この記事で分かること
- 窒化物の特徴:窒化物は、純粋な金属より緻密で安定した構造を持つため、銅の拡散をより効果的に防ぎます。また、高い熱的・化学的安定性や密着性、エレクトロマイグレーション耐性向上効果があります。
- 緻密な構造を持つ理由:金属原子と窒素原子が共有結合性の強い結合を形成し、窒素原子が金属格子の隙間に入り込むことで、より強く密な結晶構造を形成します。これにより、結合エネルギーが増加し、純粋な金属より熱的・化学的に安定します。
- タンタル単体と窒化物の使い分け:タンタル単体(Ta)は低抵抗で銅との密着性が良く、主に下地やシード層との接着に利用されます。一方、窒化タンタル(TaN)は優れた銅拡散バリア性と熱安定性を持つため、主要な拡散防止層として使われます。多くの場合、両者を積層し、それぞれの利点を活かします。
半導体の重要性が増す中で、前工程装置は世界的に成長が続いています。
https://optronics-media.com/news/20250414/99245/
特に中国は米中対立もあり、大幅な投資増加が続いています。今後も先端技術を駆使した半導体の需要増加と従来技術による成熟プロセスともにその重要性は増加するとみられています。
今回はバリアメタルに使用される窒化物についての解説となります。
半導体の前工程とは
半導体の前工程とは、シリコンウェハ上にトランジスタや配線などの微細な回路を形成する一連のプロセスのことです。ウェハを素材として、集積回路を作り込んでいく、半導体製造の最も重要な部分と言えます。非常に多くの精密な工程を経て、最終的な半導体チップの機能が決まります。
主な前工程は以下の通りです。
ウェハ準備
シリコンインゴットの製造: 高純度のシリコンを溶解し、種結晶を用いて単結晶のシリコンインゴットを育成します。
- スライス: インゴットを薄い円盤状(ウェハ)にスライスします。
- 研磨: ウェハ表面を平坦かつ滑らかに研磨します。
- 洗浄: ウェハ表面の微細な異物や汚れを徹底的に除去します。
成膜
ウェハ表面に、酸化膜、窒化膜、金属膜など、様々な薄膜を形成します。
- 成膜方法には、CVD(化学気相成長法)、スパッタリング(物理気相成長法)、ALD(原子層堆積法)などがあります。
フォトリソグラフィ
ウェハ表面に感光材(フォトレジスト)を塗布します。
- 回路パターンが描かれたマスク(フォトマスク)を通して紫外線を照射し、レジストにパターンを焼き付けます。
- 現像液で不要なレジストを除去し、ウェハ上に回路パターンを形成します。
エッチング
フォトリソグラフィでパターン形成されたレジストをマスクとして、露出した成膜を除去し、ウェハに回路パターンを転写します。
- エッチングには、液体を用いるウェットエッチングと、プラズマを用いるドライエッチングがあります。
不純物導入(ドーピング)
半導体特性を持たせるために、リンやボロンなどの不純物をウェハ中に注入します。
- イオン注入法などが用いられます。
平坦化(CMP: Chemical Mechanical Polishing)
表面の凹凸をなくし、平坦にするための処理です。
- 化学的な腐食と 研磨を同時に行います。
配線形成(メタライゼーション)
形成されたトランジスタなどの素子間を金属配線で接続します。
- スパッタリングなどで金属膜を形成し、フォトリソグラフィとエッチングで配線パターンを作ります。
これらの工程を何度も繰り返し行うことで、複雑な集積回路がウェハ上に形成されます。前工程は、半導体の性能や品質を大きく左右する、非常に重要なプロセスです。
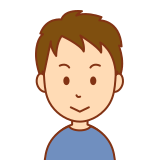
前工程は、微細な回路を形成する一連のプロセスのことで、半導体の性能や品質を大きく左右する、非常に重要なプロセスです。
バリアメタルにはどんな材料が使用されるのか
バリアメタルは、半導体配線において、銅(Cu)などの金属が周囲のシリコンや絶縁膜へ拡散するのを防ぐ薄い層です。配線材料と他の層との密着性を高め、電気特性の劣化や信頼性低下を防ぐ重要な役割を担います。
現在、主に用いられているバリアメタル材料は以下の通りです。
チタン(Ti)/窒化チタン(TiN): かつてアルミ(Al)配線で広く使われていましたが、銅配線でもバリアメタルや接着層として用いられることがあります。特に、TiNは銅との密着性やバリア性に優れる場合があります。
タンタル(Ta)/窒化タンタル(TaN): 銅配線のバリアメタルとして最も広く用いられています。TaNはTaに比べて拡散防止能力が高く、Taと組み合わせて使用されることが多いです。
窒化物を使う理由は何か
半導体プロセスにおいて、バリアメタルとして純粋な金属(タンタルやチタン)ではなく、その窒化物(窒化タンタル: TaN、窒化チタン: TiN)を使用する主な理由は、以下の優れた特性があるためです。
銅拡散防止能力の向上
- 窒化物は、純粋な金属と比較して、原子の構造がより緻密で安定しています。この構造により、銅原子の拡散経路をより効果的に遮断できます。特に、高温下での銅拡散を抑制する能力が強化されます。
- 窒素原子が金属原子の間に侵入することで、格子間隙を埋め、銅原子が通り抜けるのを防ぐ「トラップ」のような役割を果たします。
熱安定性の向上
- 窒化物は、純粋な金属に比べて一般的に融点が高く、熱安定性に優れています。半導体製造プロセスでは、配線形成後に様々な熱処理(アニールなど)が行われるため、高温に耐えうるバリア層が不可欠です。窒化物はこれらの熱処理によっても構造が安定し、バリア機能が維持されます。
化学的安定性の向上
- 窒化物は、純粋な金属よりも化学的に不活性であり、周囲の材料(特に絶縁膜)との不要な反応を抑制します。これにより、インターフェースの安定性が保たれ、デバイスの信頼性が向上します。
密着性の改善
- 特定の窒化物は、その上の金属配線(特に銅)や、下のシリコン基板、または層間絶縁膜との密着性を向上させる効果があります。これにより、配線の剥離や層間の界面欠陥の発生を抑制し、デバイスの信頼性を高めます。
エレクトロマイグレーション(EM)耐性の向上
- 窒化バリアメタルは、銅配線のEM耐性向上にも寄与すると考えられています。EMは、高電流密度下で金属原子が移動し、配線の断線やショートを引き起こす現象ですが、バリア層が銅の移動を抑制することで、この現象を緩和する効果が期待されます。
このように、窒化物は純粋な金属に比べて、バリア機能、熱安定性、化学的安定性、密着性、信頼性といった点で優れており、特に微細化が進む現代の半導体デバイスにおいて、不可欠な材料となっています。
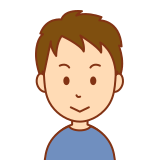
窒化物(TaN, TiNなど)は、純粋な金属より緻密で安定した構造を持つため、銅の拡散をより効果的に防ぎます。また、高い熱的・化学的安定性や密着性、エレクトロマイグレーション耐性向上効果があり、デバイス信頼性確保に不可欠です。
窒化物に原子構造がより緻密で安定する理由は何か
窒化物が純粋な金属と比較して、原子の構造がより緻密で安定する主な理由は、金属原子と窒素原子間の強力な化学結合と、それによる結晶構造の変化にあります。
- 共有結合性の寄与:純粋な金属は主に金属結合によって成り立っていますが、金属窒化物、特に遷移金属窒化物(TaN, TiNなど)では、金属原子と窒素原子の間に共有結合性の性質が強く加わります。窒素原子は電気陰性度が高く、金属原子から電子を引きつけ、共有結合的な特性を持つ結合を形成します。この共有結合は非常に強く、結晶全体をより安定させます。
- 侵入型構造(Interstitial Compound)の形成:多くの遷移金属窒化物では、比較的小さな窒素原子が、金属原子が形成する結晶格子の隙間(八面体型などの侵入サイト)に入り込む「侵入型化合物」を形成します。この窒素原子の侵入によって、金属原子間の結合が強化されたり、結晶構造全体のパッキング(充填)密度が高まったりします。結果として、より堅固で緻密な構造が形成されます。
- 結合エネルギーの増加:金属原子と窒素原子間の強力な結合(金属結合、共有結合、一部イオン結合の混在)によって、結晶全体の結合エネルギーが増加します。結合エネルギーが高いということは、その構造がより安定していることを意味し、外部からのエネルギー(熱など)に対して分解しにくいことを示します。これにより、高い融点や熱安定性が得られます。
- 結晶欠陥の低減と安定化:窒素原子の存在は、金属単体で生じやすい特定の結晶欠陥(空孔など)を埋める効果を持つこともあります。また、窒素原子が格子内に適切に配置されることで、結晶構造全体がより安定したエネルギー状態を取りやすくなります。
これらの要因が複合的に作用し、窒化物は純粋な金属単体よりも原子の動きが制限され、全体としてより緻密で熱的・化学的に安定した構造を形成するのです。
この安定性が、半導体バリア層としての優れた特性(銅拡散防止能力、熱安定性、化学的安定性など)に繋がっています。
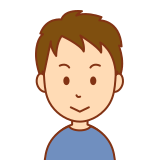
窒化物は、金属原子と窒素原子が共有結合性の強い結合を形成し、窒素原子が金属格子の隙間に入り込むことで、より強く密な結晶構造を形成します。これにより、結合エネルギーが増加し、純粋な金属より熱的・化学的に安定します。
タンタルと窒化タンタルの使い分けは
半導体前工程のバリアメタルとして、タンタル単体(Ta)と窒化タンタル(TaN)は、それぞれの特性を活かして使い分けられています。多くの場合は、両者を積層して使用することで、それぞれの利点を最大限に引き出す形がとられています。
タンタル単体(Ta)
- 特性:
- 低い抵抗率: 純粋な金属であるため、窒化物に比べて電気抵抗が低いです。これは、配線全体の抵抗を抑える上で有利です。
- 銅(Cu)との密着性: 銅との密着性が比較的良好です。
- 比較的良好なバリア性: ある程度の銅拡散防止能力は持っていますが、窒化物に比べると限定的です。
- 主な役割・使い方:
- シード層への密着層: 銅めっきの前に形成される銅シード層(めっきの下地となる薄い銅膜)との密着性を高めるために、TaN層の上にTa層を形成することがあります。TaNとCuの直接的な密着性はそこまで高くないため、間にTaを挟むことでより安定した界面を形成します。
- バリア層の一部: 他の層と組み合わせることで、バリア層全体の一部として機能します。
窒化タンタル(TaN)
- 特性:
- 優れた銅拡散防止能力: 窒素原子が金属格子に侵入することで、原子構造がより緻密で安定するため、銅原子の拡散を非常に効果的に遮断します。高温下でのバリア性も優れています。
- 高い熱安定性: 高温プロセスを経ても構造が安定し、バリア機能が維持されます。
- 化学的安定性: 周囲の絶縁膜などと反応しにくいです。
- エレクトロマイグレーション(EM)耐性向上: 銅配線のEM耐性向上に寄与します。
- 抵抗率: 純粋なTaに比べて抵抗率は高いです。
- 主な役割・使い方:
- 主要な銅拡散バリア層: 銅がシリコンや絶縁膜に拡散するのを防ぐ「主たる壁」として機能します。ビアホールや配線トレンチの内壁に直接、または下地層を介して形成されます。
タンタル単体と窒化タンタルの使い分け(積層構造)
現在の先端プロセスでは、多くの場合、以下のようなTa/TaNの積層構造が採用されています。
- 層間絶縁膜 (ILD)
- TaN層 (拡散バリア機能の主役): まず、ILDと銅の間に、高い銅拡散防止能力を持つTaN層を成膜します。これが銅の拡散を防ぐ主要なバリアです。
- Ta層 (密着性向上、抵抗低減): TaN層の上に、純粋なTa層を薄く成膜します。このTa層は、その上に形成される銅シード層(および最終的な銅配線)との密着性を高める役割を果たします。また、TaNよりも抵抗が低いため、バリア層全体の抵抗をわずかながら低減する効果も期待できます。
- 銅シード層
- 銅配線(めっき充填)
この積層構造により、TaNの優れたバリア性とTaの良好な密着性・低抵抗性という両方の利点を同時に得ることができます。
まとめると、タンタル単体は主にその低抵抗性と銅への密着性を活かし、窒化タンタルは優れた銅拡散防止能力と熱安定性を活かして、それぞれが異なる役割を担いながら協調して機能していると言えます。
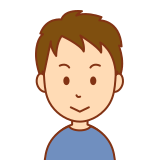
タンタル単体(Ta)は低抵抗で銅との密着性が良く、主に下地やシード層との接着に利用されます。一方、窒化タンタル(TaN)は優れた銅拡散バリア性と熱安定性を持つため、主要な拡散防止層として使われます。多くの場合、両者を積層し、それぞれの利点を活かします。
コメント