この記事で分かること
・半導体前工程とは:前工程は、シリコンウェハー上に回路を形成する工程で、半導体の性能を決定づける最も重要なプロセスであり、大規模なクリーンルームや最先端の装置が必要になります。
・なぜ、投資額の増加が続くのか:半導体の需要増 + 技術革新 + 地政学リスク + 設備の高額化が主な理由で投資額が増加しています。
・日本メーカの前工程装置の代表例:成膜装置の東京エレクトロン、ウエハ洗浄のSCREEN、CMPの荏原製作所、検査装置の日立ハイテクやアドバンテストなどが代表的です。
半導体前工程向け製造装置への投資額増加
2025年3月27日付けのEE Times Japanの記事によれば、SEMIの予測で、2025年の半導体前工程向け製造装置への投資額が前年比2%増の1100億米ドルに達し、これで6年連続の成長となる見込みです。
AI・HPC向け半導体需要の急増など様々理由によって、設備投資伸びを見せています。
半導体の前処理工程とは何か
半導体の前工程(フロントエンドプロセス)は、シリコンウェハー上に回路を形成する工程で、半導体製造の中でも特に高度な技術と設備が必要な部分です。前工程は主に以下のステップで構成されます。
1. ウェハー製造
- シリコンインゴットの成長(CZ法やFZ法)
- ウェハーのスライス・研磨(薄く切断し、平坦化)
2. 洗浄
3. 成膜(薄膜形成)
- 絶縁膜や導電膜を形成するためのプロセス。
- 代表的な手法:
- CVD(化学気相成長)
- PVD(物理気相成長)
- 酸化(熱酸化):SiO₂膜の形成
4. フォトリソグラフィ(露光・パターニング)
- 回路パターンを形成する工程。
- ステップ:
- フォトレジスト塗布(感光性樹脂をウェハー上に塗布)
- 露光(紫外線やEUVを使って回路パターンを転写)
- 現像(不要なフォトレジストを除去)
5. エッチング
- 露光された不要な部分を削る工程。
- 代表的な手法:
- ドライエッチング(プラズマエッチング)
- ウェットエッチング(化学薬品によるエッチング)
6. イオン注入(ドーピング)
- 半導体の電気特性を制御するため、不純物(ボロン、リンなど)を埋め込む工程。
7. CMP(化学機械研磨)
- 表面を均一に平坦化し、次の工程での精度を向上させる。
8. 多層配線形成
- 金属(銅、アルミなど)を使って回路を形成。
- スパッタリングやめっきで配線を作り、CMPで研磨。
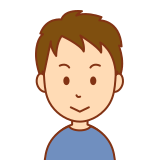
前工程は、シリコンウェハー上に回路を形成する工程で、半導体の性能を決定づける最も重要なプロセスであり、大規模なクリーンルームや最先端の装置が必要になります。
前工程の製造装置にはどんなものがあるのか
半導体の前工程(フロントエンドプロセス)では、各製造ステップごとに以下のような専用の装置が使われます。
1. ウェハー製造関連
- シリコン単結晶引き上げ装置(CZ法、FZ法)
→ シリコンインゴットを成長させる装置 - ウェハー研磨装置(ラッピング、ポリッシング)
→ スライスしたウェハーの表面を平坦化
2. ウェハー洗浄装置
- バッチ式洗浄装置
→ 化学薬品や超純水を使って複数枚のウェハーを同時に洗浄 - シングルウェハー洗浄装置
→ 1枚ずつ高精度に洗浄(先端半導体向け)
3. 成膜装置(薄膜形成)
- CVD(化学気相成長)装置
→ 絶縁膜や導電膜を成膜(SiO₂, Si₃N₄, 金属膜など) - PVD(物理気相成長)装置(スパッタリング装置)
→ 金属膜(Cu, Alなど)の成膜 - 熱酸化炉
→ シリコン基板を酸素や水蒸気で加熱し、SiO₂膜を形成
4. フォトリソグラフィ(露光・パターニング)
- コーターデベロッパー(塗布・現像装置)
→ フォトレジストをウェハーに均一に塗布し、現像も行う - 露光装置(ステッパー / スキャナー)
→ 紫外線やEUV光を使い、回路パターンを転写
→ ASML(オランダ)がEUV露光装置で世界シェア独占
5. エッチング装置
- ドライエッチング装置(プラズマエッチング)
→ 精密な加工を行うための主流装置(Si, SiO₂, 金属膜のエッチング) - ウェットエッチング装置
→ 化学薬品を使って特定の材料を除去(微細加工には不向き)
6. イオン注入装置(ドーピング)
- イオン注入装置
→ 高速のイオンビームでウェハーに不純物を注入し、電気特性を制御
7. CMP(化学機械研磨)装置
- CMP装置(Chemical Mechanical Polishing)
→ 表面を平坦化し、配線工程の精度を確保
8. 多層配線形成
- メッキ装置(電解 / 無電解)
→ 銅配線形成のためのCuメッキ - スパッタリング装置(PVDと同様)
→ 金属膜を成膜し、配線層を形成 - エッチバック / 研磨装置(CMP)
→ 過剰な金属を削り、平坦化
9. 検査・測定装置
- 膜厚測定装置
→ 成膜された薄膜の厚さを測定 - CD-SEM(Critical Dimension-SEM)
→ ナノスケールの回路寸法を測定する電子顕微鏡 - パーティクル測定装置
→ 微粒子汚染を検出し、不良を防ぐ
主要装置メーカー
- ASML(オランダ):EUV露光装置
- 東京エレクトロン(TEL):成膜、エッチング、洗浄、露光など幅広い装置
- アプライドマテリアルズ(AMAT・米国):成膜、エッチング、CMP装置
- ラムリサーチ(Lam Research・米国):エッチング装置
- KLA(米国):検査・測定装置
- SCREEN(日本):洗浄装置
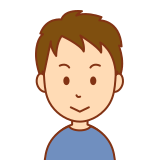
半導体の前工程には、多くの工程があり、それぞれの工程で、複数の専用装置が使用されています。
なぜ、製造装置への投資が増加しているのか
半導体の前工程製造装置への投資が増加している理由は、以下のような要因が影響しています。
1. AI・HPC向け半導体需要の急増
- AI(人工知能)やHPC(ハイパフォーマンスコンピューティング)の普及により、高性能チップ(GPU・TPU・専用AIプロセッサなど)の需要が拡大。
- これらのチップは最先端の微細加工技術(3nm、2nmなど)を必要とし、高度な製造装置への投資が不可欠。
2. 微細化の進行とEUV装置の需要増
- 2nm、1.4nmプロセスに向けた微細化が進み、従来の**DUV(深紫外線)**では対応できないため、EUV(極端紫外線)露光装置の導入が必須に。
- ASMLのEUV装置は非常に高価(1台数千億円規模)で、導入が増えると投資額も大きくなる。
3. ロジック・メモリ市場の回復
- 2023年は半導体不況だったが、2024年から需要が回復し、2025年は本格的な投資フェーズに移行。
- メモリ(DRAM、NAND)の設備投資が増加し、特に次世代DRAM(HBM、DDR5)向けの製造装置が必要。
- TSMC、Samsung、Intelなどのファウンドリも最先端プロセス向けに積極投資。
4. 地政学リスクによる国内生産回帰(CHIPS法など)
- 米国・EU・日本が半導体サプライチェーンの強化を進めており、国内生産回帰のための補助金が増加。
- 例:
- 米国CHIPS法(520億ドルの補助金)
- EU CHIPS Act(430億ユーロの投資計画)
- 日本もTSMC熊本工場に助成金
- 各国で新工場が建設されることで、製造装置の需要が増加。
5. 自動車・産業用半導体の需要増
- EV(電気自動車)やADAS(先進運転支援システム)の普及により、高性能なパワー半導体や車載半導体の需要が拡大。
- これに伴い、SiC(炭化ケイ素)やGaN(窒化ガリウム)の製造装置の導入が増えている。
6. 3Dパッケージング技術の進化
- TSMCのCoWoS、IntelのFoveros、SamsungのX-Cube など、先端パッケージ技術の発展により、ウェハーレベルでの積層技術が必要。
- TSV(シリコン貫通ビア)や先端リソグラフィなどの装置が必要になり、投資が増加。
7. 製造装置の価格上昇
・半導体製造装置の高度化により、1台あたりの価格が上昇。
例:ASMLのEUV装置は1台4000億円超、高価な装置が増えることで、投資額全体が増加。
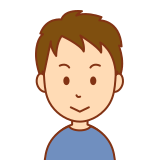
半導体の需要増 + 技術革新 + 地政学リスク + 設備の高額化 が重なり、製造装置への投資が増加しています。
コメント