この記事で分かること
- スパッタリングとは:真空中で不活性ガスをイオン化させ、生成したイオンをターゲット(に衝突させます。この衝突エネルギーにより、ターゲット原子が弾き飛ばされ、基板上に堆積して薄膜を形成する技術です。
- 特徴は:高い密着性、緻密な膜の形成が可能、金属だけでなく、合金、酸化物、窒化物など、様々な材料の薄膜を形成できる、安定性が高いなどの特長があります。
スパッタリングによる成膜
半導体の重要性が増す中で、前工程装置は世界的に成長が続いています。
https://optronics-media.com/news/20250414/99245/
特に中国は米中対立もあり、大幅な投資増加が続いています。今後も先端技術を駆使した半導体の需要増加と従来技術による成熟プロセスともにその重要性は増加するとみられています。
今回は前工程の成膜工程の方法のひとつであるスパッタリングの解説となります。
半導体の前工程とは
半導体の前工程とは、シリコンウェハ上にトランジスタや配線などの微細な回路を形成する一連のプロセスのことです。ウェハを素材として、集積回路を作り込んでいく、半導体製造の最も重要な部分と言えます。非常に多くの精密な工程を経て、最終的な半導体チップの機能が決まります。
主な前工程は以下の通りです。
ウェハ準備
シリコンインゴットの製造: 高純度のシリコンを溶解し、種結晶を用いて単結晶のシリコンインゴットを育成します。
- スライス: インゴットを薄い円盤状(ウェハ)にスライスします。
- 研磨: ウェハ表面を平坦かつ滑らかに研磨します。
- 洗浄: ウェハ表面の微細な異物や汚れを徹底的に除去します。
成膜
ウェハ表面に、酸化膜、窒化膜、金属膜など、様々な薄膜を形成します。
- 成膜方法には、CVD(化学気相成長法)、スパッタリング(物理気相成長法)、ALD(原子層堆積法)などがあります。
フォトリソグラフィ
ウェハ表面に感光材(フォトレジスト)を塗布します。
- 回路パターンが描かれたマスク(フォトマスク)を通して紫外線を照射し、レジストにパターンを焼き付けます。
- 現像液で不要なレジストを除去し、ウェハ上に回路パターンを形成します。
エッチング
フォトリソグラフィでパターン形成されたレジストをマスクとして、露出した成膜を除去し、ウェハに回路パターンを転写します。
- エッチングには、液体を用いるウェットエッチングと、プラズマを用いるドライエッチングがあります。
不純物導入(ドーピング)
半導体特性を持たせるために、リンやボロンなどの不純物をウェハ中に注入します。
- イオン注入法などが用いられます。
平坦化(CMP: Chemical Mechanical Polishing)
表面の凹凸をなくし、平坦にするための処理です。
- 化学的な腐食と механическая研磨を同時に行います。
配線形成(メタライゼーション)
形成されたトランジスタなどの素子間を金属配線で接続します。
- スパッタリングなどで金属膜を形成し、フォトリソグラフィとエッチングで配線パターンを作ります。
これらの工程を何度も繰り返し行うことで、複雑な集積回路がウェハ上に形成されます。前工程は、半導体の性能や品質を大きく左右する、非常に重要なプロセスです。
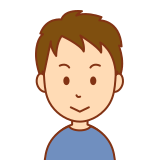
前工程は、細な回路を形成する一連のプロセスのことで、半導体の性能や品質を大きく左右する、非常に重要なプロセスです。
スパッタリング(物理気相成長法)とは何か
スパッタリングは、真空中で行われる物理気相成長(PVD)法の一種であり、半導体デバイスの製造において、薄膜を形成するための重要な技術の一つです。
スパッタリングの原理
- 真空チャンバー: 装置内は高真空状態に保たれます。
- プラズマ生成: アルゴンなどの不活性ガスを導入し、ターゲット(成膜材料)と基板(シリコンウェハなど)の間に電圧を印加します。これにより、ガスがイオン化されプラズマが発生します。
- ターゲットへのイオン衝突: プラズマ中のイオンがターゲットに高速で衝突します。
- スパッタリング現象: 衝突のエネルギーにより、ターゲットを構成する原子や分子が弾き飛ばされます。この現象がスパッタリングと呼ばれます。
- 薄膜形成: 弾き飛ばされたターゲット原子や分子が基板表面に堆積し、薄い膜を形成します。
例えるなら、真空の部屋の中で、ボール(イオン)を壁(ターゲット)に勢いよくぶつけると、壁の塗料(ターゲット原子)が剥がれ落ちて、近くにある板(基板)に付着するようなイメージです。
スパッタリングの特徴と半導体製造における利点
- 高い密着性: ターゲットから弾き出された粒子は高いエネルギーを持っているため、基板に強固に密着した膜を形成できます。
- 緻密な膜質: 形成される膜は密度が高く、均一性に優れています。ナノスケールの薄膜を精密に制御できるため、微細化が進む半導体デバイスの製造に不可欠です。
- 多様な材料に対応: 金属だけでなく、合金、酸化物、窒化物など、様々な材料の薄膜を形成できます。融点の高い材料や、複数の元素からなる化合物でも組成を維持したまま成膜が可能です。
- 成膜プロセスの安定性: プロセスパラメータを精密に制御することで、膜厚や膜質を高い精度で再現できます。
- 基板へのダメージが少ない: ターゲットを加熱する必要がないため、熱に弱い材料を基板に使用する場合にも適しています。
半導体製造でのスパッタリングの用途
- 金属配線: アルミニウム(Al)、銅(Cu)などの金属薄膜を形成し、デバイス内の電気信号の通り道を作ります。
- 電極形成: チタン(Ti)、白金(Pt)などの金属薄膜を用いて、トランジスタなどの電極を形成します。
- バリア膜: タンタル(Ta)、窒化チタン(TiN)などの薄膜を形成し、金属配線の拡散を防いだり、デバイスの信頼性を向上させたりします。
- 絶縁膜: 酸化シリコン(SiO₂)、窒化シリコン(Si₃N₄)などの薄膜を形成し、素子間の電気的な絶縁を行います。
- 透明導電膜: 酸化インジウムスズ(ITO)などの透明な導電性薄膜を形成し、タッチパネルやディスプレイなどに利用されます。
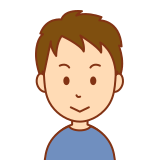
スパッタリングは真空中で不活性ガス(主にアルゴン)をイオン化させ、生成したイオンをターゲット(成膜材料)に衝突させます。この衝突エネルギーにより、ターゲット原子が弾き飛ばされ(スパッタリング現象)、基板上に堆積して薄膜を形成する技術です。
CVDとの比較
スパッタリングとCVDはそれぞれ異なる原理と特徴を持っており、形成したい薄膜の種類、求められる特性、基板の形状や材質などによって、最適な成膜方法が選択されます。
半導体デバイスの製造においては、複数の薄膜を様々な材料で形成する必要があるため、スパッタリングとCVDは相互に補完し合う重要な技術として活用されています。
スパッタリングとCVDの比較
特徴 | スパッタリング(PVD) | CVD(化学気相成長法) |
---|---|---|
成膜原理 | 物理的なスパッタリング現象 | 化学反応 |
原料 | 固体ターゲット | 気体原料(前駆体) |
エネルギー源 | イオン衝突の運動エネルギー | 熱、プラズマ、光など |
成膜温度 | 低温~比較的低温 | 低温~高温(プロセスによる) |
膜の組成 | ターゲットの組成を反映 | 原料ガスの化学反応により制御 |
密着性 | 良好 | 非常に良好(化学結合による) |
段差被覆性 | 比較的悪い(直線的な堆積) | 良好~非常に良好(コンフォーマル成膜性) |
膜の純度 | 比較的高い | 高い(反応条件による) |
成膜速度 | 比較的遅い~速い(マグネトロンスパッタなど) | 比較的速い~遅い(プロセスによる) |
装置の複雑さ | 比較的単純 | 比較的複雑 |
材料の多様性 | 広い | 比較的広い(適切な前駆体が必要) |
主な用途 | 金属配線、電極、バリア膜など | 絶縁膜、保護膜、半導体薄膜、化合物半導体など |
安全性・環境 | 比較的安全、有害物質の使用が少ない | 原料ガスによっては毒性・可燃性があり、安全管理が必要 |
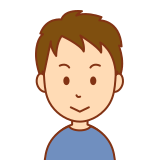
スパッタリングとCVDはそれぞれに特徴をもつ成膜方法であり、相互に補完し合う重要な技術として活用されています。
スパッタリング装置はどのような構成なのか
一般的なスパッタリング装置は、主に以下の要素で構成されています。
- 真空チャンバー: 内部を高真空に保つための容器。
- 真空ポンプ: チャンバー内を排気し、高真空状態を作り出すための装置。
- ターゲット: 成膜材料となる固体。通常、チャンバー内のカソード(陰極)に取り付けられます。
- 基板ホルダー: シリコンウェハなどの基板を固定するための機構。アノード(陽極)またはその近傍に配置されます。
- 電源: プラズマを生成し、イオンを加速するための高電圧電源。直流(DC)電源や高周波(RF)電源などが用いられます。
- ガス導入系: スパッタリングに必要なアルゴンなどの不活性ガスをチャンバー内に導入するシステム。
- 排気系: スパッタリング中に発生する不要なガスや反応生成物を排気するシステム。
- 制御系: スパッタリングプロセス全体を制御するためのコンピューターシステムやセンサー類。
- マグネトロン: 磁石を利用してプラズマをターゲット近傍に閉じ込め、スパッタリング効率を高めるための機構(マグネトロンスパッタリングの場合)
有名な装置はメーカーどこか
これらのメーカーは、半導体製造だけでなく、様々な産業分野向けにスパッタリング装置を提供しています。
主要なスパッタリング装置メーカー
- アプライドマテリアルズ (Applied Materials):アメリカの大手半導体製造装置メーカーで、スパッタリング装置においても世界的なシェアを持っています。
- アルバック (ULVAC):日本の総合真空機器メーカーで、スパッタリング装置においても幅広いラインナップを提供しています。半導体向けだけでなく、FPD、電子部品、一般産業向けなど多様な用途に対応しています。
- キヤノンアネルバ (CANON ANELVA):キヤノン株式会社のグループ会社で、真空技術と薄膜形成技術を核に、スパッタリング装置をはじめとする半導体製造装置を提供しています。
- 東京エレクトロン (Tokyo Electron):日本を代表する半導体製造装置メーカーであり、成膜装置の一つとしてスパッタリング装置も提供しています。
- KOKUSAI ELECTRIC (国際電気):こちらも日本の大手半導体製造装置メーカーで、枚葉式ALD装置などで強みがありますが、スパッタリング装置も手掛けています。
- SCREENホールディングス (SCREEN Holdings):洗浄装置などで有名ですが、スパッタリング装置も提供しています。
- 芝浦メカトロニクス (Shibaura Mechatronics):半導体製造装置、FPD製造装置などを手掛けており、スパッタリング装置もラインナップにあります。
- パナソニック プロダクションエンジニアリング (Panasonic Production Engineering):パナソニックの生産技術部門が独立した会社で、スパッタリング装置の開発・製造を行っています。
- 株式会社昭和真空 (Showa Shinku):真空蒸着装置やスパッタリング装置などの真空技術応用装置を専門に製造・販売している日本のメーカーです。
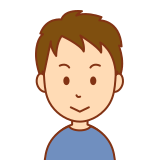
多くのメーカーが装置を提供しています。特にアプライドマテリアルズやアルバックのシェアが高いといわれています。
コメント