この記事で分かること
- 金属積層造形とは:金属3Dプリンターとも呼ばれ、金属粉末やワイヤーを材料として、層ごとに金属部品を造形する装置です。
- 利点は:複雑形状や中空構造なども一体で作ることができるため、軽量化が可能であり、少量多品種に対応しやすいという利点があります。
- どのような種類があるのか:レーザー粉末床溶融結合法、指向性エネルギー堆積法、バインダージェッティングなどがあります。
金属積層造形の実用化加速
工作機械各社が金属積層造形(AM)機事業を加速していることがニュースになっています。
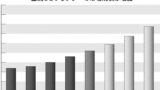
軽量化、短納期、小ロット生産、設計自由度の向上といったメリットがあるものの、試作にとどまっていた部分が多かった事業ですが、実用に向けた動きが加速しています。
金属積層造形機とは何か
金属積層造形機とは一般的に「金属3Dプリンター」や「金属AM(Additive Manufacturing)」とも呼ばれ、金属粉末やワイヤーを材料として、層ごとに金属部品を造形する装置です。
従来の切削加工とは異なり、材料を付加していくため、複雑形状や中空構造なども一体で作ることができます。
金属積層造形機の用途としては、航空宇宙、医療(インプラント)、自動車、金型製作などがあり、軽量化、短納期、小ロット生産、設計自由度の向上といったメリットがあります。
一方で、装置や材料コストの高さ、造形後の後処理(サポート除去や熱処理)が必要、品質管理が難しいといった課題もあります。
造形を行う方法によって以下のように分類されています。
レーザー粉末床溶融結合法(LPBF, Laser Powder Bed Fusion)
- 粉末状の金属を薄く敷き、レーザーで選択的に溶融・凝固。
- 代表機種:EOS, SLM Solutions, Trumpf など。
- 精密で高密度な部品が可能だが、造形サイズに制限あり。
電子ビーム粉末床溶融結合法(EBM, Electron Beam Melting)
- 電子ビームで粉末を溶融。
- 高真空中での造形で酸化しにくい。
- 代表機種:Arcam(GE Additive)。
指向性エネルギー堆積法(DED, Directed Energy Deposition)
- ノズルから金属粉末やワイヤーを供給しながらレーザーや電子ビームで溶融。
- 大型部品や補修用途に適する。
- 代表機種:Optomec, DMG Mori, Trumpf。
バインダージェッティング → 焼結(金属バインダージェッティング)
- 粉末にバインダーをインクジェットで吹き付けて形状を作り、後に焼結。
- 比較的低コストで高速。
- 代表機種:Desktop Metal, ExOne。
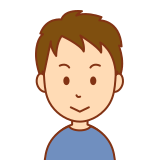
金属積層造形機とは金属粉末やワイヤーを材料として、層ごとに金属部品を造形する装置です。複雑形状や中空構造なども一体で作ることができるため、軽量化が可能であり、少量多品種に対応しやすいという利点があります。
レーザー粉末床溶融結合法はどのような仕組みか
レーザー粉末床溶融結合法(LPBF: Laser Powder Bed Fusion) は以下のような工程で造形が進みます:
1. 粉末敷き
- 金属粉末を薄い層(20~100ミクロン程度)で造形エリアに均一に敷きます。
- リコーター(ブレードやローラー)が使われます。
2. レーザー照射・溶融
- CADデータを基に、必要な箇所に 高出力レーザー(通常はファイバーレーザー) を走査。
- 照射された粉末が局所的に溶けて凝固し、固体の金属層が形成されます。
- 1層ごとにこの工程を繰り返します。
3. 層の積み重ね
- 造形プラットフォームが 1層分下降 し、再び新しい粉末が敷かれます。
- 同じようにレーザーで選択的に溶融。
- このプロセスを繰り返して、3D構造を積み上げていく。
4. 完成後の冷却・取り出し
- 造形終了後、冷却。
- ビルドプレート(造形台)から切り離し、サポート材を除去。
- 必要に応じて熱処理(応力除去焼鈍など)を行います。
技術ポイント
- 造形中は 不活性ガス(アルゴンや窒素) を充填して酸化防止。
- レーザーの出力、走査速度、ピッチ(スキャン間隔)、粉末の粒径などが重要なパラメータ。
- 基本的に 100%に近い緻密な金属組織 が得られます。
この方式の特徴は、非常に高い精度(±0.05~0.1mm程度)、微細なディテール再現、高密度が可能なことです。ただし、造形サイズや速度、使用可能な材料には制限があります。
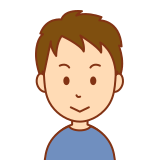
レーザー粉末床溶融結合法では、必要な箇所に 高出力レーザー を走査し、粉末が局所的に溶けて凝固し、固体の金属層が形成されます。
指向性エネルギー堆積法の仕組みは
指向性エネルギー堆積法(DED: Directed Energy Deposition)」の仕組みは以下のようなものです。
DEDの基本仕組み
- 材料供給
- 金属粉末 または 金属ワイヤー をノズルから直接供給。
- ノズルは通常、造形ヘッドに取り付けられ、ロボットアームやガントリーで移動。
- エネルギー照射(レーザー、電子ビーム、プラズマアーク)
- ノズル先端近くで、レーザーや電子ビーム、プラズマアーク などの高エネルギー源を材料供給点に照射。
- 照射ポイントで供給された金属が即座に溶融。
- 溶融池形成と堆積
- 溶けた金属が冷えて固まることで層を形成。
- 溶融池がノズルの移動に合わせて移動し、造形物が一筆書きのように成長。
- 造形物の成長
- レイヤーごとに積み上げるのではなく、リアルタイムで連続的に材料を供給・溶融・凝固 しながら成形。
- 必要に応じてノズルの高さや角度を調整して立体的に形状を構築。
DEDの特徴
- 粉末床方式(LPBF)よりも 大きな部品 が作れる(1m超の造形も可能)。
- 既存の金属部品の上に直接造形(肉盛り修理など) できる。
- 精度はLPBFほど高くないが、造形速度が速く、材料無駄が少ない。
- 使用材料:ステンレス、チタン、ニッケル合金、工具鋼など。
用途の一例
- 航空機エンジンのブレード修理
- 大型構造物の肉盛り補修
- 大型・中空構造の一体造形
- 金型の局所強化
レーザーDEDの場合、レーザーがエネルギー源なので、ビームの焦点調整やガスによる溶融池の保護(シールドガス) も重要な要素になります。
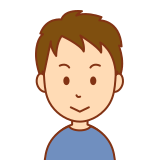
指向性エネルギー堆積法は金属源をノズルから供給し、高エネルギー源を材料供給点に照射することで、金属が溶融し、冷えて固まることで層を形成する仕組みです。
バインダージェッティングの仕組みは
バインダージェッティング(Binder Jetting)は粉末を接着剤(バインダー)で固める方式で、他の金属積層造形技術とはプロセスが大きく異なります。
他の金属積層造形法と比べると、設備コストが比較的低く、スケーラビリティに優れますが、機械的強度や精度で劣る場合があるのが課題です。
バインダージェッティングの基本的な仕組み
- 粉末敷き
- 造形ベッドに金属粉末(またはセラミック粉末など)を薄い層(約50~100μm)で均一に敷きます。
- リコーター(ブレードやローラー)を使って層を平らにします。
- バインダー噴射
- インクジェットプリンタのようなヘッドから、必要な部分に液体バインダー(接着剤)を噴射。
- バインダーが粉末を部分的に接着し、グリーンパーツ(仮成形体)」が作られます。
- 層の積み重ね
- 造形プラットフォームが1層分下降。
- 新しい粉末を敷き、再びバインダーを噴射。
- このプロセスを繰り返して立体を構築。
- 乾燥
- 造形後、バインダーを乾燥させ、グリーンパーツを安定化。
- 脱脂・焼結
- 乾燥後、脱脂工程(バインダーを燃焼除去)を行い、バインダーを取り除く。
- その後、高温で焼結して金属粉末を融着させ、最終的な高密度の金属部品に仕上げる。
バインダージェッティングのポイント
- レーザーや電子ビームによる局所的溶融がない → 造形時の熱ひずみや残留応力が少ない。
- 専用の後処理(焼結)が必要 → 焼結時に10~20%程度の収縮が起きるため、それを見込んだ設計が必要。
- サポート構造が不要な場合が多い(未使用の粉末が造形物を支える)。
特徴とメリット
- 造形速度が非常に速い → インクジェット技術に基づくため、大面積でも短時間で造形。
- 材料無駄が少ない → 未使用粉末は再利用可能。
- 複雑形状、大量生産向き → 工業用途だけでなくジュエリーやアート分野でも利用。
- 表面粗さや密度は他方式に劣る → 焼結後に追加の後処理(浸炭処理やHIP)が必要な場合がある。
用途の一例
- 金型インサート
- 中空構造や複雑なパーツ
- 多孔質金属フィルター
- 低コストの小~中ロット金属部品
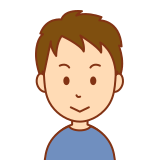
金属粉末を薄い層(約50~100μm)で均一に敷き、必要な部分に液体バインダー(接着剤)を噴射します。バインダーが粉末を部分的に接着し、仮成形体が作られ、バインダーの除去と金属の高温で融着させることで金属の層を形成しています。
コメント