしてセンサーによる状態監視と予知保全で故障を未然に防ぎます。また、高度な制御システムが最適な搬送と自動復旧を担い、迅速なサービス体制も加えて実現されます。
コメント